“The approach should be to minimise concrete and steel” says Lasse Lind
Mass timber could become a key tool in reducing waste from the construction industry, GXN partner Lasse Lind tells Dezeen in this interview for our Timber Revolution series.
GXN was founded in 2007 as the research arm of Copenhagen-based architecture studio 3XN.
GXN looks at circular and low-carbon design, behavioural design – including the social aspect of buildings – and technologies that can help the industry transition to a more sustainable future.
Use of timber “exploded”
Its use of timber has “exploded” recently, with around half of its buildings now having a significant element of wood in their structure, up from almost none five years ago, Lind said.
“We’ve always been very interested in materials and material technology,” Lind told Dezeen.
“Our material focus has evolved to change over the years and now we’re extremely focused on recyclability, recycled content, low-carbon, natural biogenic materials – that is our absolute focus.”
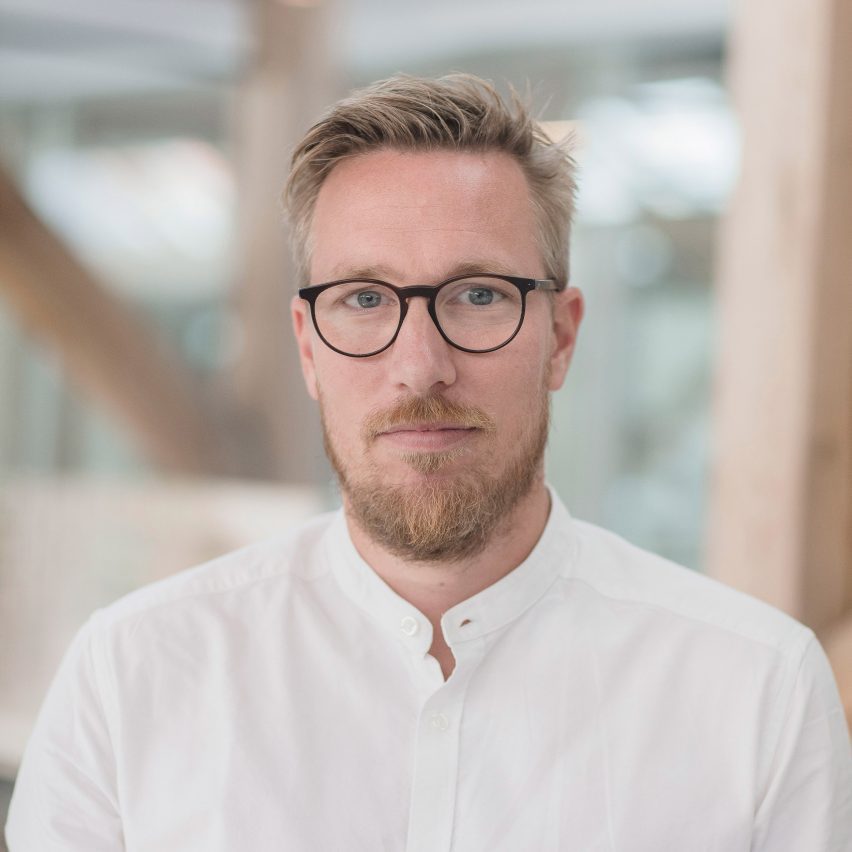
The majority of the studio’s work at the moment is in mass timber, which Lind says has many advantages over other building materials.
“The first one is obviously lower carbon, which is a big advantage, and the fact that it’s kind of regenerative as a material,” he said.
“There are other aspects as well, which are related to build-ability,” he added. “Timber tends to be lighter than, for example, concrete construction. So you need less transport and, in principle, fewer crane lifts.”
Timber helps you “close the loop on waste”
The fact that everything is prefabricated when it comes to mass-timber construction also means it is possible to work with more precise tolerances and cut down on waste, according to Lind.
In a recent project, a full-timber hotel extension on the island of Bornholm, Denmark, the studio even used offcuts from the cross-laminated timber (CLT) used for the building to create furniture and furnishings.
“You don’t have a lot of waste, potentially, in the production,” he said. “Especially if you think about it like we did in the prototype on Bornholm, where we used all the offcuts for furniture – you can actually close the loop on waste in the production chain a bit.”
Construction waste currently accounts for more than a third of all waste generated in the EU.
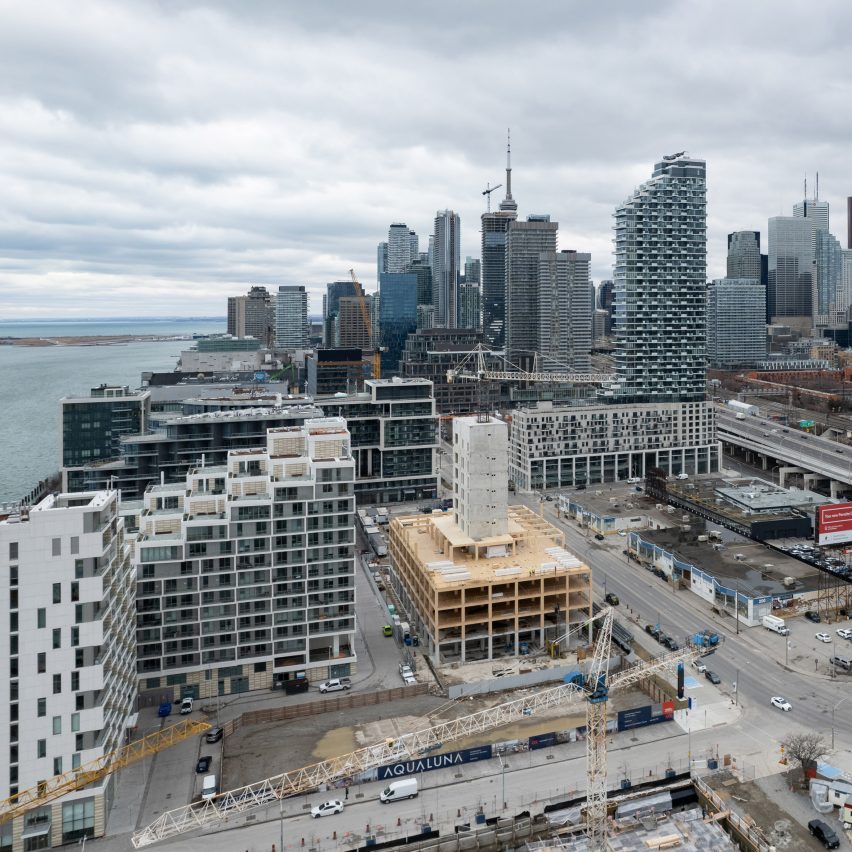
As part of its research in this area, GXN is also experimenting with using offcuts from CLT boards as slabs in its buildings.
“You would have to live with the fact that it’s different thicknesses and you would have to look at the grid because if it’s offcut materials, you cannot get everything in eight metres,” he said.
“You have to have some substructure to accommodate a variety of sizes, so you need to spend a little bit more energy on the substructure but then you can actually use these offcuts as actual slabs.”
At the moment, the addition of concrete to the slabs is one of the things that makes it hard to design fully reversible timber buildings.
“In larger timber structures, where you have slabs, the standard practice is to cast everything out due to sound and vibration,” Lind explained.
“So essentially, if you have a timber slab, you cast a screed of concrete on top, and that actually messes up the reversibility of a lot of the structure,” he added.
GXN has attempted to create buildings that use alternatives to concrete slabs, including a version that saw the studio use egg crates filled with sand instead of the slabs.
“What we tried to do on the project on Bornholm is to have these crates and fill them with granite dust, waste production from granite, but the engineers wouldn’t sign off on it, unfortunately, so we weren’t able to do that for that project,” Lind said.
“But we are doing a building right now where we are getting rid of that concrete screed,” he continued.
“It’s something we’re always aware of when we’re building with timber – if we can get away from that detail, we’d like to, because it’s a small detail but it messes up the reversibility of the whole structure.”
Carbon budget “structures the discussion”
Lind believes that in the future, we will see a lot of hybrid timber systems as the industry figures out when wood is best to use.
“We [need to] figure out what timber is really good for, what concrete is really good for and what steel is really good for,” he said.
“The approach should be to minimise the use of concrete and steel, but there are just parts of a building where [those materials] makes more sense,” he added.
“I’m very interested that we use materials where they are best, and I think there are a lot of places where we could easily replace concrete or steel with timber.”
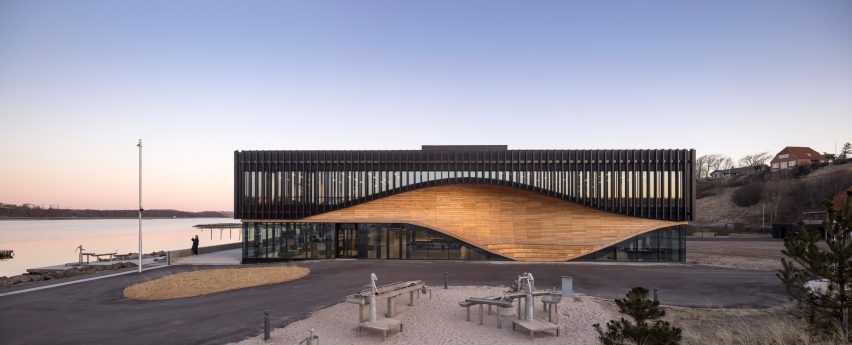
To help minimise carbon emissions, GXN sets carbon budgets for each of its projects that vary depending on the type of project and country it’s built in.
“The one thing we always try to do is bring a carbon budget, because it puts carbon up for discussion with every material choice and in that sense, it structures the discussion, like a financial budget does,” Lind said.
As timber buildings become more popular, Lind believes that as well as having an impact on carbon emissions, the material will also impact the way that buildings look, behave and feel.
“I think we will begin to explore, as designers, the vocabulary of what we can do, which I think will be very interesting,” he said.
“I don’t think it will be the same as architecture was 50 years ago when we kind of discovered the computer, but if you think about it, there are a lot of really creative half-timber buildings in Europe that have all kinds of weird ornaments and shapes and forms,” he added.
But though the use of timber and mass-timber is becoming more popular, there are still challenges facing architects when designing timber buildings. One of these is conveying the safety of the buildings to insurance companies.
“What we’re seeing as a challenge for timber buildings right now is generally insurance, because it’s a different material from what people usually use,” Lind said.
“We often find that insurers need to get on board and understand that it’s different. Because you can secure timber buildings, you can build them in a way where they are safe to operate and they’re safe as an asset, but there is a degree of scepticism from insurers.”
Designers should love timber’s “natural patina”
There are also sometimes regulatory difficulties as fire safety rules are often based on buildings made from steel or concrete.
“Inherently timber structures burn in a different way than steel or concrete does,” Lind said.
“And you can build safely with timber, but the way that you measure and regulate it needs to be different because it’s not steel,” he continued.
“Steel gets extremely hot and then it snaps, timber burns very slowly. It’s just a different strategy, fire-wise, that you need to apply.”
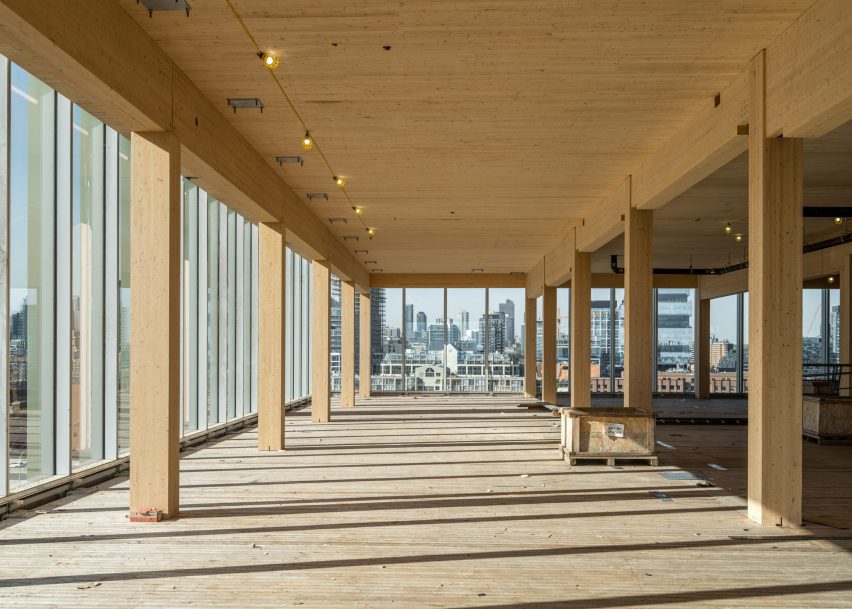
Architects and clients also need to get used to the fact that timber is a living material, which means it will change in ways that concrete and steel buildings might not, he argued.
“There’s a certain degree of natural patina that you should love as a designer,” Lind said.
“You should love the fact that it’s a material that changes over time – it’ll change colour, maybe have some cracks, it’s not going to look the same forever,” he added.
“So there’s some aesthetical considerations that you should be able to take your client through and understand that this is a living material and performs in a different way than an inorganic material.”
The architect believes that we’re only at the beginning of seeing the possibilities of timber and mass timber.
“There are loads of things that you could do even with fairly simple timber construction; there’s a whole field of investigation that we’re getting into which will be very interesting,” Lind concluded.

Timber Revolution
This article is part of Dezeen’s Timber Revolution series, which explores the potential of mass timber and asks whether going back to wood as our primary construction material can lead the world to a more sustainable future.