Puma reveals results of Re:Suede experiment to make biodegradable shoe
Sportswear brand Puma has said it is a step closer to launching a truly biodegradable shoe, following a trial in which a specially made version of its Suede sneakers decomposed under strict conditions.
In the Re:Suede experiment, 500 shoes were sent out to testers for six months of wear. Of those shoes, 412 were returned to Puma and sent to an industrial composting facility in The Netherlands, where they were mixed with other green waste and left to biodegrade.
After around three and a half months, a large proportion of the leather trainer had broken down sufficiently to be sold in The Netherlands as Grade A compost – a high-quality compost typically used on gardens and landscapes.
Slowing things down was the sole, which in the Re:Suedes was made of thermoplastic elastomer (TPE-E), a type of rubber. It took longer than the other components to break down into small enough pieces to be classified as compost, around six months.
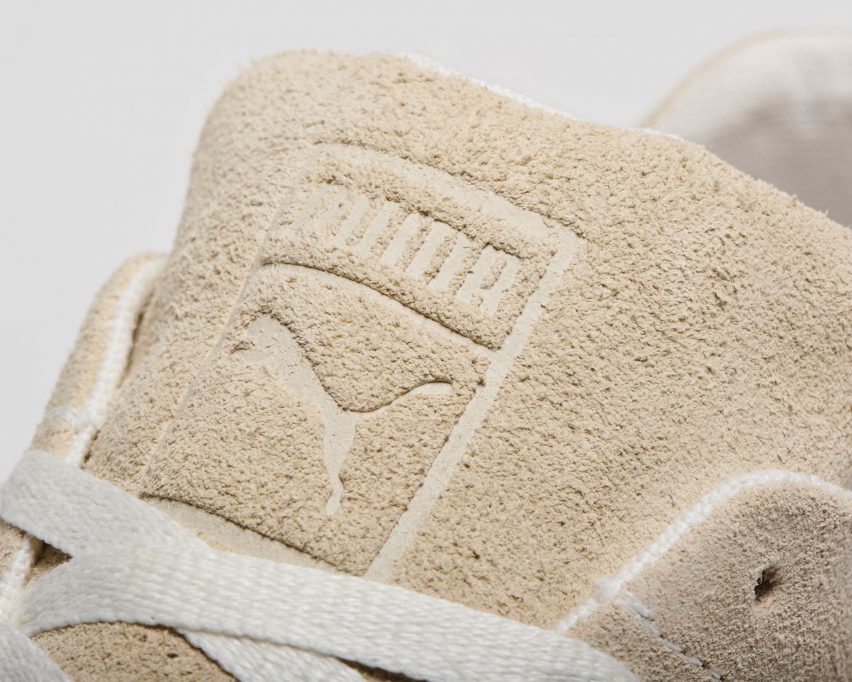
Puma is calling the Re:Suede experiment “successful” – with caveats. The longer timeframe required for the soles to break down is a deviation from standard operating procedures for industrial composting, so the shoes could not just be thrown into a household food waste collection.
However, Puma is hoping to launch a commercial version of the sneaker next year, incorporating a takeback scheme that would see it compost the shoe using its tailor-made process.
“While the Re:Suede could not be processed under the standard operating procedures for industrial composting, the shoes did eventually turn into compost,” said Puma chief sourcing officer Anne-Laure Descours.
“We will continue to innovate with our partners to determine the infrastructure and technologies needed to make the process viable for a commercial version of the Re:Suede, including a takeback scheme, in 2024.”

In a report of the experiment’s findings, Puma said it would pursue a “new business model in composting” that could support the decomposition of the shoe.
“The soles slow the process down, resulting in more composting cycles required to turn the shoe into Grade A compost, meaning they can’t be processed using today’s standard industrial composting operating procedures,” said the report.
“But with a new business model in composting and a higher volume of input into it, those standard operating procedures can change,” the report concluded. “There is a future for Re:Suede. To get there, we need more scale.”
Puma’s Re:Suede shoe is made of Zeology suede, which is tanned using a process based on zeolite minerals and free of chrome, aldehyde and heavy metals. Padding and laces are made of hemp, while the lining is made of a hemp-cotton blend.
For the composting process, Puma partnered with Dutch waste company Ortessa. The procedure involved shredding the shoe and placing the pieces into a composting tunnel – a unit where the temperature, humidity and oxygen levels are kept at optimal levels for bacteria to break down organic matter.
For the decomposing shoe granules to be considered small enough for compost, they had to be under 10 millimetres in size.
Those granules were periodically filtered out and sold as compost in The Netherlands.
The leftover pieces, 10 to 40 millimetres in size, became part of the “compost starter mix” and were combined with more green waste to continue decomposing. Ortessa estimated that the full shoe was turned into compost within approximately six months.
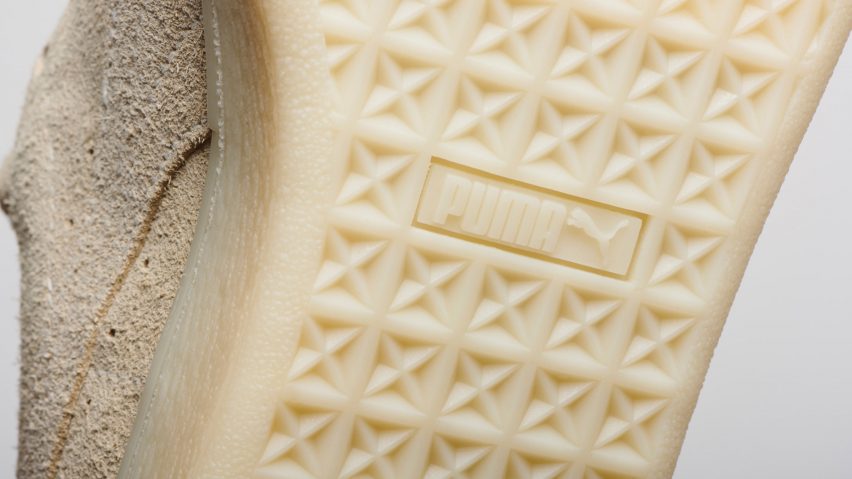
Re:Suede is Puma’s second attempt at launching a compostable shoe, with the first coming over a decade ago in the form of 2012’s InCycle collection.
Its Basket sneaker, which Puma said was fully compostable through industrial composting, was made of organic cotton and linen with a sole composed of a biodegradable plastic called APINATbio. The range was discontinued in 2014 and its failure blamed on poor consumer demand.
While several shoe designs have been marketed as biodegradable in recent years, the strict conditions required for them to actually break down are often not specified or the infrastructure not available. This can be seen as a kind of greenwashing.
Brands that have launched footwear described as biodegradable include Bottega Veneta with its sugarcane and coffee boots and Adidas with the uppers of its Futurecraft trainers.
A more experimental composition came from German designer Emilie Burfeind, whose compostable sneakers are made with a mushroom mycelium sole and a canine hair upper.