External Reference creates 3D-printed organic displays for La Manso store
3D-printed shelving structures informed by Catalan-modernist buildings were used for shelving in this store designed by External Reference for a Spanish jewellery brand.
Experimental jewellery designer Adriana Manso asked Carmelo Zappulla’s studio External Reference to develop a suitably unusual interior concept for her first physical store in the city.
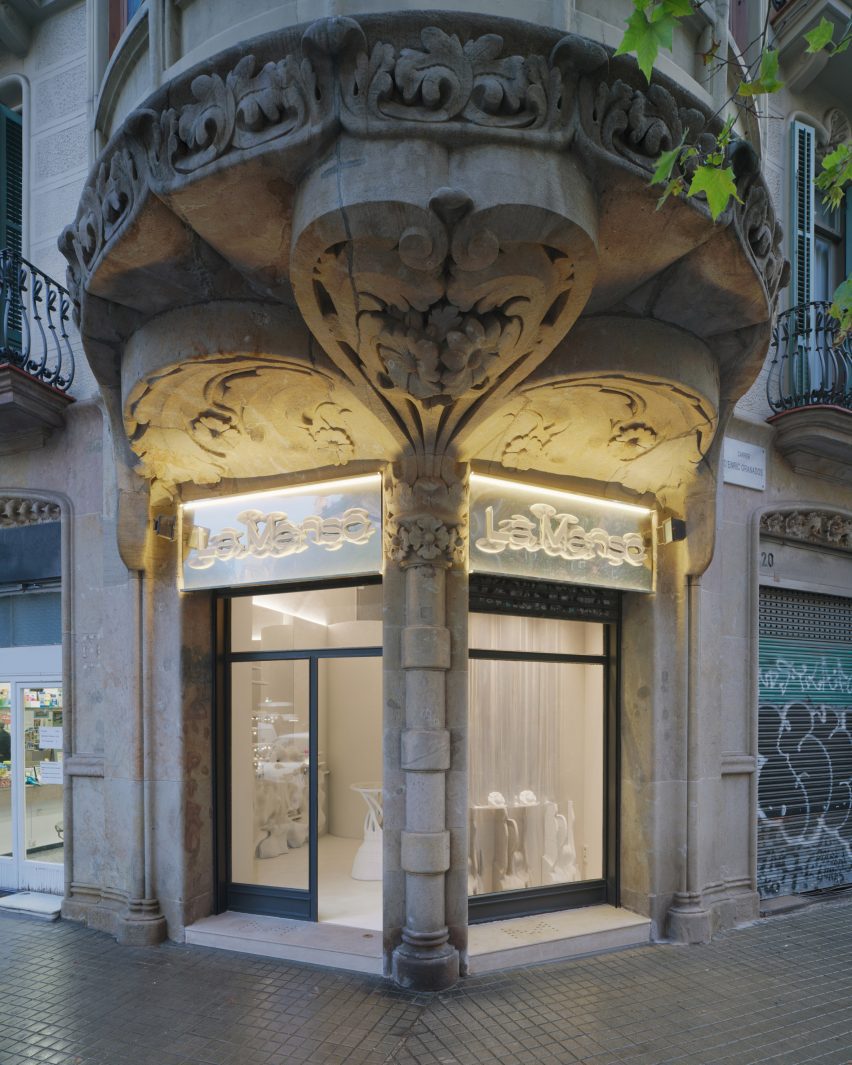
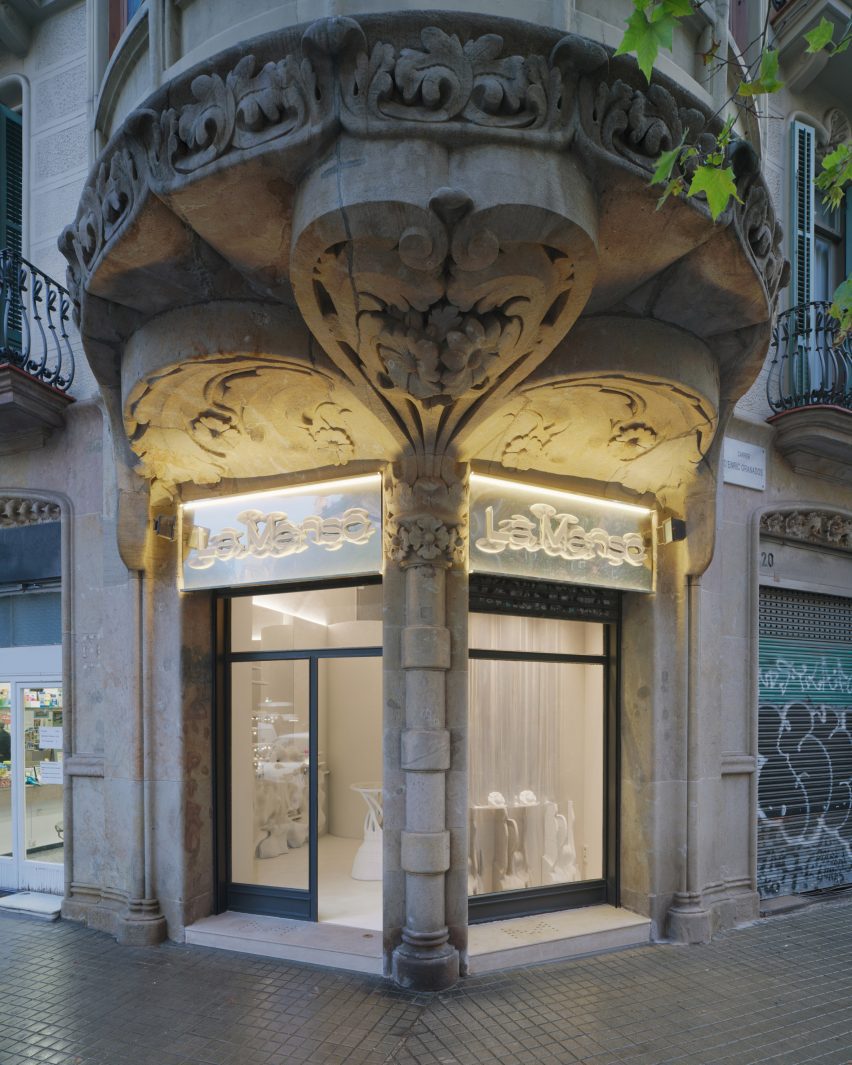
The project involved designing a window display and shelving for the 25-square-metre store, which is located in Barcelona’s Eixample district just a few metres from the house where Manso was born.
Manso is known for her playful pieces made from recycled plastic, which she wanted to display in a space that evokes the luxury feel of an haute-couture boutique.
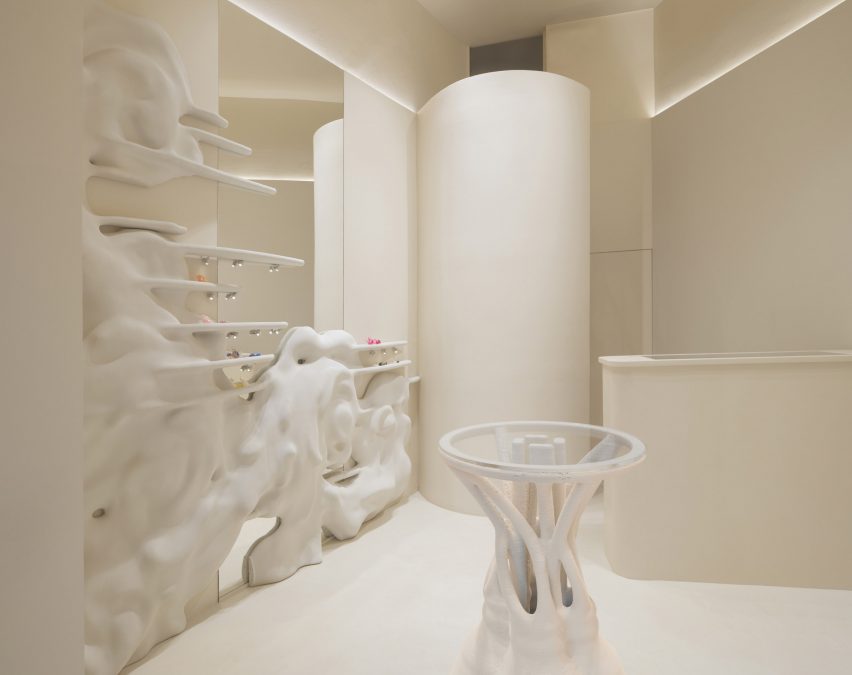
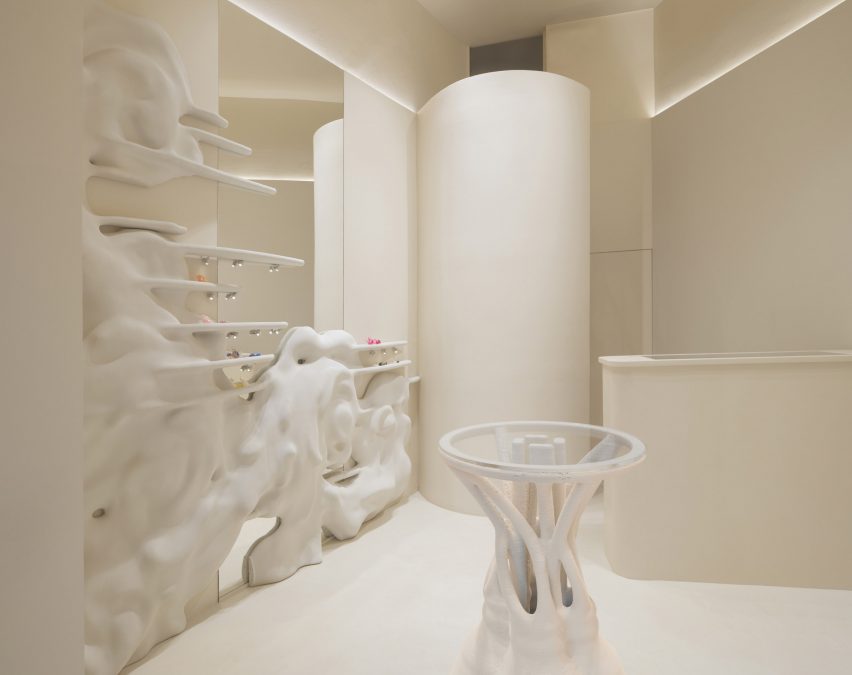
External Reference sought to combine the contemporary plasticity of La Manso’s jewellery with motifs influenced by Barcelona’s early 20th-century architecture, including the building in which the store is situated.
“Our design concept revolved around bringing the exterior facade inside, creating a melted and fluid background that would serve as an artistic canvas for showcasing the jewellery,” Zappulla told Dezeen.
“By blending the expressive elements of Catalan modernism with the organic forms inspired by La Manso design, our goal was to craft a visually captivating environment that elevates the overall shopping experience.”
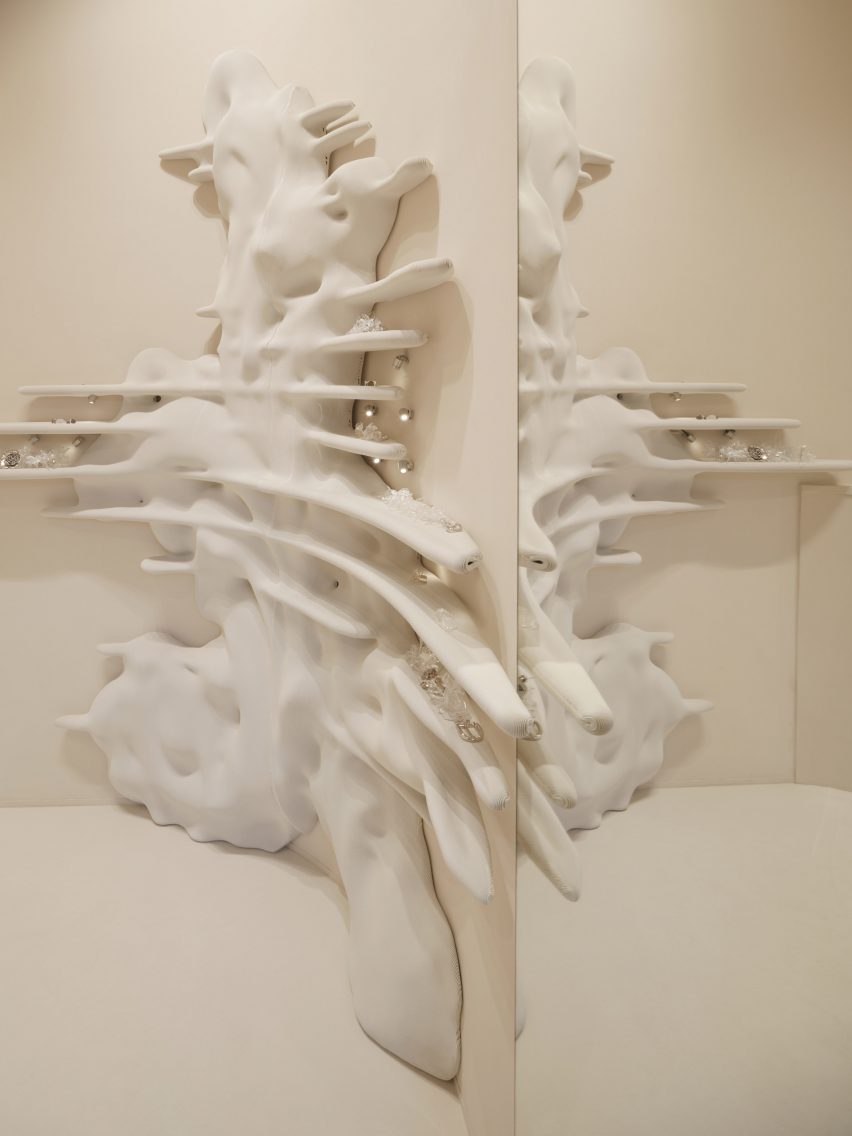
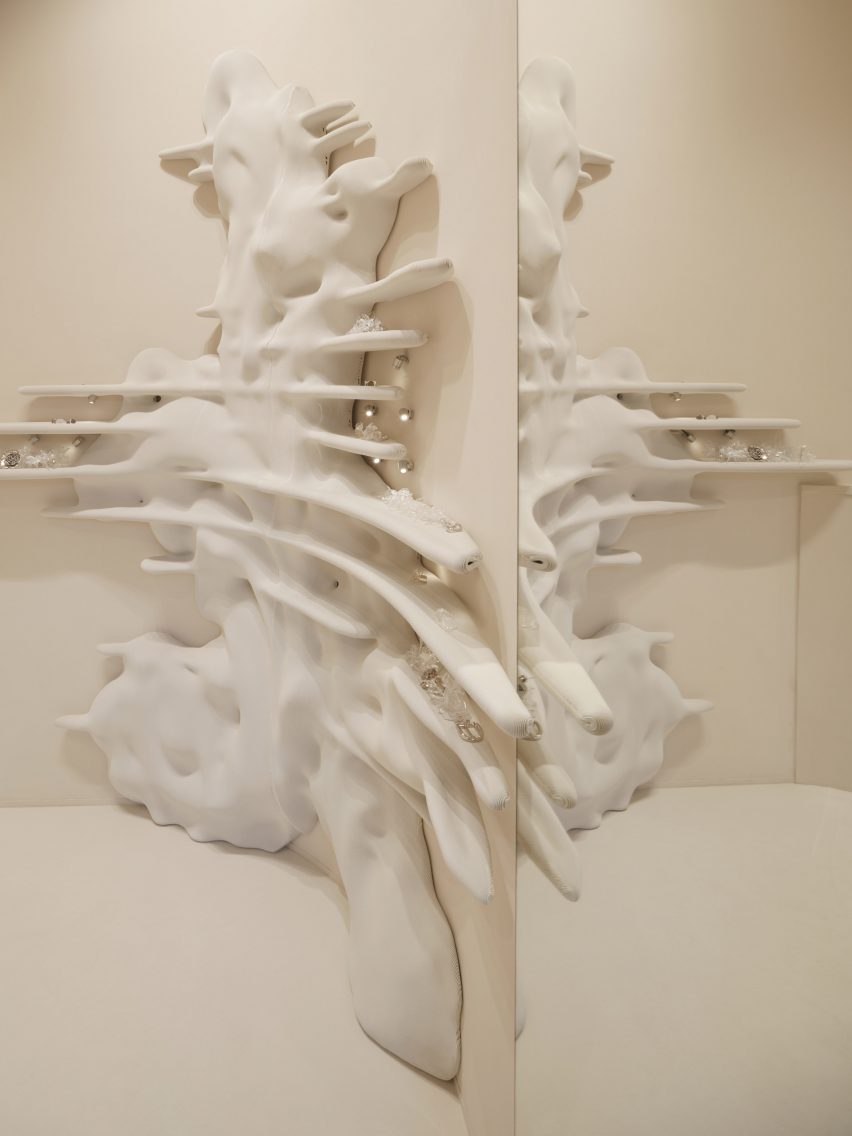
The designers selected fragments from the decorative facade and abstracted them using a process involving hand drawing and computational design techniques.
In particular, floral details from the elaborate canopy at the store’s entrance were reinterpreted as large rosettes incorporating futuristic glitches and bas-reliefs.
The organic shapes form shelving units that range in height from 90 centimetres to 1.7 metres. Jewellery and accessories are displayed on the shelves, as well as on a small table at the centre of the space.
The furniture is made from biodegradable cellulose and was produced with technical support from specialist 3D-printing workshop La Máquina.
Zappulla and his team refined the digital models to optimise them for printing. This involved splitting them into manageable parts that could be processed by the machine’s robotic arm.
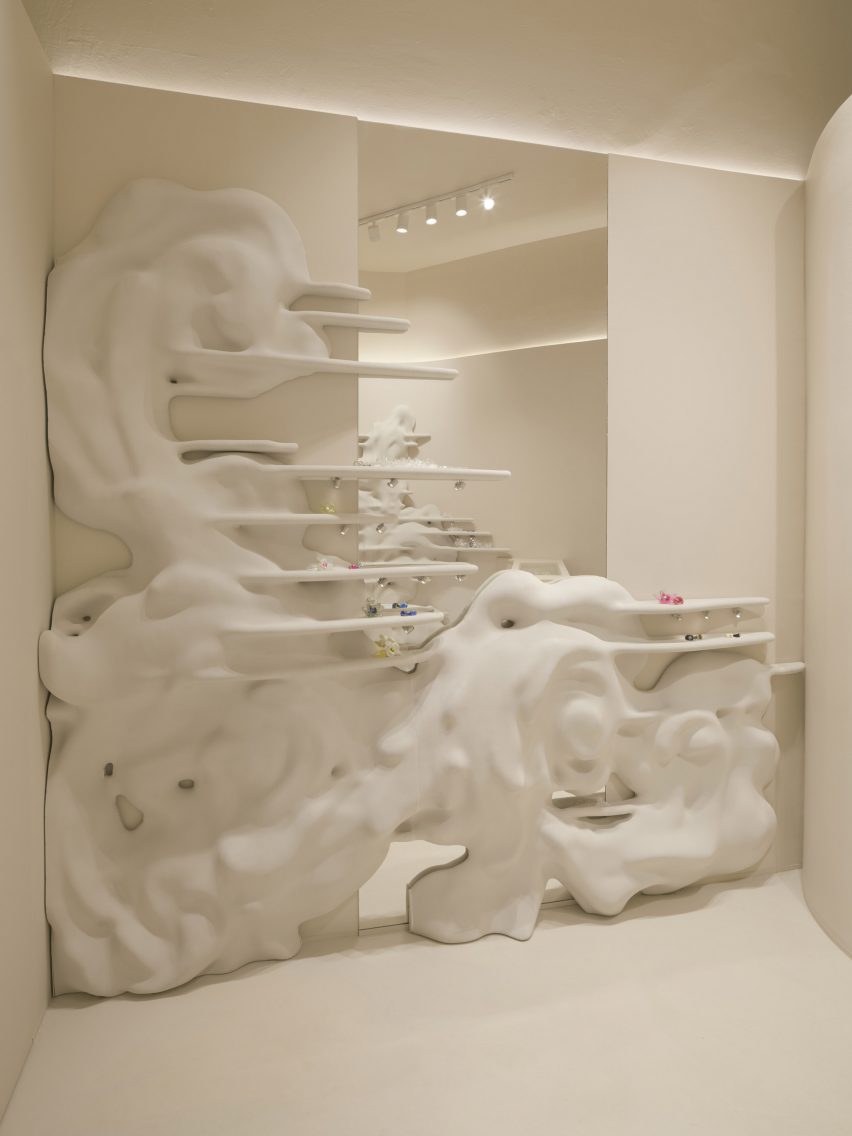
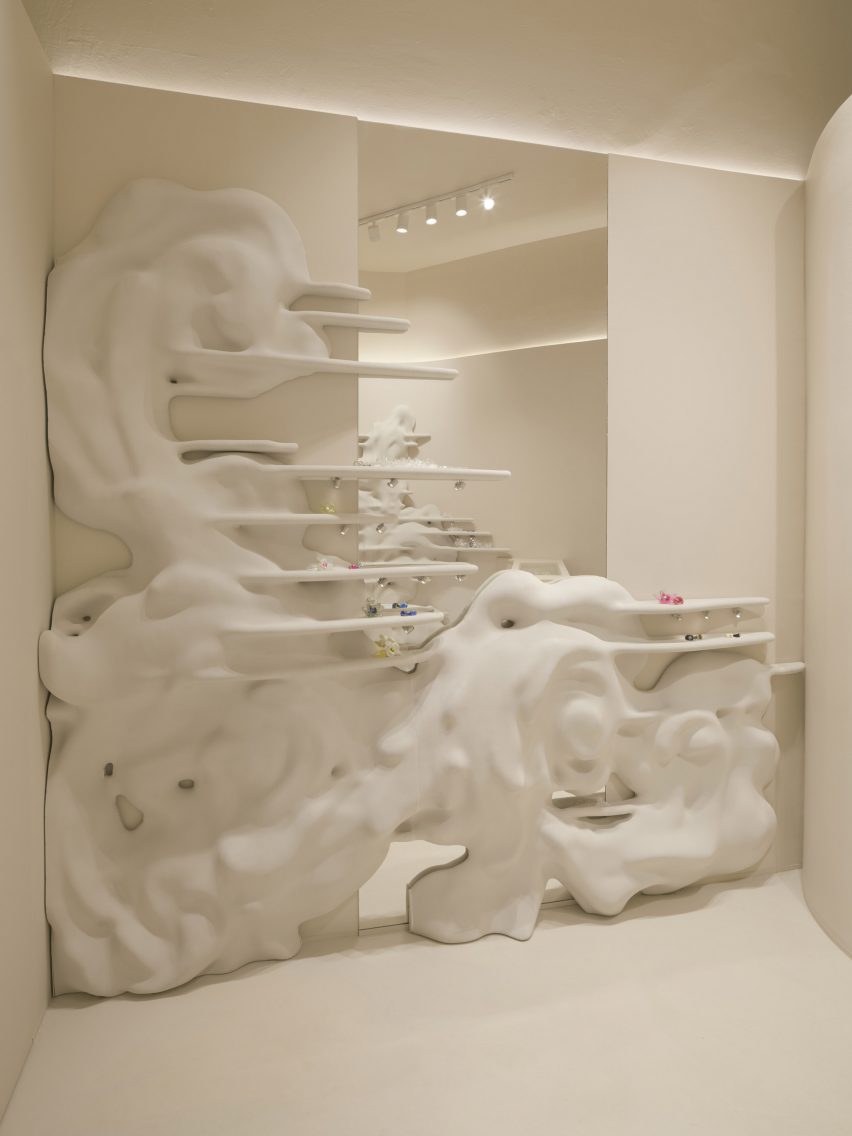
All of the printed elements are finished in a muted off-white shade that matches the rest of the interior and provides a neutral backdrop for displaying the jewellery.
Large, mirrored surfaces help to make the interior feel more expansive, while spotlights provide targeted illumination for highlighting the collection.
In addition to the main furniture, the designers also developed a window display and 3D-printed signage that extend the store’s conceptual design out into the street.
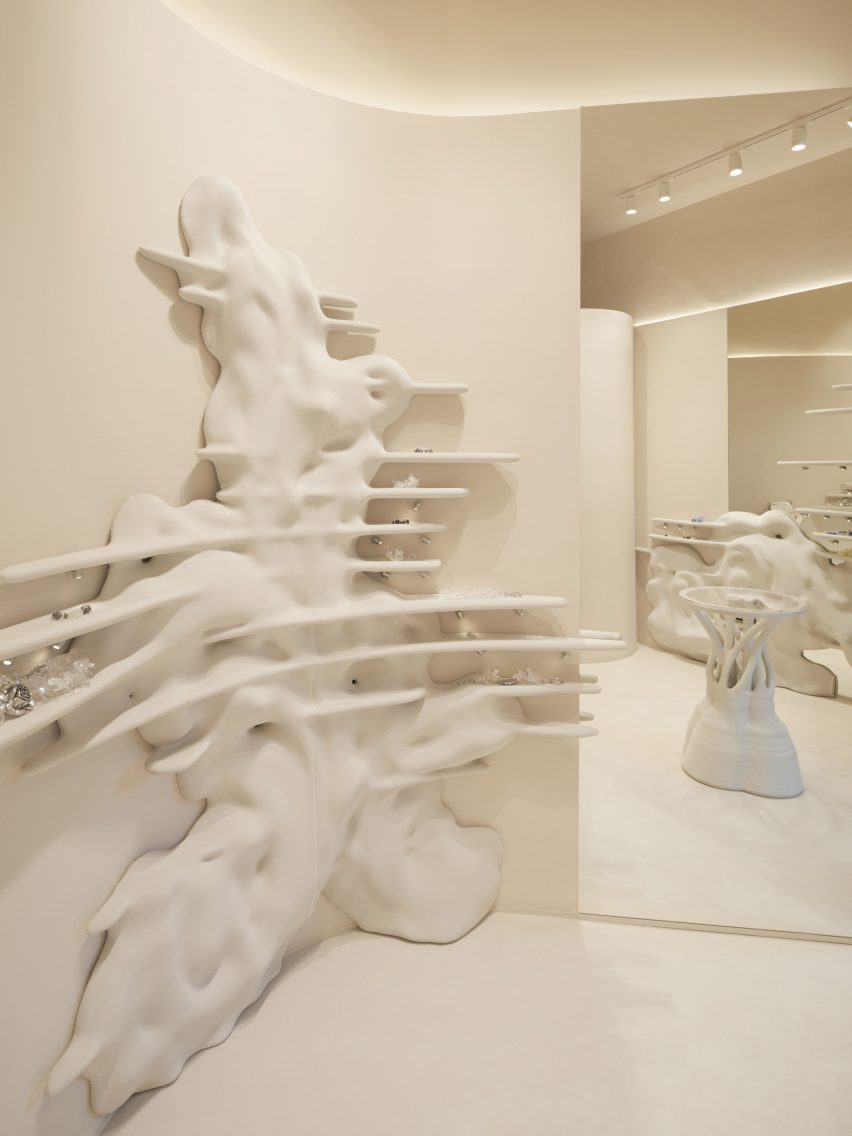
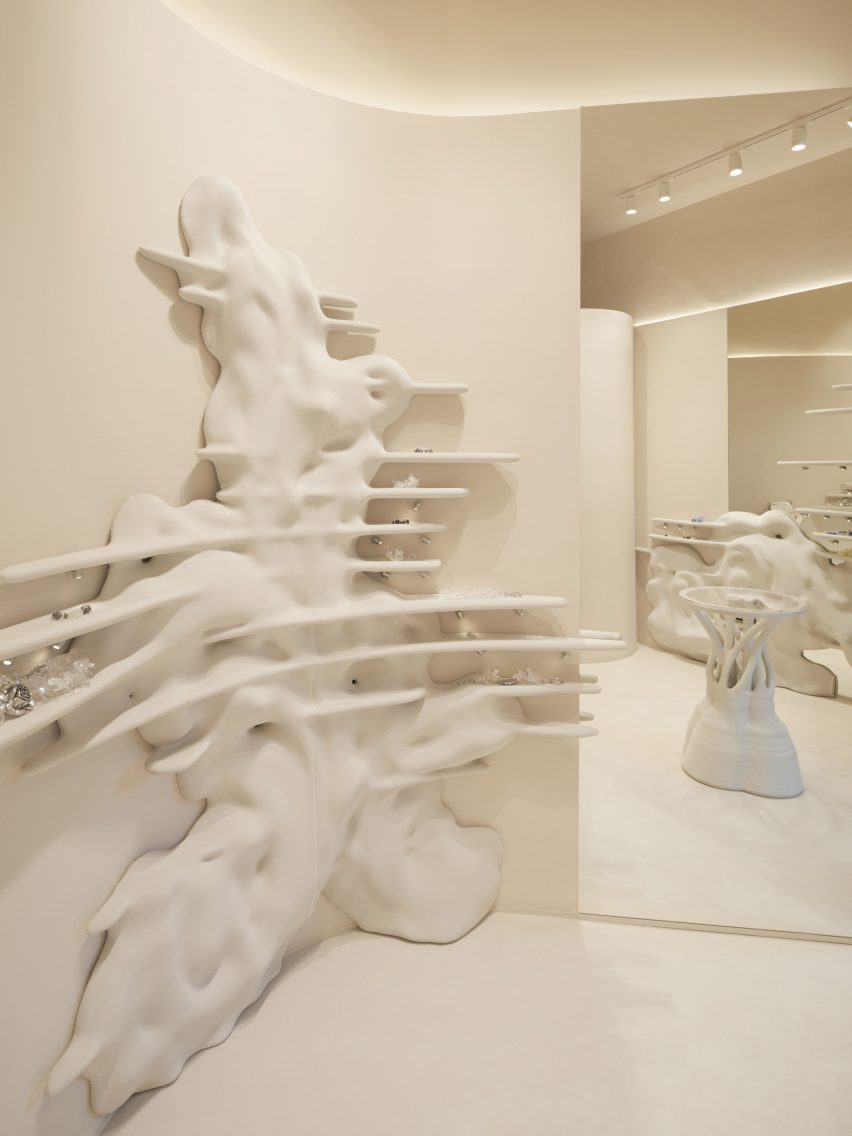
Large-scale 3D-printing technology offers designers possibilities to create unique elements for branded interiors, which makes it increasingly popular for retail spaces.
Spanish design studio Nagami has created a store for sustainable clothing brand Ecoalf featuring transparent 3D-printed displays that recall melting glaciers, while Dutch architecture practice Studio RAP used the technology to produce a wave-like tiled facade for an Amsterdam boutique.
The photography is courtesy of External Reference.