FranklinTill lists nine principles for a shift to regenerative materials
Design research agency FranklinTill has compiled a list of principles to help designers, makers and brands avoid greenwashing when sourcing textiles.
By making it easier to identify textiles that have a greater positive impact on people and planet, FranklinTill hopes to enable a shift towards regenerative materials.
“We can only move towards a regenerative approach to textiles by understanding the full lifecycle of our materials,” said co-founder FranklinTill Caroline Till.
“As designers, makers, brands and manufacturers, we need to think of materials not as static and linear, but as dynamic, evolving systems, to holistically consider the full impact to the wider ecosystem they are a part of.”
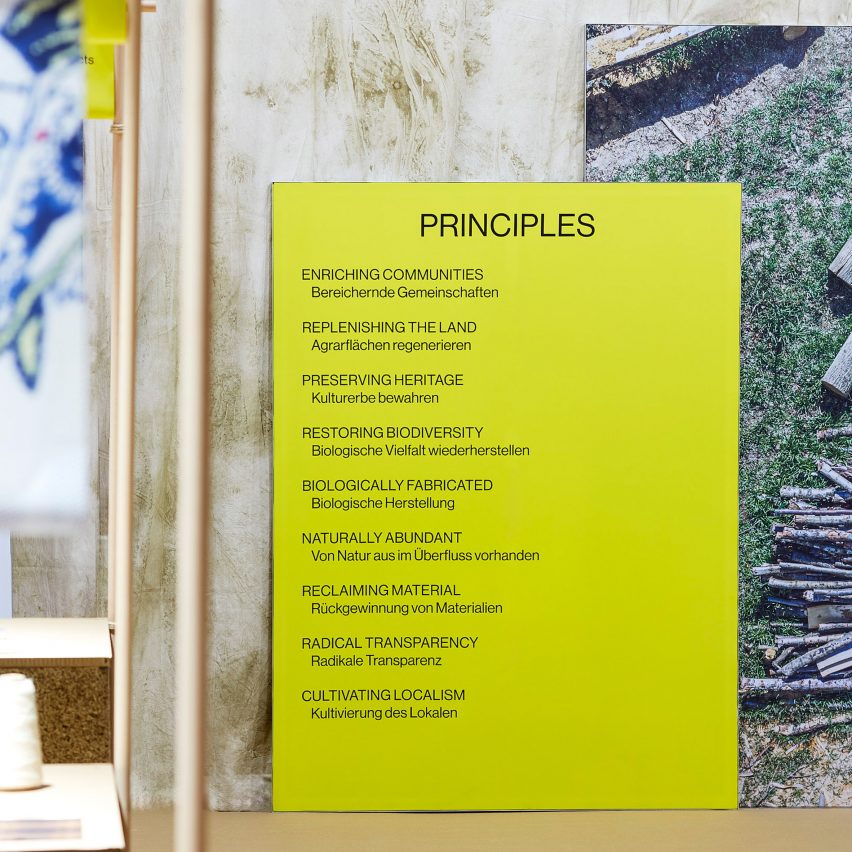
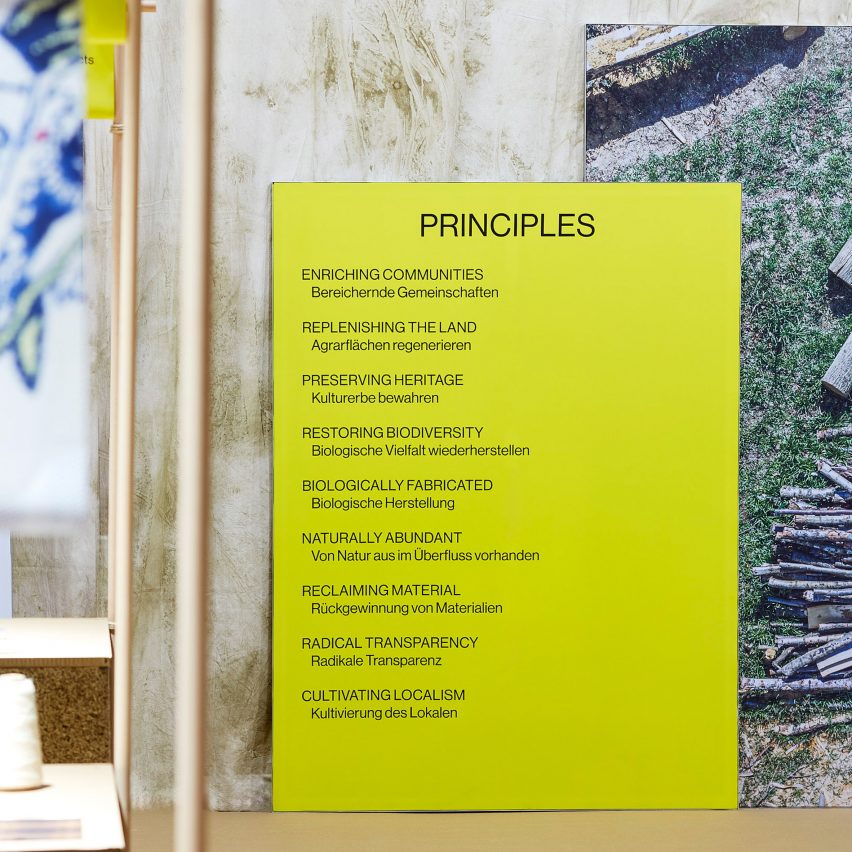
The defining characteristic of regenerative materials, according to Till, is that they restore and nourish the ecosystems they are part of.
“Sustainability, by its very definition, is all about maintaining the status quo, while regeneration seeks to actively heal and put back better,” she said.
FranklinTill first unveiled its nine principles of regenerative design in an exhibition at the Heimtextil trade fair in Frankfurt in January, with a second show planned for the Techtextil fair in April.
In an online exclusive, we are also unveiling them here. Read on to see all nine, with captions written by FranklinTill and examples of material innovation in practice:
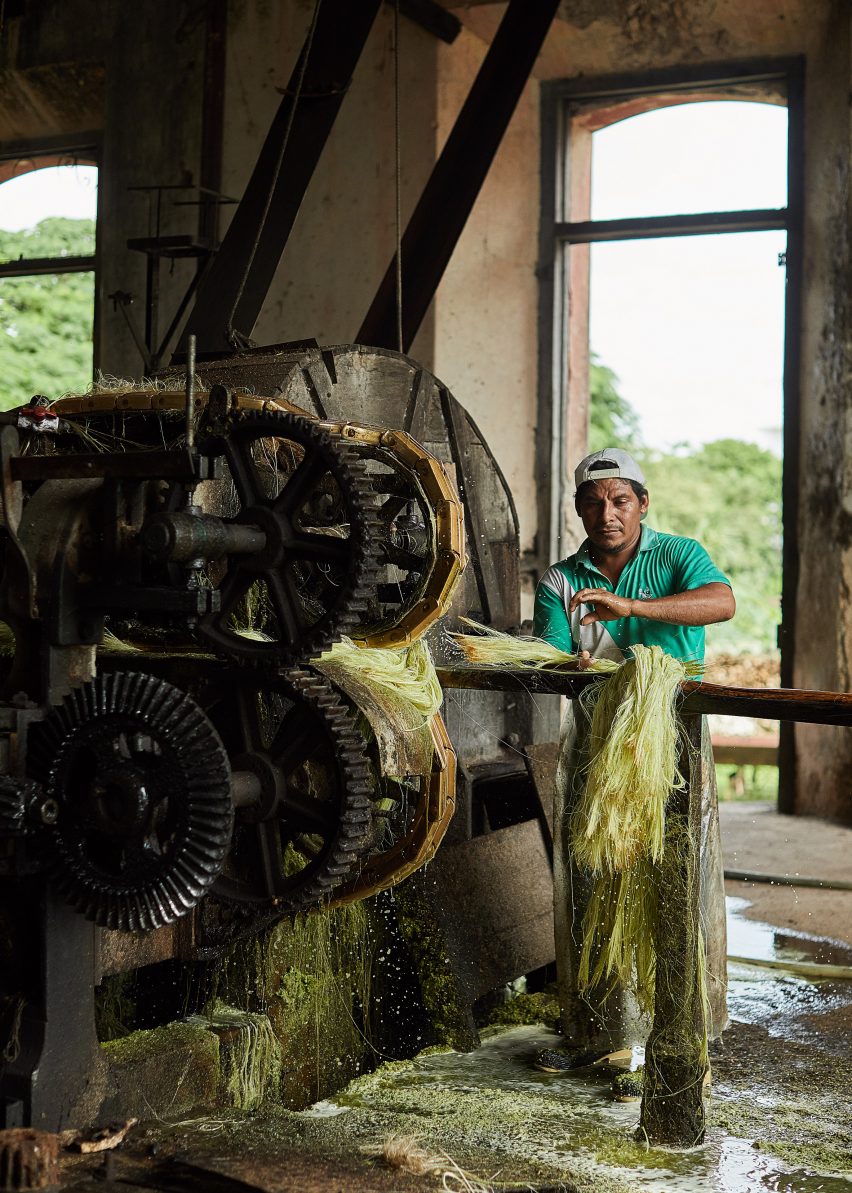
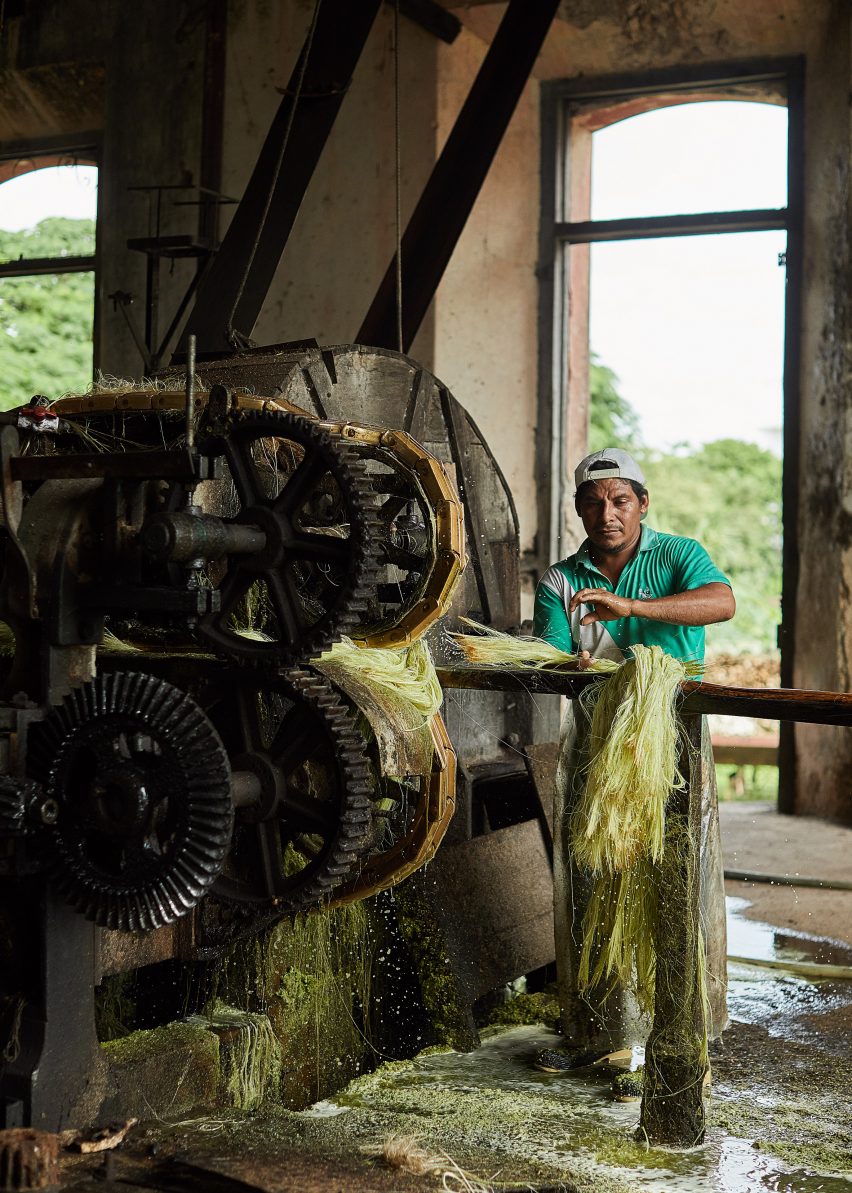
Enriching Communities
“To go beyond sustainability and become regenerative, we must focus on both the social and the environmental impact of production.”
“This means spotlighting how materials are made and by whom, looking to improve livelihoods with better pay, working conditions and future prospects.”
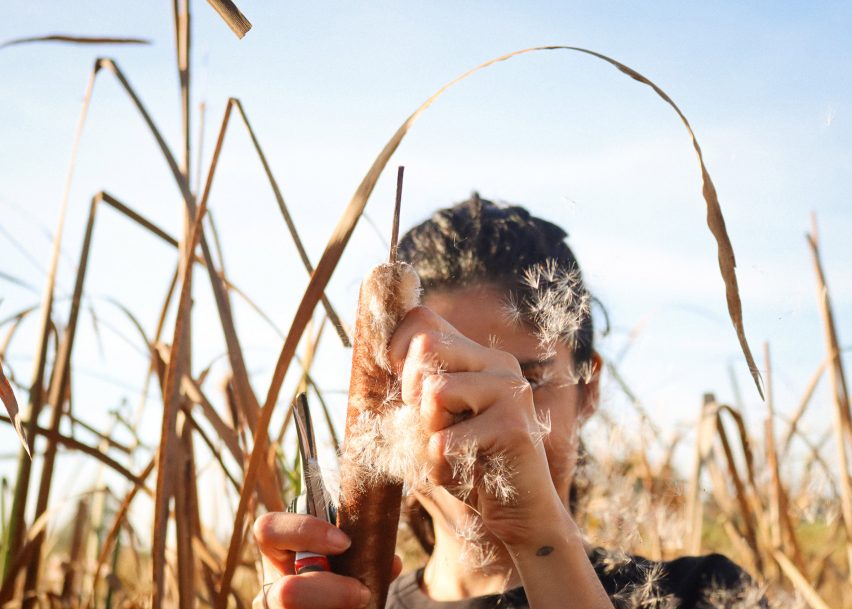
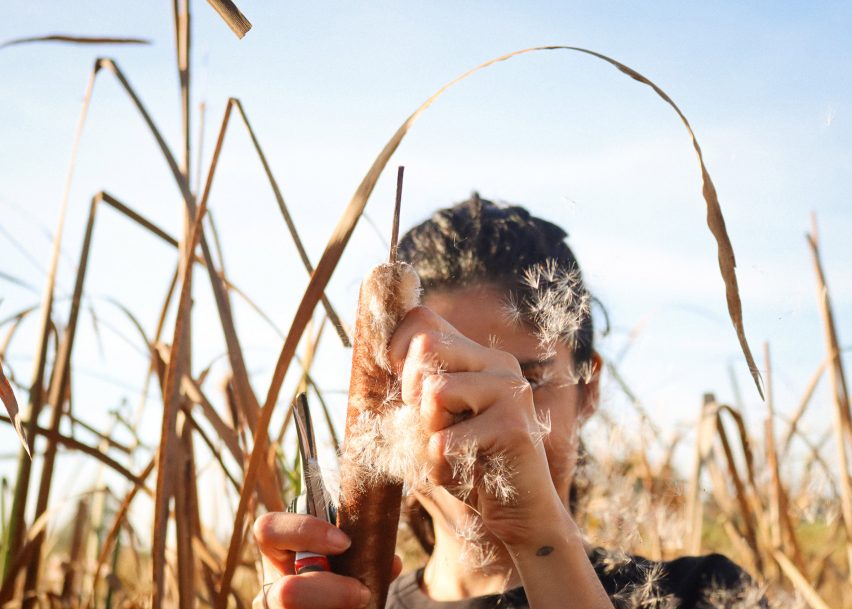
Replenishing the Land
“Focused on high yields with an over-reliance on pesticides and water, modern industrial farming damages land.”
“Regenerative farming works holistically to reverse this, rebuilding organic soil matter and sequestering carbon in soil, wetlands and trees, retaining water and reducing the use of artificial pesticides and fertilisers.”
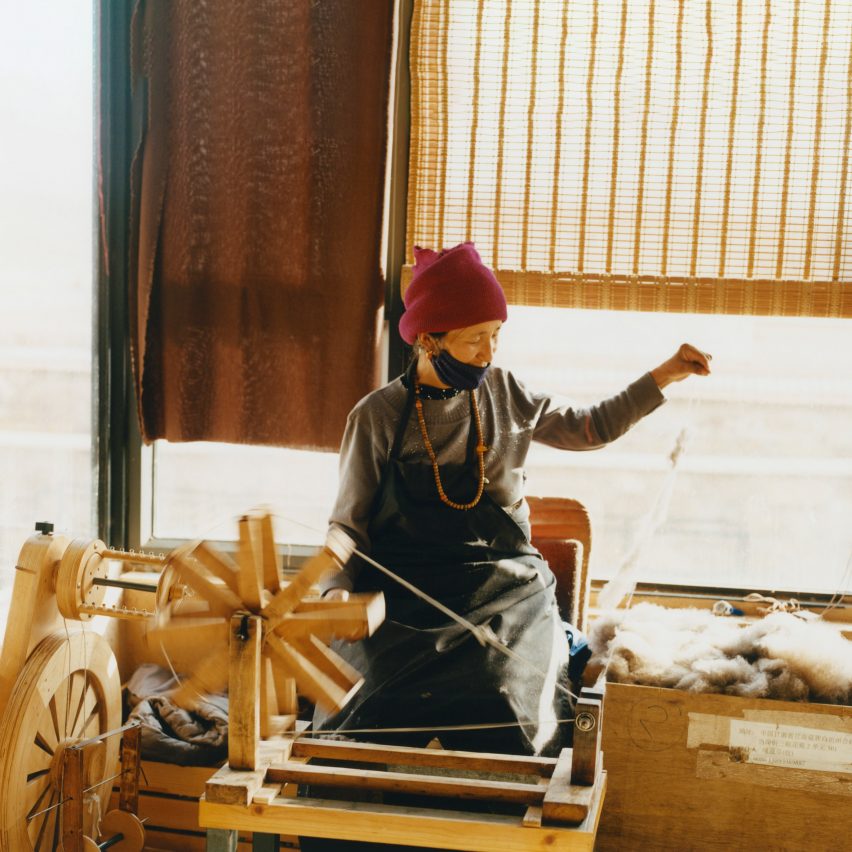
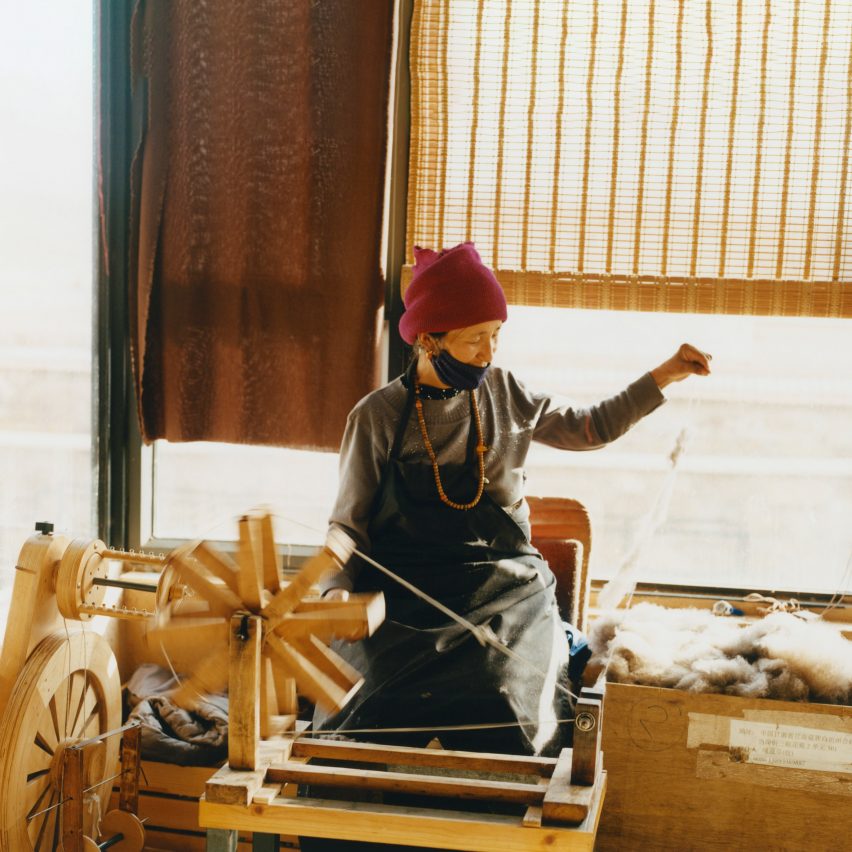
Preserving Heritage
“Many indigenous practices are regenerative by nature, working with the land and local communities.”
“By acknowledging and celebrating the value of cultural heritage and craftsmanship and learning from its ecological wisdom, we can protect valuable skills and knowledge from being lost to technology and globalisation.”
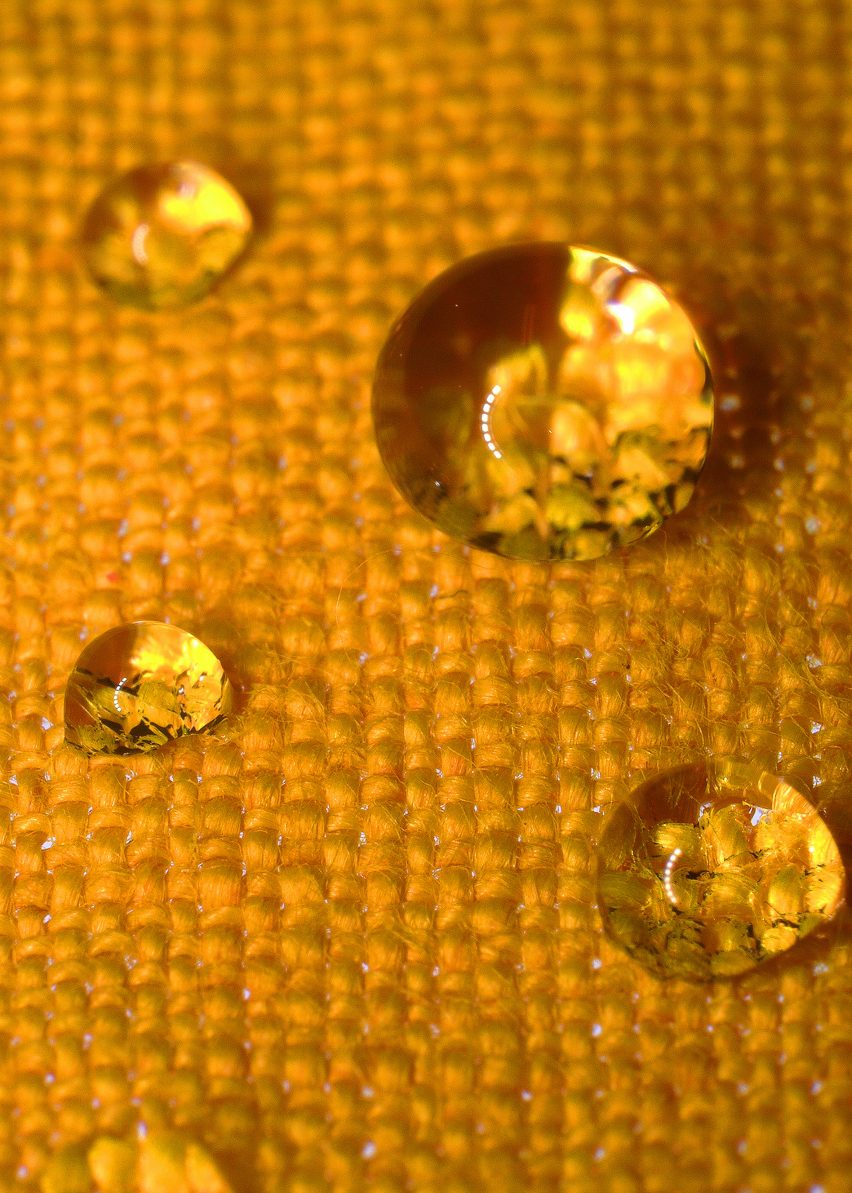
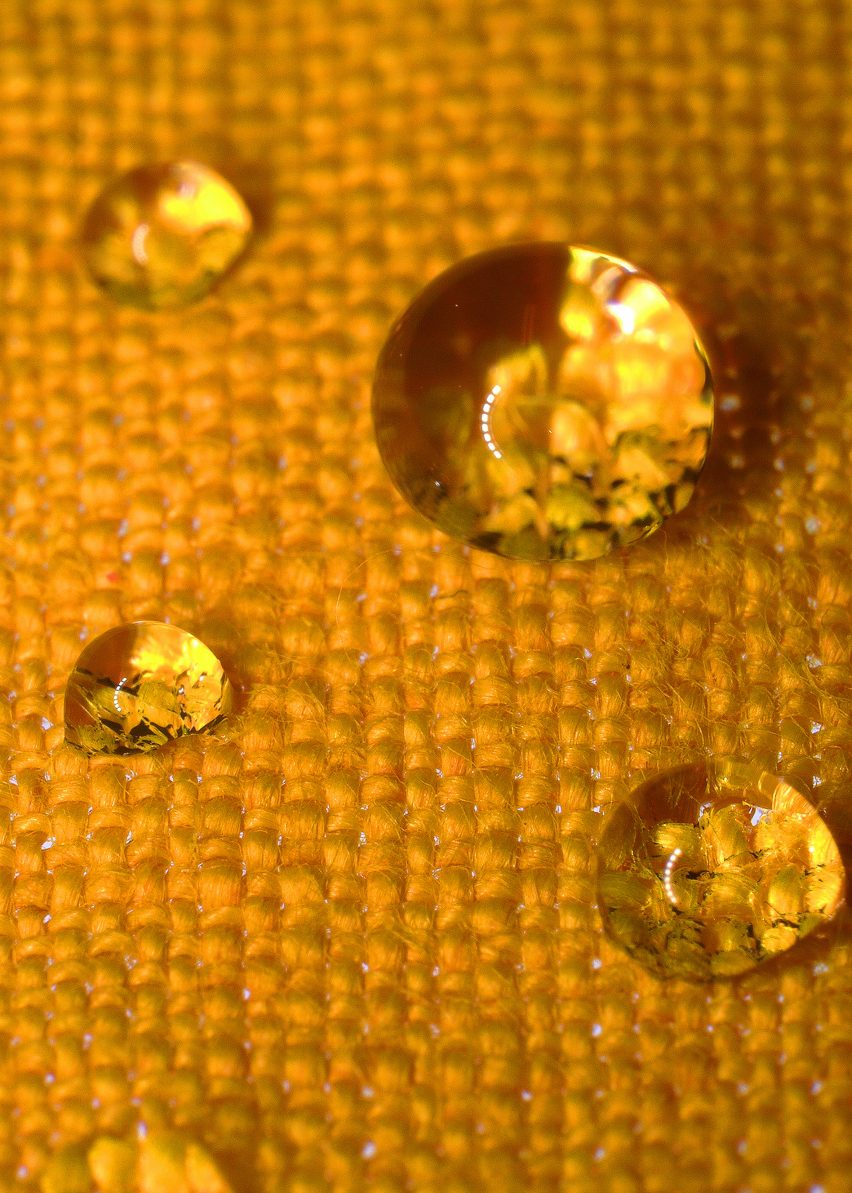
Restoring Biodiversity
“Regenerative practices must take a multispecies approach to encouraging biodiversity.”
“Acknowledging the threat of extinction, addressing the causes of loss, and reviving habitats for diverse plants and wildlife aids ecological restoration.”
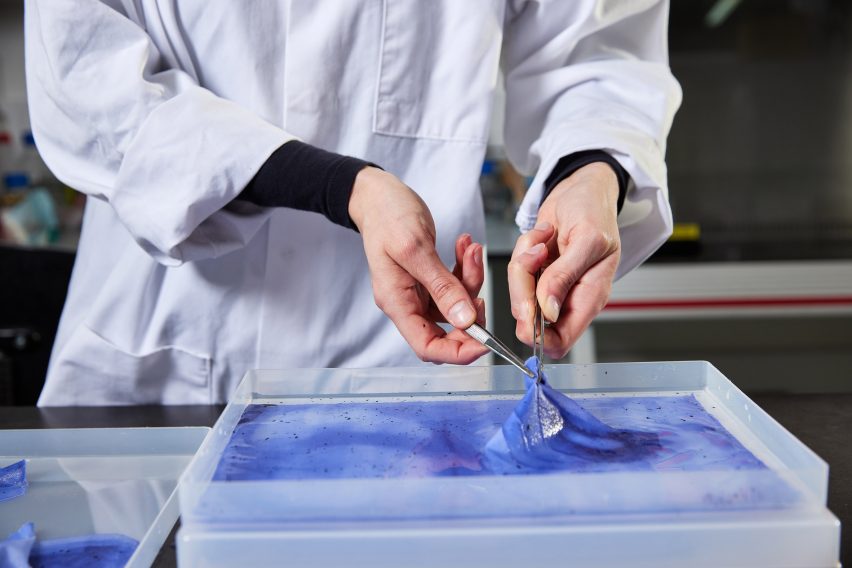
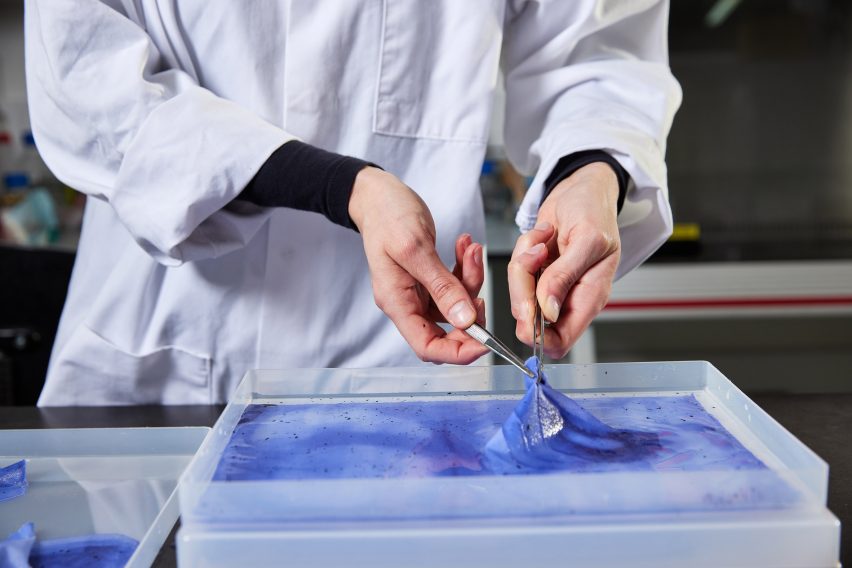
Biological Fabrication
“The convergence of science and design offers huge potential for new materials, from living microbial systems to synthesising nature’s regenerative powers.”
“Growing and extracting next-generation materials using innovative, highly productive processes can create plentiful resources from minimal input.”
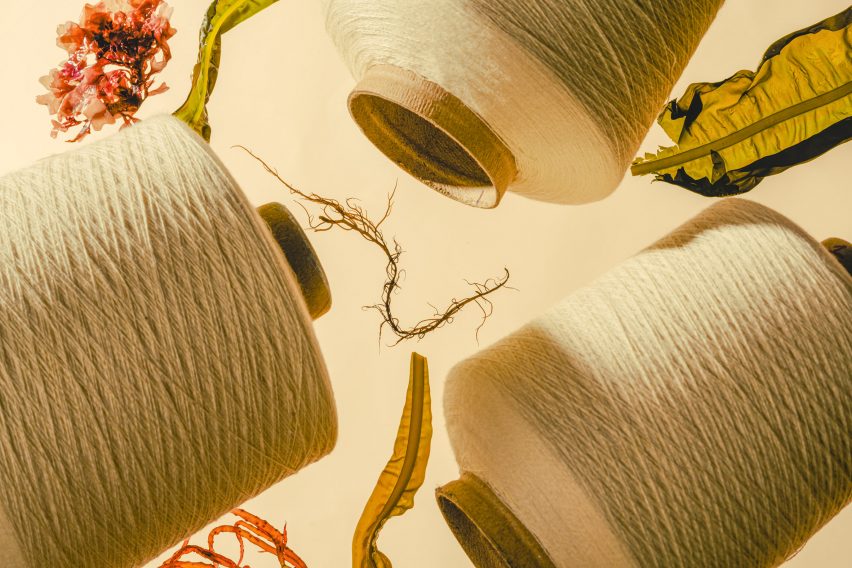
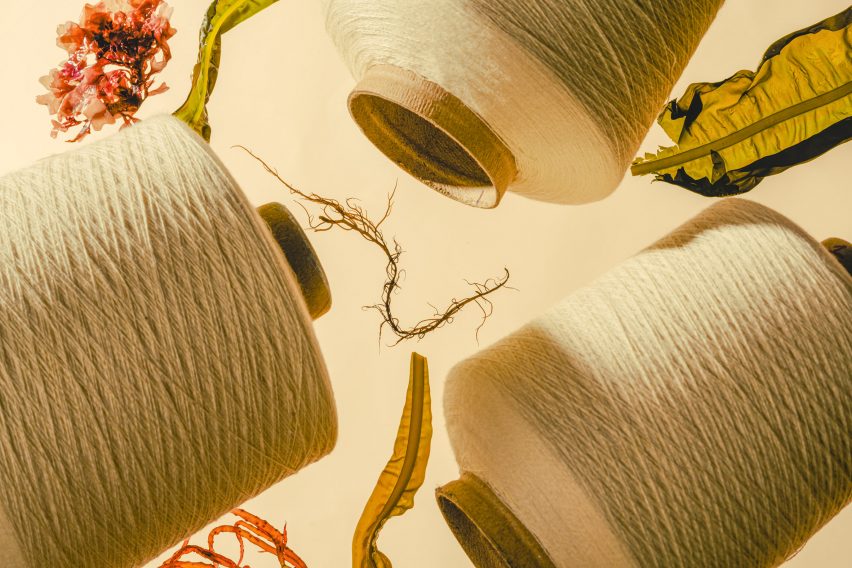
Naturally Abundant
“Highly productive, resilient raw materials that grow with little human intervention offer naturally high yields, strengthen soils and capture carbon.”
“These abundant, versatile crops could help move the focus away from traditional natural material fibres that require high levels of water, pesticides or fertilisers.”
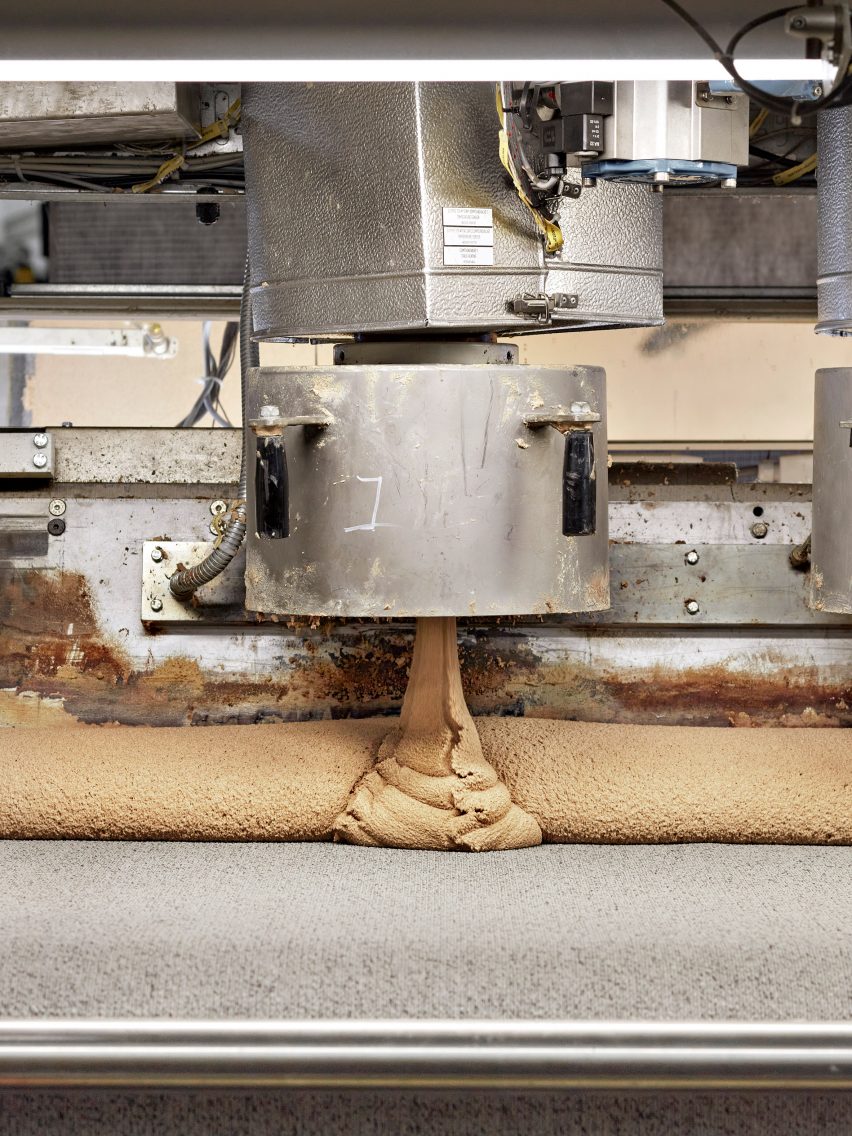
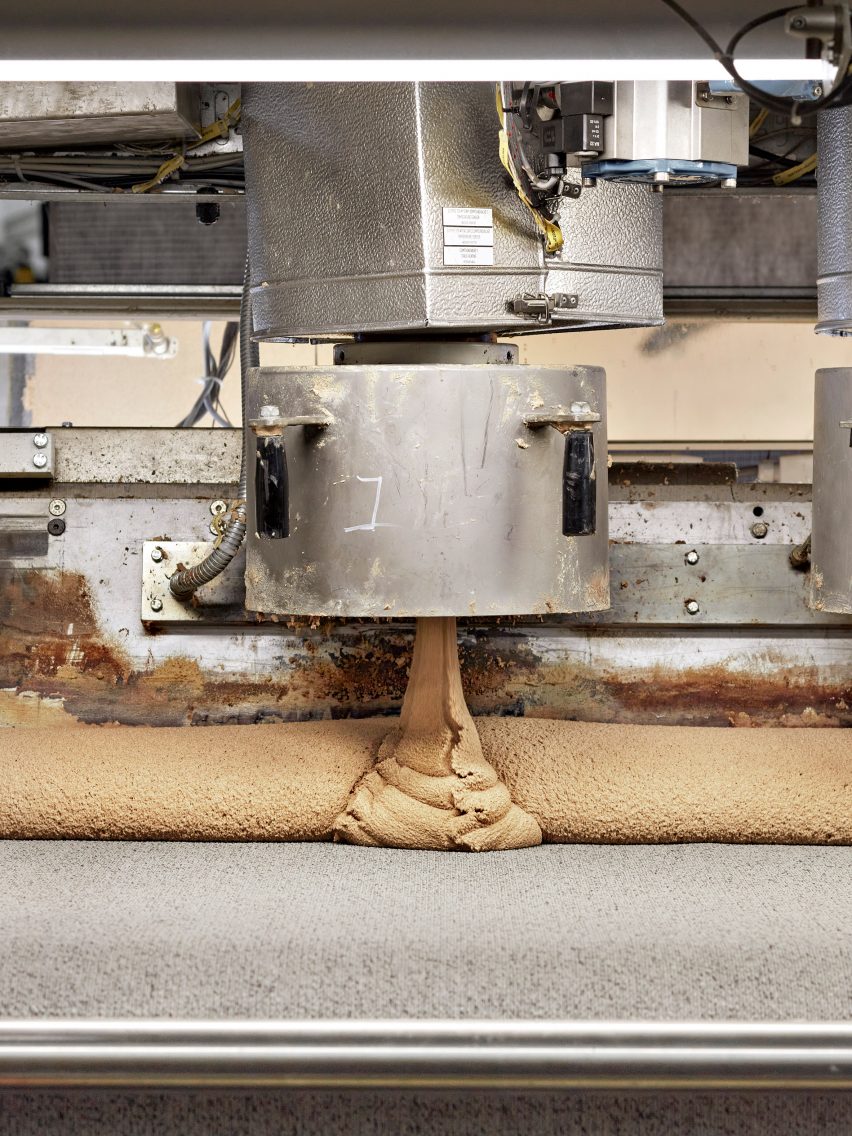
Reclaiming Material
“Extracting raw materials, making products, then discarding them and their byproducts is contributing to the global waste problem.”
“By putting useful waste streams back into production, we can better utilise existing resources and avoid waste altogether.”
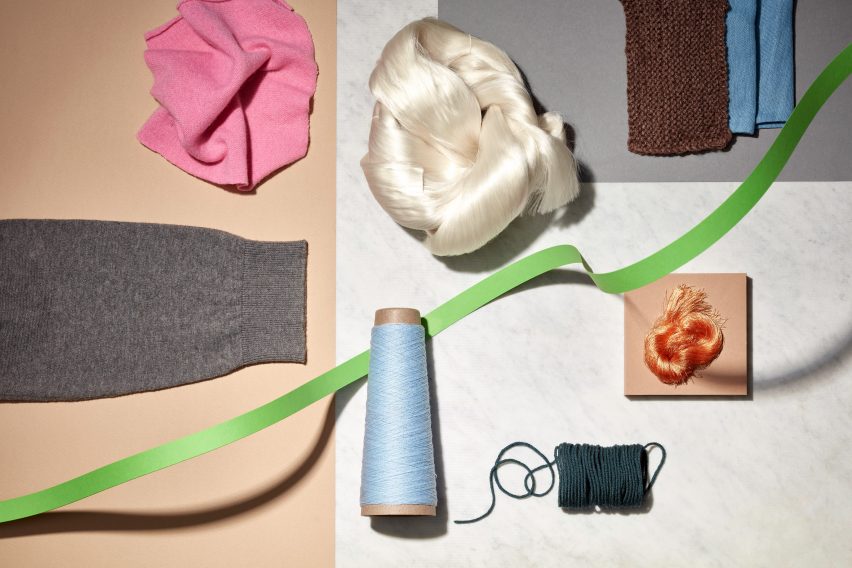
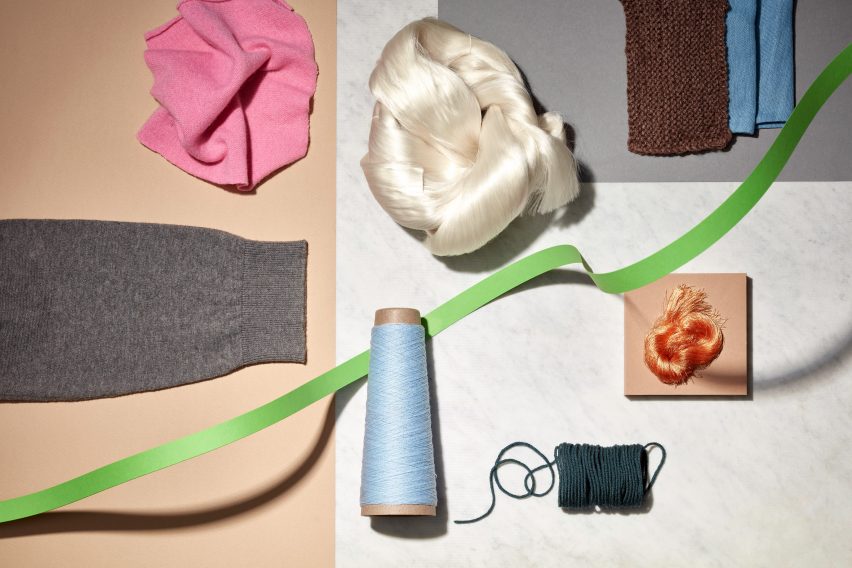
Radical Transparency
“By using science and technology to create tools and processes that capture and record data along supply chains, we can understand the social and environmental impact of the materials we consume.”
“Encrypting materials helps brands track their footprints and life cycles, and communicate this information to customers in a meaningful, trustworthy and accessible way.”
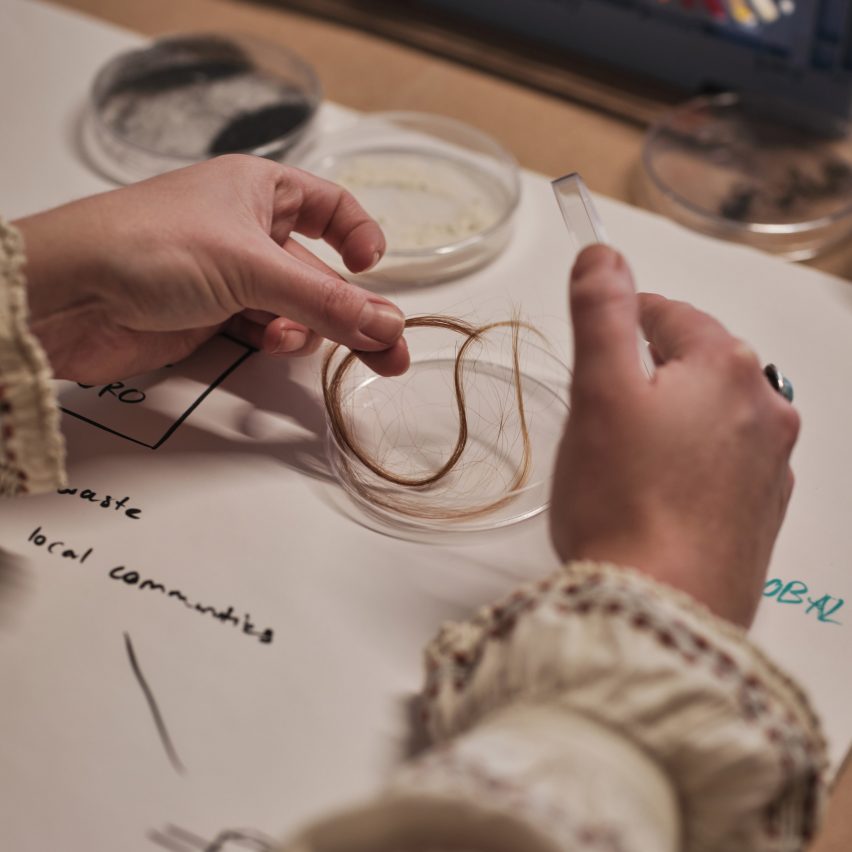
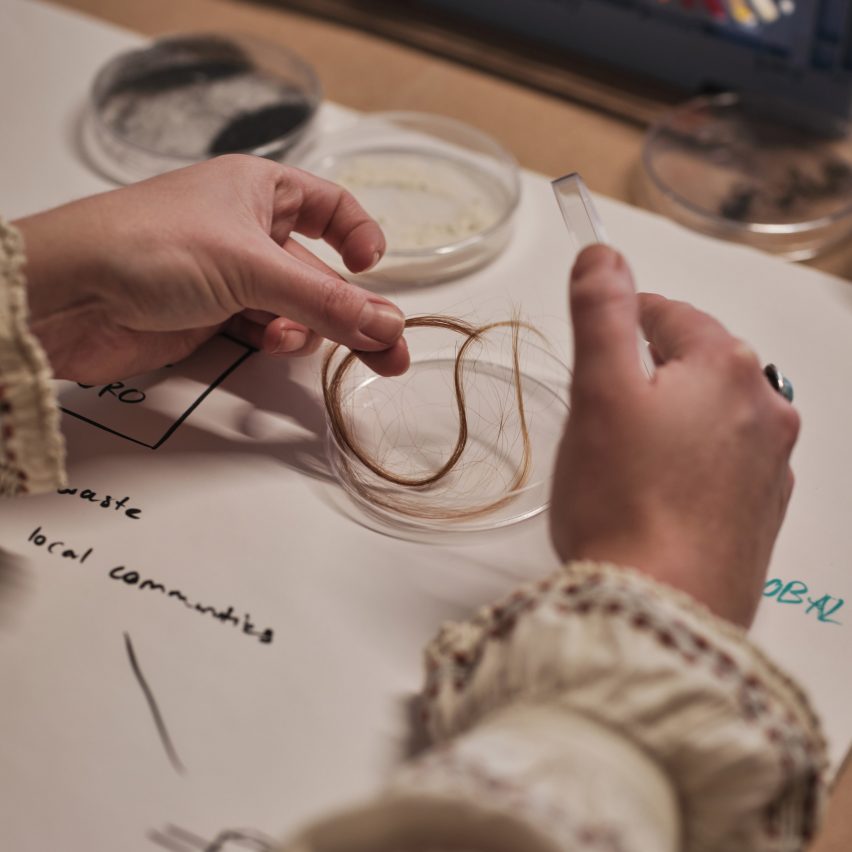
Cultivating Localism
“By supporting the local sourcing, production and consumption of materials, we can avoid globalised transportation and reduce carbon footprints.”
“Focusing on availability, seasonality and resourcefulness means embracing non-standardisation, often improving local environments as well as extracting from them.”