Snøhetta designs compostable hemp light Superdupertube
Norwegian studio Snøhetta has teamed up with lighting brand Ateljé Lyktan to create Superdupertube, an office lamp made from extruded hemp and sugarcane bioplastic.
The design is a contemporary update of Ateljé Lyktan‘s Supertube – an office light from the 1970s made from extruded aluminium.
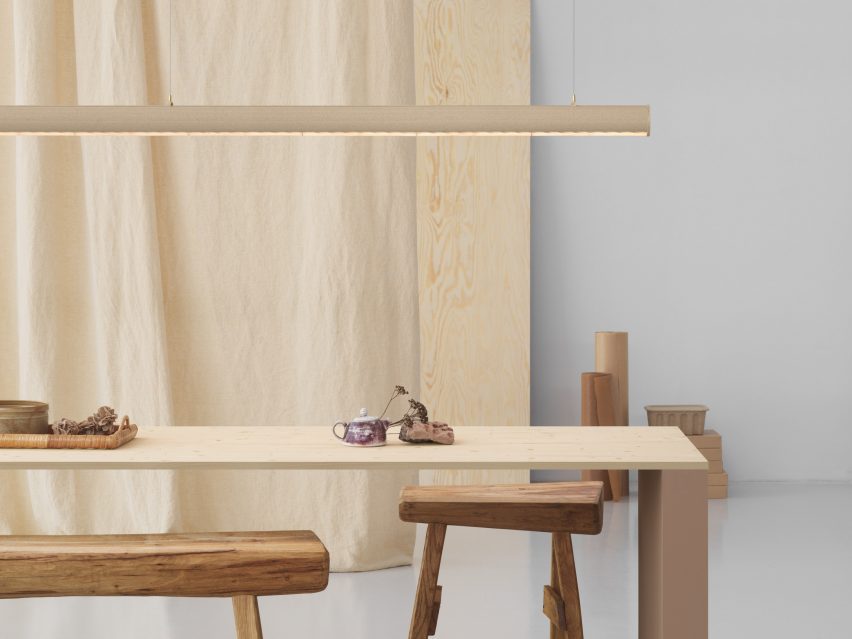
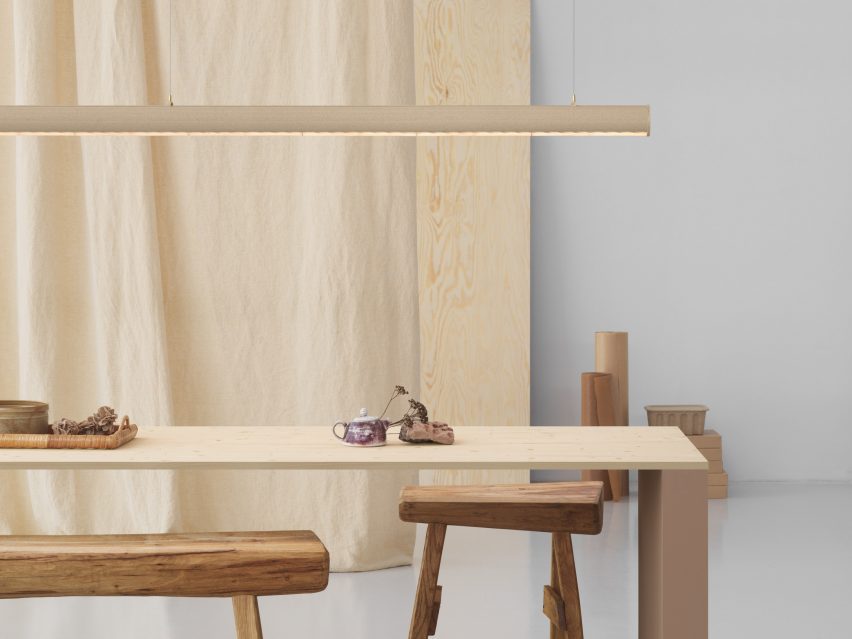
“[The Supertube] had finished production in 2010 or something like that, so it was iconic but sort of forgotten,” Snøhetta partner Jenny B Osuldsen told Dezeen. “And it’s a tube. It’s not rocket science but it is what you need for a smart lamp in an office.”
“We really loved it and think it has a lot of possibilities, so we wanted to upgrade it to a new level,” she added.
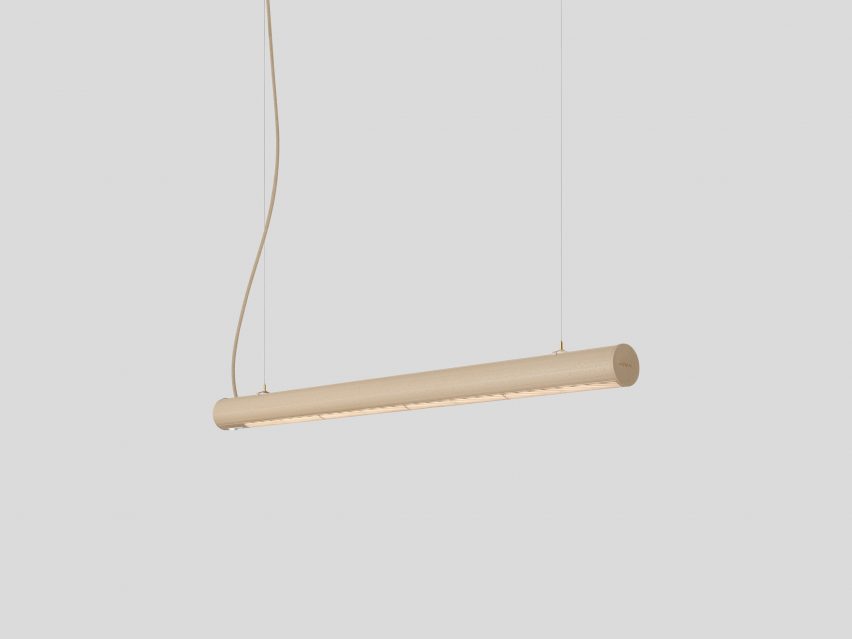
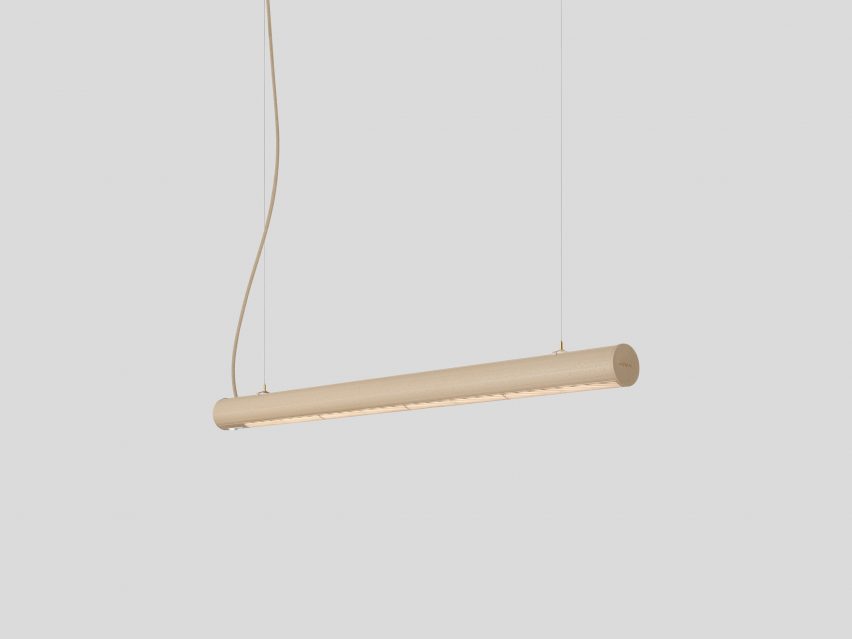
The extrusion technique for the original lamp was developed in the 1960s, and Snøhetta and Ateljé Lyktan decided to create a lamp that would nod to the original design.
However, the aim was to lower the carbon footprint of the lamp by choosing the most sustainable material possible.
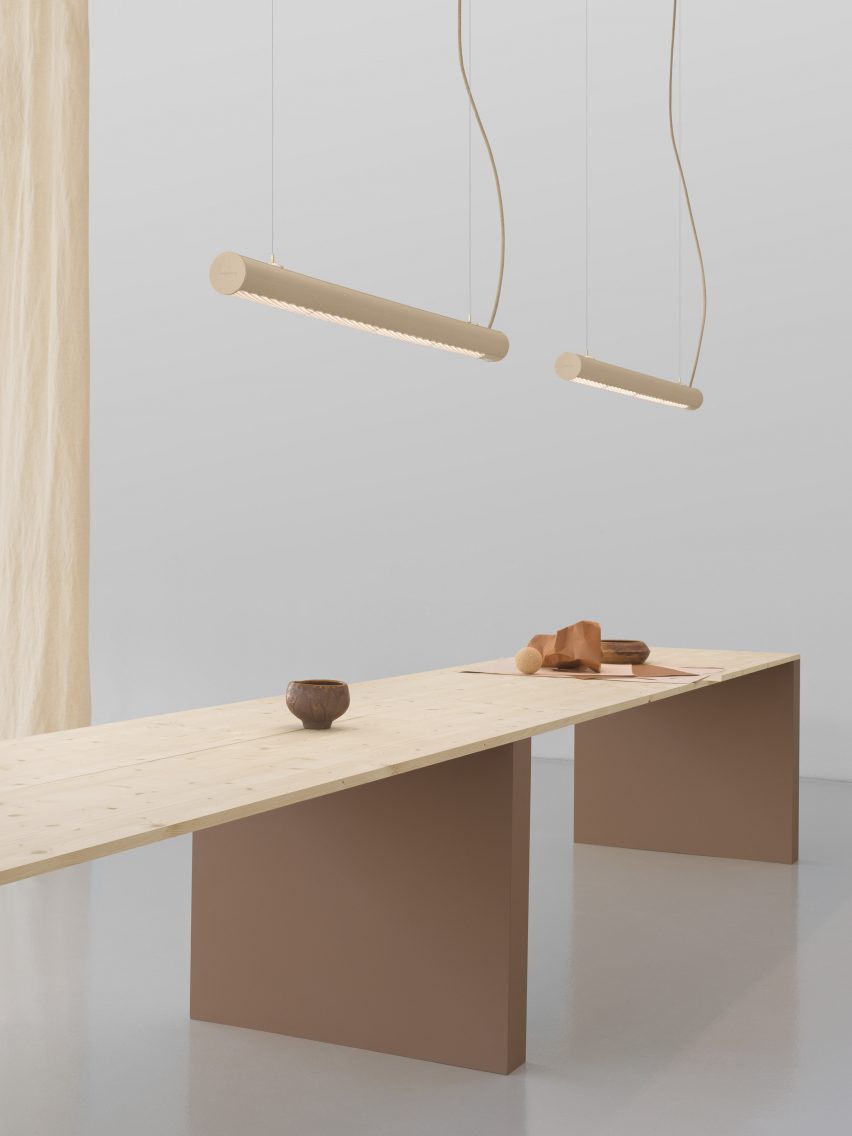
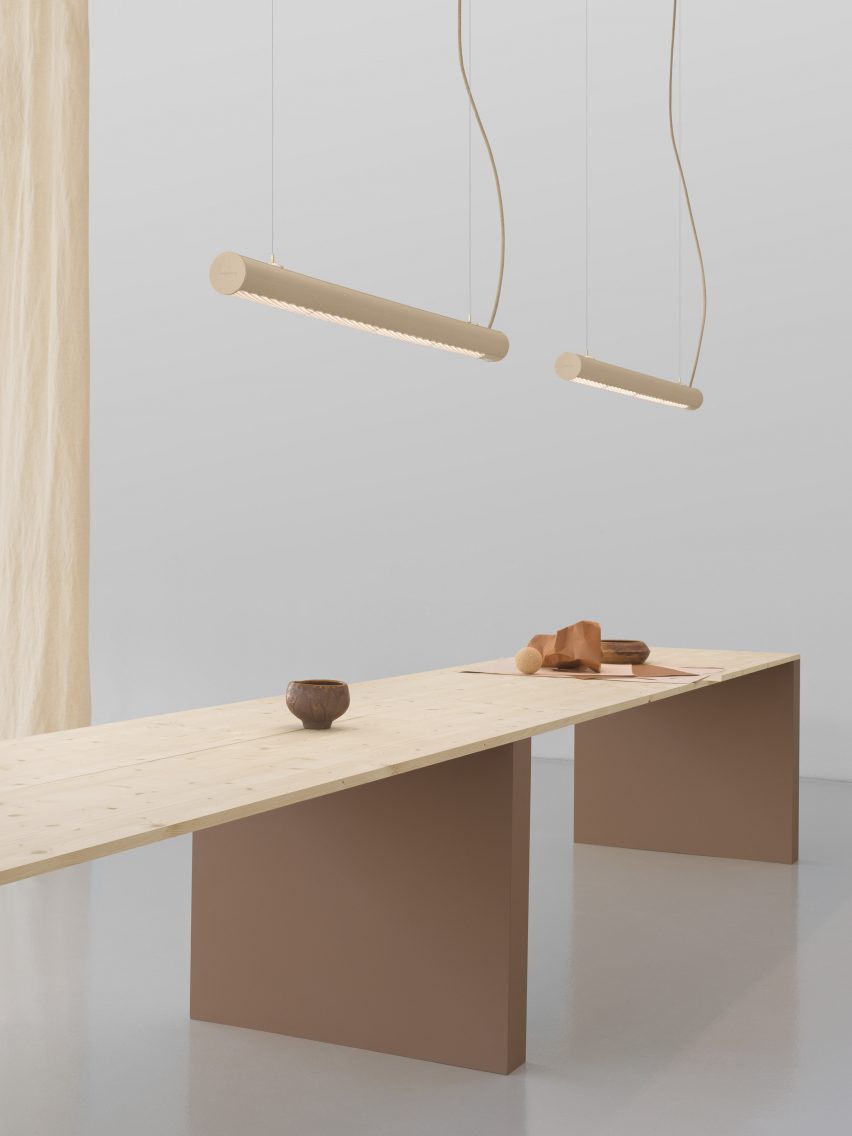
The studios played around with multiple different materials before settling on the hemp bioplastic, which was used to form Snøhetta’s first office lighting design.
Snøhetta and Ateljé Lyktan first worked together on The 7th Room, a charred-timber cabin suspended among the treetops in northern Sweden, for which they also collaborated on the lighting design.
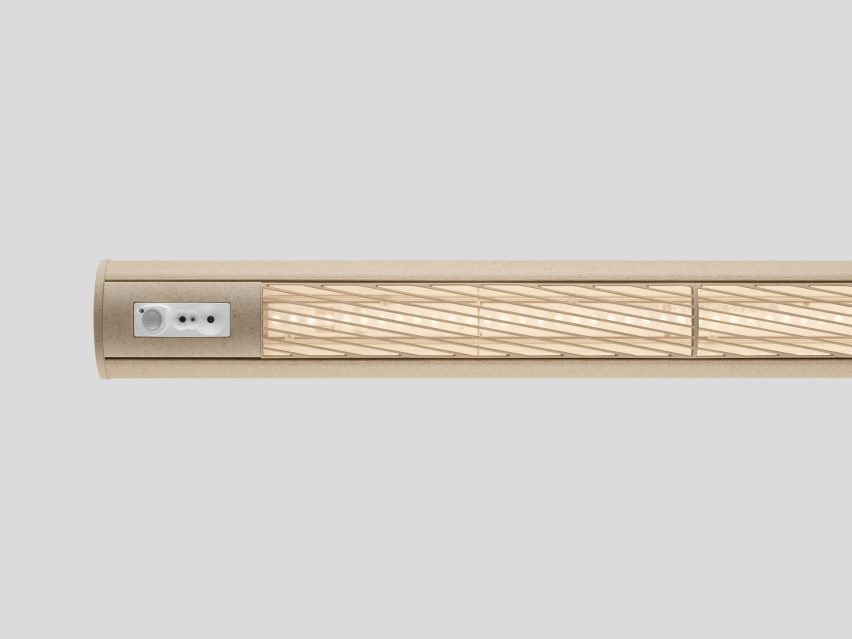
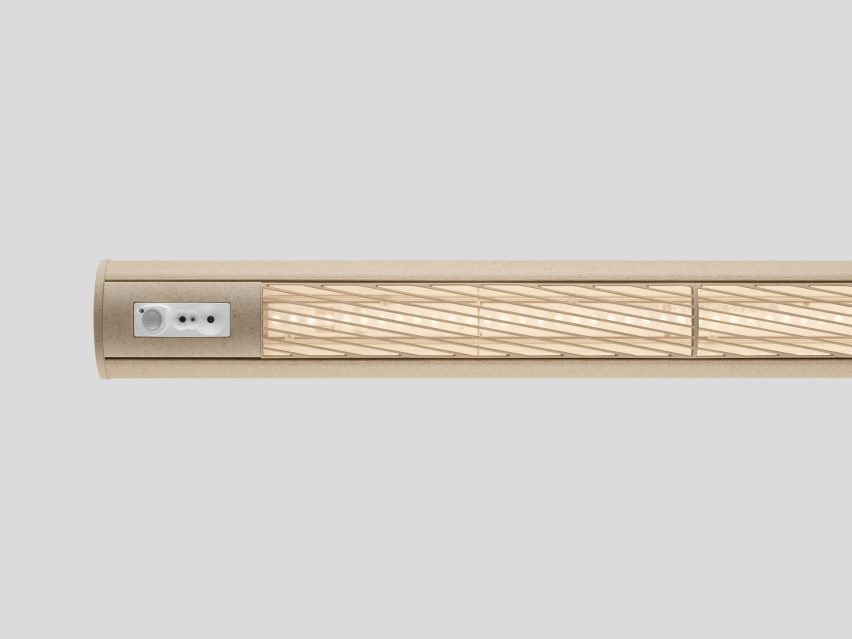
“When we were doing The 7th Room project up in northern Sweden, everything was in pine and there were lots of pine cones,” Osuldsen said.
“We wanted to find a product or material that isn’t used for anything else, so we started testing the use of pine cones by grinding them, but it didn’t work.”
“The fibres in the cones are too short,” said Ateljé Lyktan product director Malin Gadd. “We also tried using coffee grounds but they are even shorter, so we realised quite quickly that we needed fibres that are long and strong.”
“That’s where the hemp fibres come into the picture,” she added.
Snøhetta and Ateljé Lyktan sourced the hemp used for the lights from the Netherlands, as the quality of the hemp from Swedish farmers “wasn’t quite there yet”, according to Gadd.
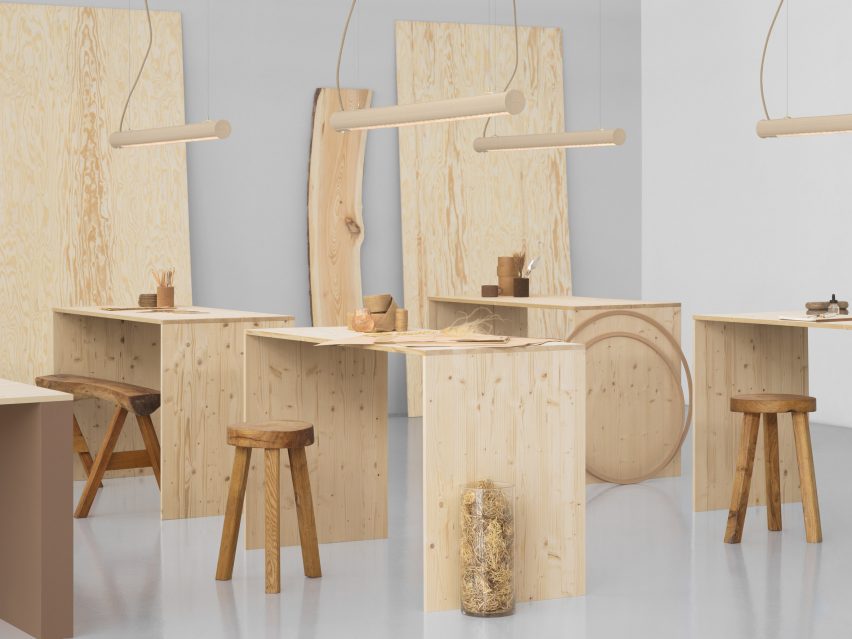
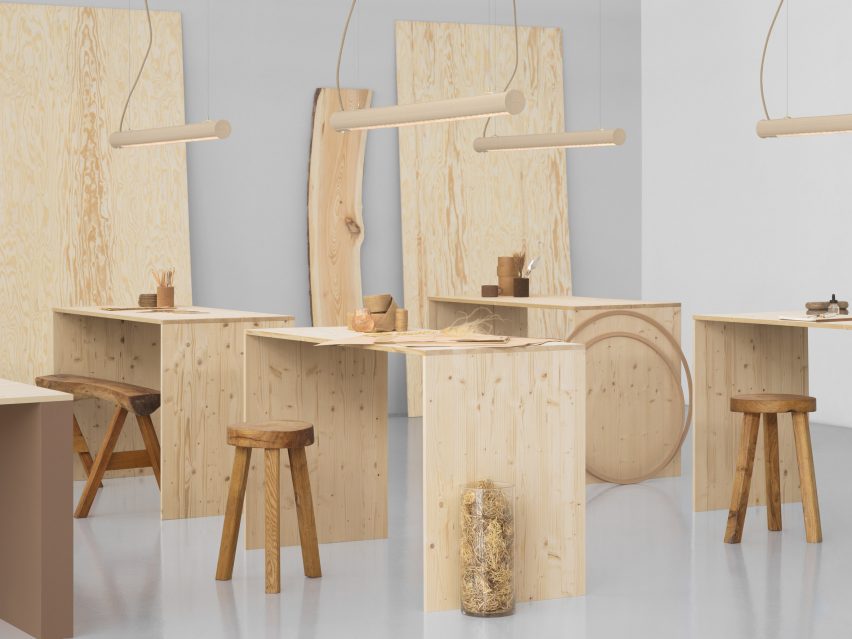
The hemp is mixed with a polylactic acid (PLA) bioplastic derived from sugarcane, alongside wood cellulose and different minerals to create a fossil- and gas-free composite.
The material is then extruded to create the main body of the lamp, which also comprises injection-moulded louvres and side covers. To add to the organic feel of the light, its electric cables are covered with linen fabric.
“Hemp is an old cultural plant and it’s very easy to renew [by growing more],” Osuldsen said. “And it’s very durable.”
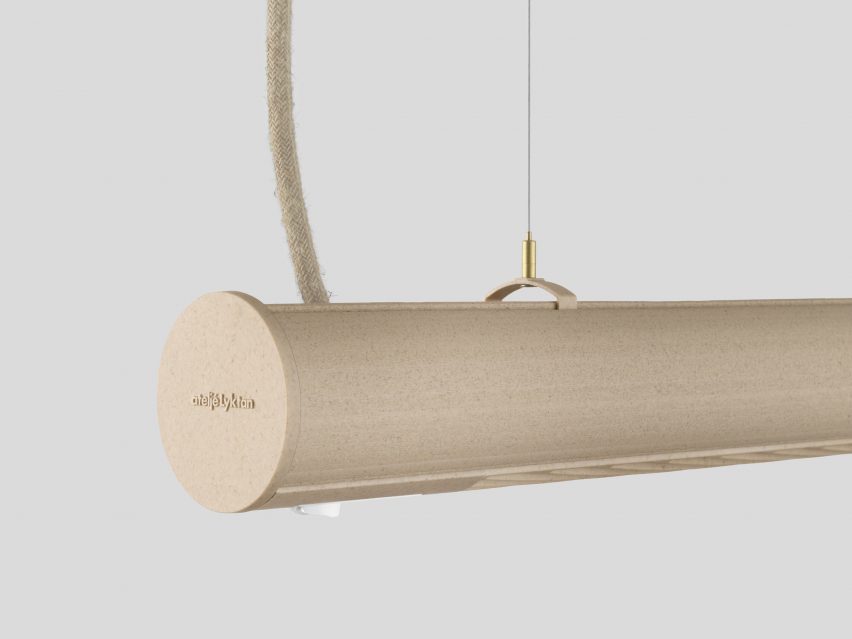
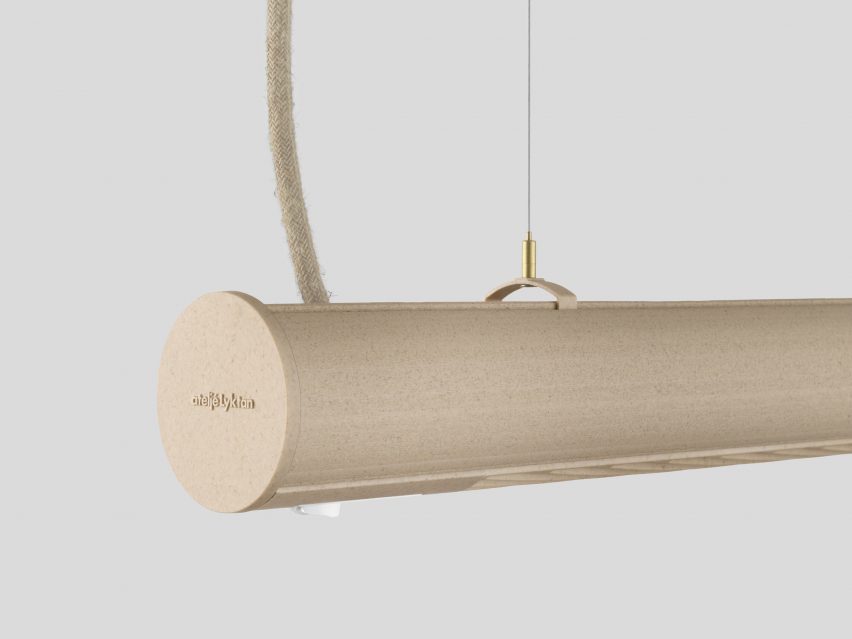
The Superdupertube can be composted in an industrial composter or recycled and ground down into pellets to create more lamps.
However, this currently requires owners to send the lamps back to the producer, as the material cannot be processed in regular recycling centres.
Using the hemp bioplastic reduces the lamp’s carbon footprint by over 50 per cent compared to traditional aluminium variants, according to Snøhetta and Ateljé Lyktan.
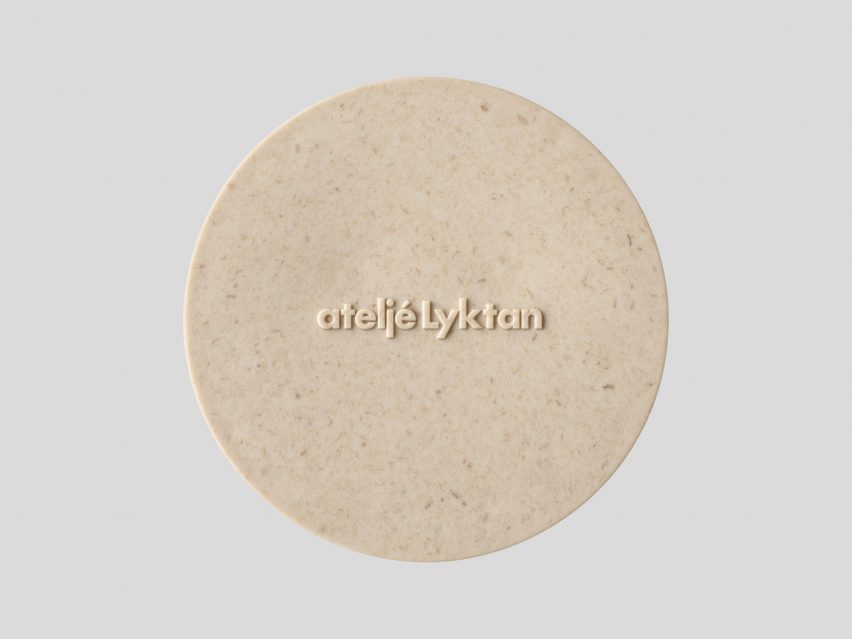
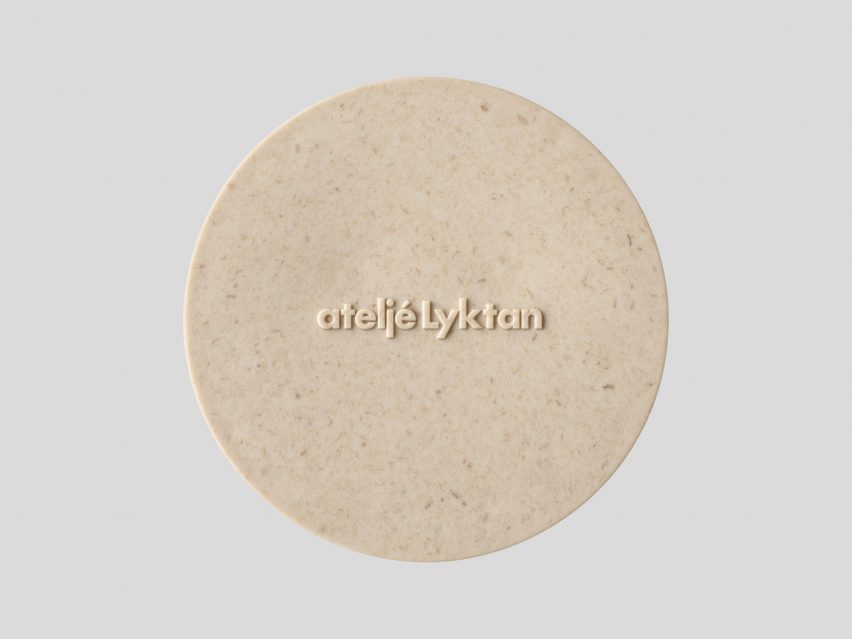
The dimmable Superdupertube features twisted louvres – an architectural detail that helps the light feel softer by angling the glare away.
“That’s why it’s a perfect workspace luminaire, it’s adapted to be better for the person sitting working and it’s also totally unique – it doesn’t exist on the market,” Gadd said.
The Superdupertube, which comes in four different lengths, has an organic beige colour with a natural pattern from the hemp and other ingredients.
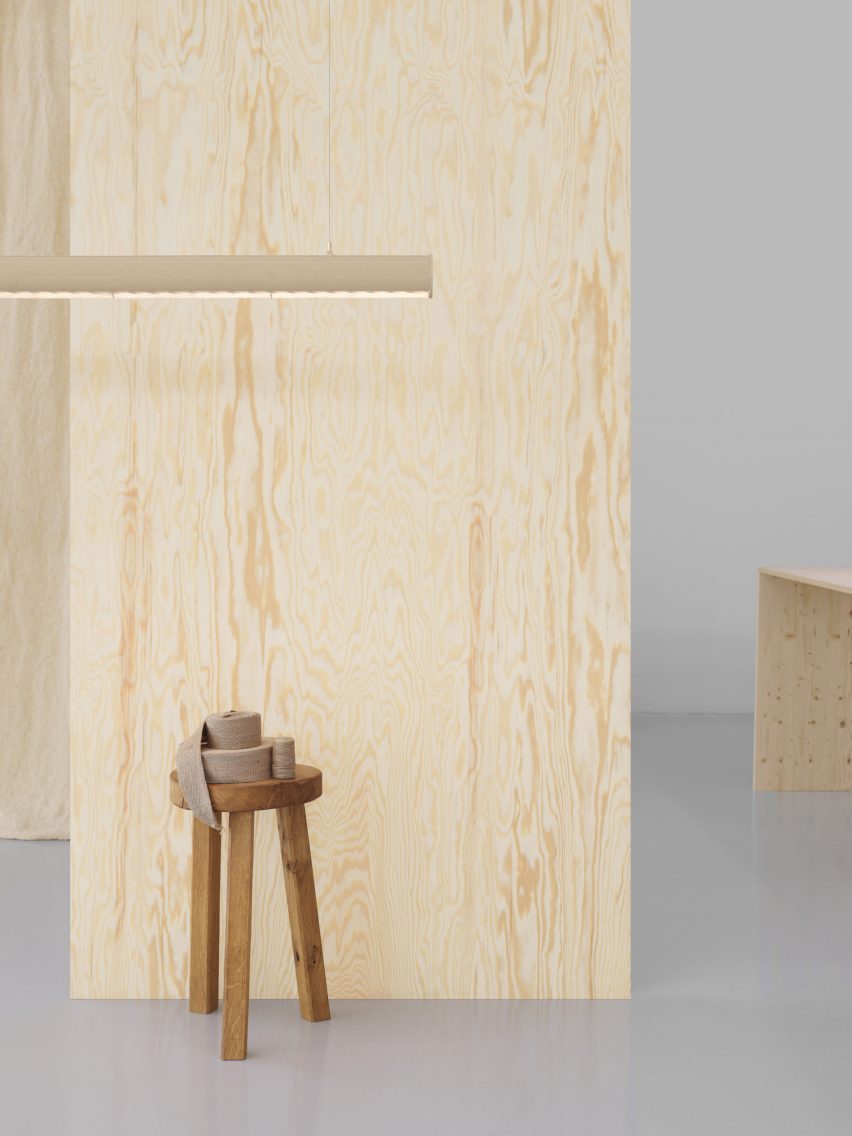
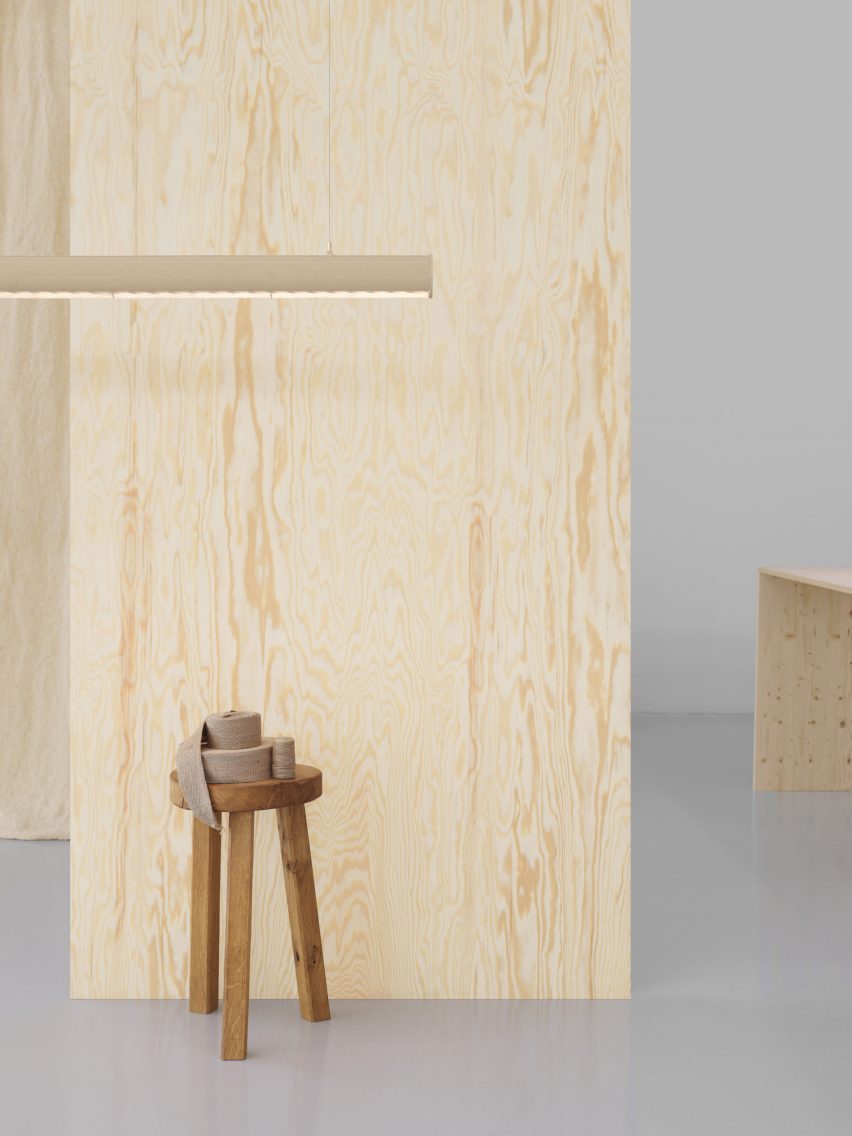
“We didn’t really know how it would look,” Osuldsen said. “The material is the colour of the hemp. And, of course, there’s probably something from the sugarcane because it’s heated up. It’s burnt sugar in a way.”
“So we get this specific colour and that also means that all of them will be a little bit different,” she added. “It’s all about the crops; if it’s a wet year or a dry year, the humidity in the material will be a little bit different. That’s why it’s sort of alive.”
Other recent Snøhetta projects include a glass-lined library in China designed to look like a forest and a hexagonal paving system for urban landscapes.
The photography is by Jonas Lindstrom unless otherwise stated.