From Float Glass to OLEDs: How Recent Advancements in Glass Technology Are Reshaping 21st Century Design
Architizer’s A+Product Awards celebrate the manufacturers at the forefront of material innovation. If your brand is innovating in product design for architects, consider entering today:
It might be hard to believe in today’s see-through society, but glass was once a scarce resource used sparingly in architecture. In the early years, glass was a medium for divine storytelling. The Sainte-Chapelle in Paris, a stunning structure completed in 1248, illustrates 1,113 scenes from the Old and New Testaments across a massive surface area of 6,888 square feet (640 square meters) of stained glass windows. Although beautiful, the windows were not decorative. They were an educational tool to teach religion to an illiterate population — 13th-century marketing at its very best.
By 1851, Joseph Paxton had designed and built The Crystal Palace for The Great Exhibition in London. With its vast expanse of plate glass panels and cast iron framework, the structure redefined the possibilities of architecture and design. As time and technology progressed, the float glass process (pouring the molten glass from a furnace into a chamber that contains a bed of molten tin), conceived by Sir Alastair Pilkington in 1959, was groundbreaking. It enabled the creation of large, uniform glass sheets that were less time-consuming to manufacture and more stable. The new process allowed glass to be seen as a structural element rather than a decorative addition.
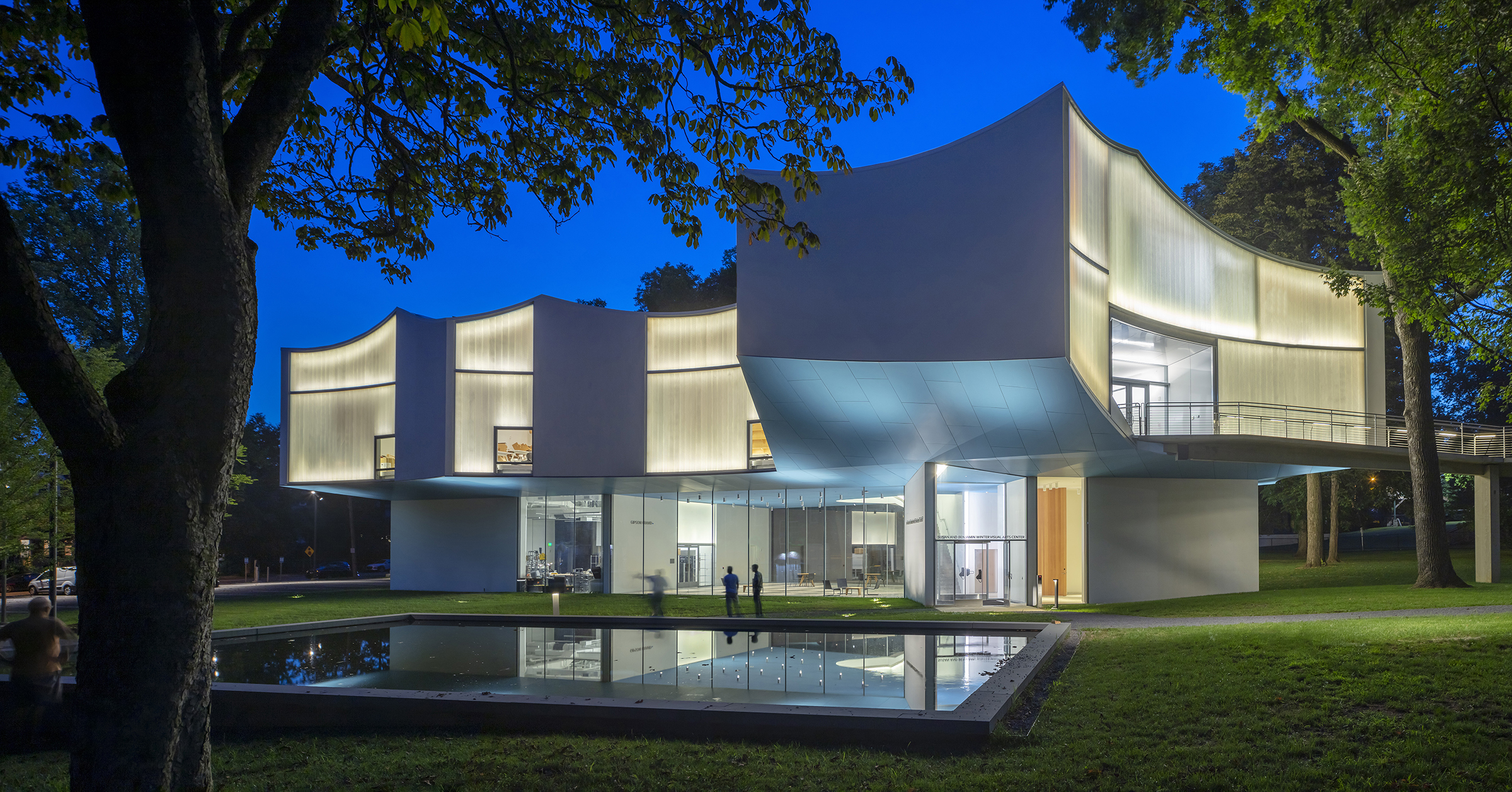
Double-Curved Channel Glass Walls by Bendheim. Finalist, 2022 A+Product Awards, Best of the Year, Architectural Design
By the time Modernism came into its own, a new vision of glazing was well underway — influenced mainly by the ever-experimental Ludwig Mies van der Rohe. Mies’s philosophy of “less is more” led to a minimalist aesthetic where glazing allowed architects to move away from the solid, enclosed walls of traditional design to a language of openness and fluidity. This work laid the foundation for the modern skyscraper and encouraged a shift towards integrating buildings with their environment, emphasizing nature and light. It was a pinnacle time for glazing advancement, and now, 100 years on, we are entering a new phase of glazing innovation.
The market for advanced glazing technologies is robust and expanding. Industry analyses, such as those conducted by Grand View Research, indicate that the global smart glass market, valued at USD 4.22 billion in 2020, is anticipated to grow at a compound annual growth rate (CAGR) of 6.8% from 2021 to 2028. This growth trajectory is propelled by the escalating demand for energy-efficient and technologically sophisticated building solutions. The market expansion reflects a broader architectural trend toward buildings that are not just structures but adaptive, energy-efficient systems.
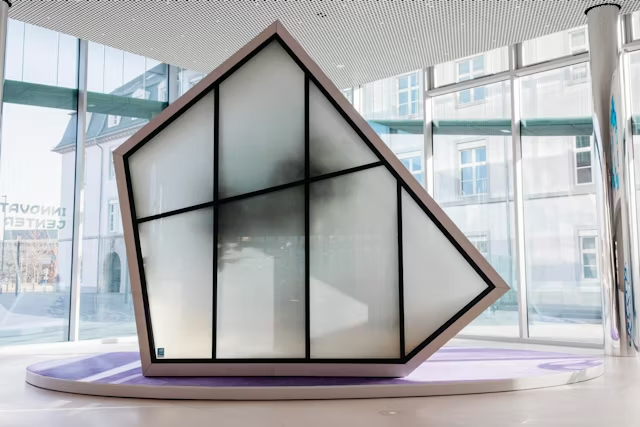
eyrise i350 Invisible Privacy Glazing by Merck KGaA. Jury Winner, 2022 A+Product Awards, Best of the Year, Health & Wellness
Smart glass technologies, like electrochromic glass, are at the forefront of such innovation. Using a minimal electrical charge, electrochromic glass can transition between transparent and opaque states, offering dynamic control over both natural lighting and privacy while significantly impacting energy efficiency. For instance, in its opaque state, electrochromic glass can block solar radiation, substantially reducing the need for air conditioning in buildings. According to a U.S. Department of Energy report, smart windows have the potential to save up to 20% in annual energy costs, marking a substantial stride in building energy efficiency through one of the most used materials in construction.
Sustainability is one of the key drivers in the evolution of glazing technologies, with an emphasis on integrating recycled materials into the production process being a priority. The use of cullet, or recycled glass, in glass manufacturing has been bolstered by new sorting and cleaning technologies that efficiently prepare the recycled glass for melting, causing less waste and using less energy.
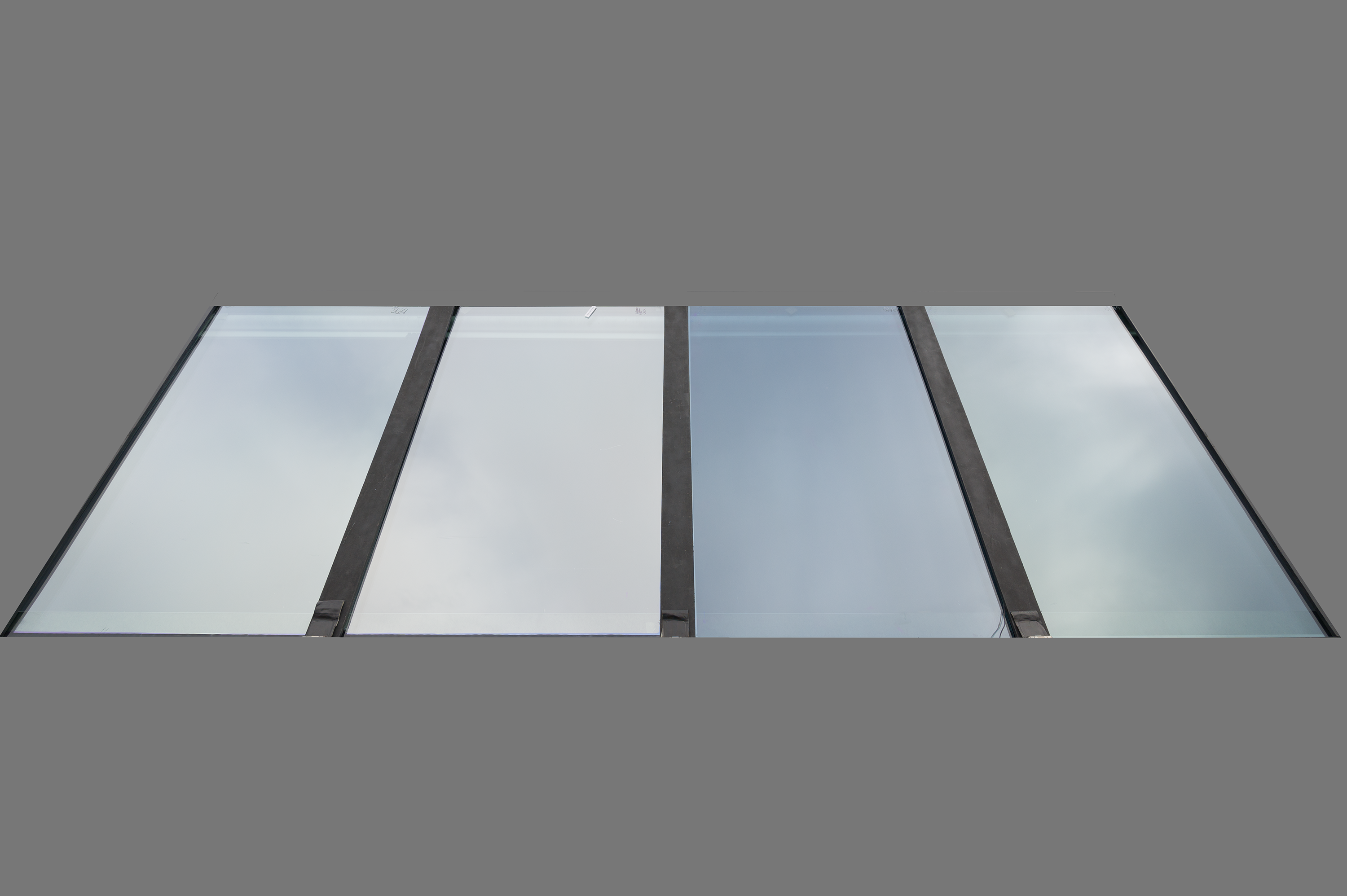
SunGuard SNR 50 coated glass by Guardian Glass. Popular Choice Winner, 2022 A+Product Awards, Façades & Openings, Glass & Glazing
Thanks to these new recycling techniques, coatings derived from recycled glass are being used more frequently. Low-emissivity (Low-E) coatings featuring microscopic layers of metallic oxides are becoming ever more popular. These glasses effectively minimize thermal transmittance while maintaining high levels of light transmittance. As do solar control coatings that selectively reflect infrared solar radiation, reducing heat gain and glare. In the context of urban design, these technologies lower heat absorption, thereby lowering ambient temperatures throughout our warming cities and reducing the urban heat island effect, a growing concern in densely populated cities.
Yet it’s not all about sustainability and climate. Multifunctional glazing solutions are reshaping the role of glass in architecture. These advanced solutions, integrating features like LED displays and touch-screen capabilities, are transforming windows from passive elements into interactive, multifaceted platforms. This transformation is underpinned by advances in optoelectronic engineering, enabling the integration of Organic Light Emitting Diodes (OLEDs) directly onto glass surfaces. These OLEDs provide energy-efficient, high-quality displays. Touch-screen functionality is achieved through the application of transparent conductive oxides (TCOs), which offer capacitive touch recognition without compromising the transparency of the glass.
Experts in the industry are highly optimistic about the potential of such technologies. With a simple touch, users can control lighting and privacy and have immediate access to information, making buildings more functional and adaptable.
Digital display glass provides a platform for real-time information dissemination; things like weather updates, service information, local points of interest, or even emergency alerts can be shown on the building itself. From a commercial perspective, digital display glass holds great potential, with it being used for advertising or showcasing products, offering business opportunities, and reaching broader audiences. Although advertising is a popular function, architects and designers have an opportunity to utilize this technology as a space for artistic expression, integrating digital art, animations, or dynamic visuals that can contribute to the aesthetic language of buildings.
Similarly, the integration of augmented reality (AR) and interactive features in smart glass technologies are pushing digital imaging and sensor technology. AR functionalities can be embedded in glass through the use of micro-projectors and transparent photovoltaic cells, allowing buildings to communicate and engage with occupants in unprecedented. This integration signifies a leap in the application of photonics and digital interactivity in architectural design, pointing towards a future where buildings offer not just shelter but dynamic, responsive environments.
In educational or public spaces, digital display glass and AR features can be used as a dynamic learning tool, displaying educational content, interactive exhibits, or historical information, enriching the learning experience and promoting knowledge while providing opportunities to increase accessibility in buildings, ensuring that everyone can benefit from the technology in a surreal revisiting of glazing’s original purpose from the 13th Century.
In essence, like much of our industry, glazing is witnessing a revolution marked by innovation, a commitment to sustainability, and a focus on enhancing human experiences. The enthusiastic embrace of these technologies by industry experts and leading architects underscores a shared commitment to innovating for a better, more sustainable, and aesthetically enriching future.
Architizer’s A+Product Awards celebrate the manufacturers at the forefront of material innovation. If your brand is innovating in product design for architects, consider entering today.