Buildings account for at least 39% of energy-related global carbon emissions on an annual basis. At least one-quarter of these emissions result from embodied carbon, or the carbon emissions associated with building materials and construction. The solutions for addressing embodied carbon in buildings have not been widely studied in the United States, leaving a significant knowledge gap for engineers, architects, contractors, policymakers, and building owners. Further, there is little information about the cost-effectiveness of reducing embodied carbon in buildings.
RMI’s new report, Reducing Embodied Carbon in Buildings: Low-Cost, High-Value Opportunities, helps fill this knowledge gap. The report demonstrates low- or no-cost options to reduce embodied carbon in buildings and provides design and construction strategies that can help limit a project’s embodied carbon. The case studies showcased in the report show an embodied carbon savings potential of 19% to 46% at cost premiums of less than 1%. Current practice indicates that we can achieve these reductions by specifying and substituting material alternatives with lower embodied carbon during the design and specification process. Far greater reductions are possible through a whole-building design approach.
This report was developed to help building owners, designers, contractors, and policymakers understand the low-cost and no-cost solutions for reducing embodied carbon in buildings. To accomplish that, we studied three building types and considered design strategies that can reduce embodied carbon at any stage of a project’s design and construction phases. The report quantifies the construction cost difference associated with low-embodied-carbon solutions and points to next-generation solutions that could drive even greater reductions.
Top categories of building materials for reducing embodied carbon.
Critical Materials Driving Embodied Carbon in US Buildings
In order to tackle embodied carbon in buildings, we first need to understand the carbon impact of the industries driving embodied carbon emissions. A building’s structure and substructure typically constitute the largest source of its up-front embodied carbon, up to 80% depending on building type. However, because of the relatively rapid renovation cycle of building interiors associated with tenancy and turnover, the total embodied carbon associated with interiors can account for a similar amount of emissions over the lifetime of a building. Our report focuses primarily on structural materials, metals (including steel and aluminum), cement, and timber. Each of these materials has a different embodied carbon content but is critical to our consideration of structural systems in this context.
Proven Solutions and Strategies to Reduce Embodied Carbon
Today, there are many solutions that can be leveraged to limit embodied carbon in new buildings. The totality of low-embodied-carbon solutions includes a long list of offerings that span a wide range of complexity.
Most simply, low-embodied-carbon solutions for buildings can be broken down into three main categories: whole-building design, one-for-one material substitution, and specification. In general, whole-building design solutions can drive the greatest embodied carbon savings. However, material substitution and specification can also result in substantial embodied carbon savings, especially when these solutions target carbon-intensive materials such as concrete and steel. Furthermore, these categories are not mutually exclusive — they can be combined or performed in parallel to drive deeper embodied carbon savings.
The following graphic demonstrates embodied carbon best practices that can be implemented throughout the building design and construction process.
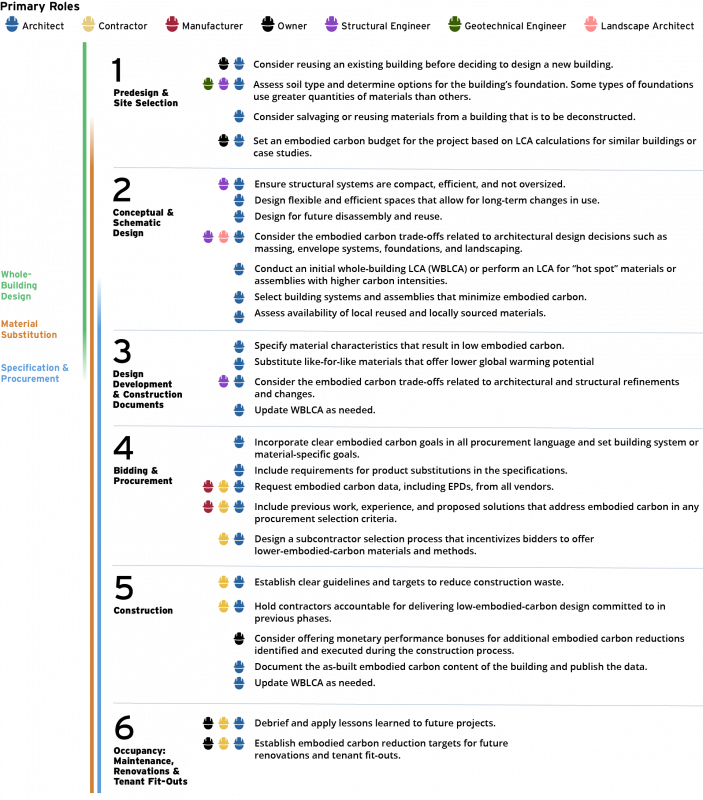
Case Studies in the Economics of Low-Embodied-Carbon Buildings
One core objective of the report is to answer the question: How much can we reduce embodied carbon in new buildings at no additional cost?
In short, this study shows that embodied carbon can be reduced by 19% to 46% in mid-rise commercial office, multifamily, and tilt-up-style buildings by leveraging low- and no-cost measures. Together, these measures increased overall project costs by less than 1%, which is within the margin of error for most construction project budgets.
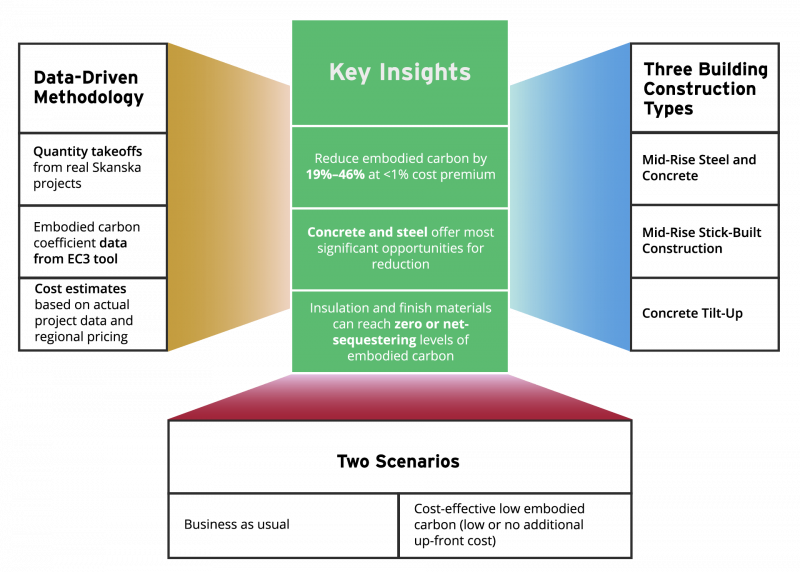
Skanska, one of the world’s leading sustainable construction firms, provided cost data from three actual projects in the Pacific Northwest and conducted an analysis under the guidance of RMI to generate the results of this study.
These case studies lead us to a few powerful observations. Even though the strategies employed do not include comprehensive, whole-building design strategies, they still yielded reductions of up to 46% in up-front embodied carbon through specification and material substitution measures. Given that these conclusions are based on three case studies in the Pacific Northwest, we can note them as strong anecdotal evidence, rather than broadly applicable conclusions.
Given the fact that we were not able to redesign building structural systems, we were unable to draw deep conclusions about the cost, carbon, and material impacts of whole-building design solutions, such as substituting more structural steel and concrete with wood. Given this scope, our key findings are:
- Optimizing the ready-mix concrete design can lead to significant embodied carbon reductions (14% to 33%) at no cost, or with a possible cost reduction in some cases.
- Rebar contributed up to 10% of total project embodied carbon in two case study buildings, but rebar’s up-front embodied carbon can be cut in half with minimal cost impact to the overall projects. These results may vary by location, as rebar with high recycled material content may not be available at a low cost premium in other regions.
- Insulation material selection can be a significant factor in project-level embodied carbon, with insulation making up approximately 20% of one building’s baseline embodied carbon content. Insulation products utilizing hydrofluoroolefin (HFO) or other foaming agents with low global warming potential can reduce embodied carbon impacts significantly, and several emerging plant-based products have the potential to store more carbon than is emitted in their production.
- Glazing remains a critical challenge for reducing embodied carbon, between the significant amount of heat required for glass production and the high-embodied-carbon materials often used for framing. Products available today can cut embodied carbon in glazing by approximately 25%, but at a 10% cost premium.
- For some finish materials such as flooring, carpet tiles, ceiling tiles, and paint, embodied carbon reductions of more than 50% are possible at no up-front cost premium. In some locales, carbon-sequestering materials may even be available.
Read the Report to Learn More
The Reducing Embodied Carbon in Buildings report includes detailed information about each of the three building case studies, sections exploring related topics such as tenant fit-outs and building reuse, and further analysis of our key conclusions. Download the report to learn more about opportunities for reducing embodied carbon in buildings, and why embodied carbon needs to be addressed now to drive the most impact.
Matt Jungclaus is Manager of Carbon Free Buildings at the Rocky Mountain Institute.