Layer rethinks bed design with Mazzu disassemblable mattress
British design studio Layer has aimed to bring sustainability to mattress design in a collaboration with Chinese start-up Mazzu, creating a modular, foamless product made up of textile-covered springs.
The Mazzu Open mattress was designed to have the comfort of a traditional sprung mattress while being adaptable, repairable and easy to pack down when moving house, so as to prolong the product’s life.
The design features row upon row of individually textile-wrapped pocket springs, which sit sandwiched between a base “matrix” and a cushioned topper to hold them in place.
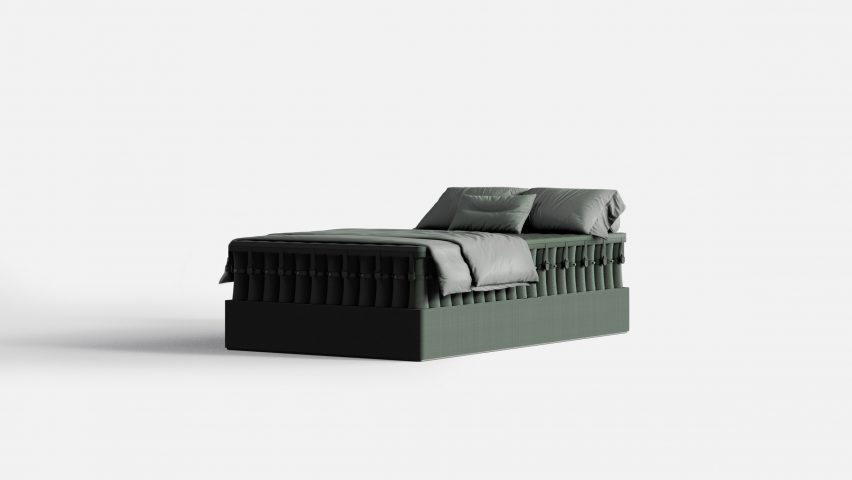
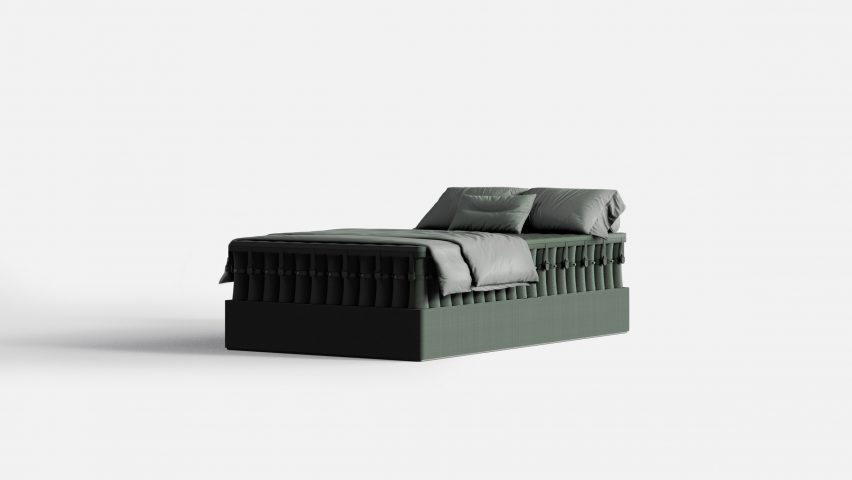
All its components are either recyclable or biodegradable, and no glue was used in the construction of the mattress.
The structure — left open at the sides for a distinctive, utilitarian look — also has the benefit of being hygienic, according to the studio, as users can check the inside of the mattress and take it apart to clean every element.
The modular design of the mattress means buyers can treat the springs like “pixels”, choosing between three levels of firmness for each point in the matrix to create a support pattern of their choosing. This also allows couples to customise their own side of the bed.
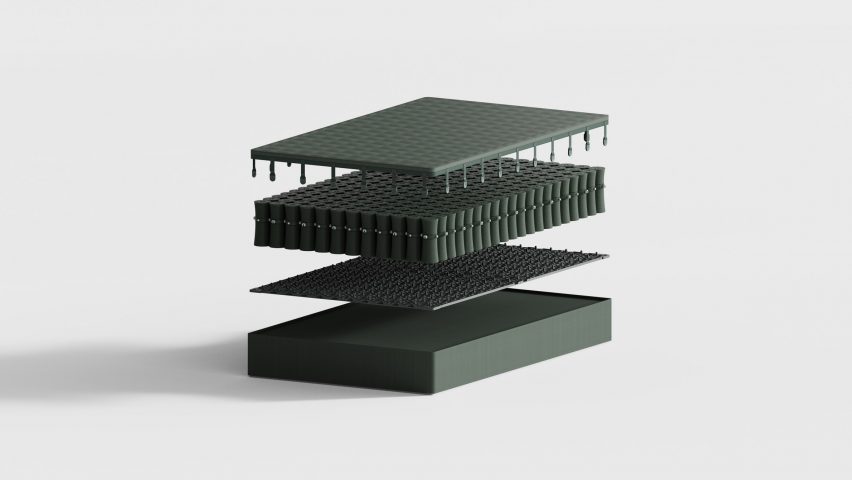
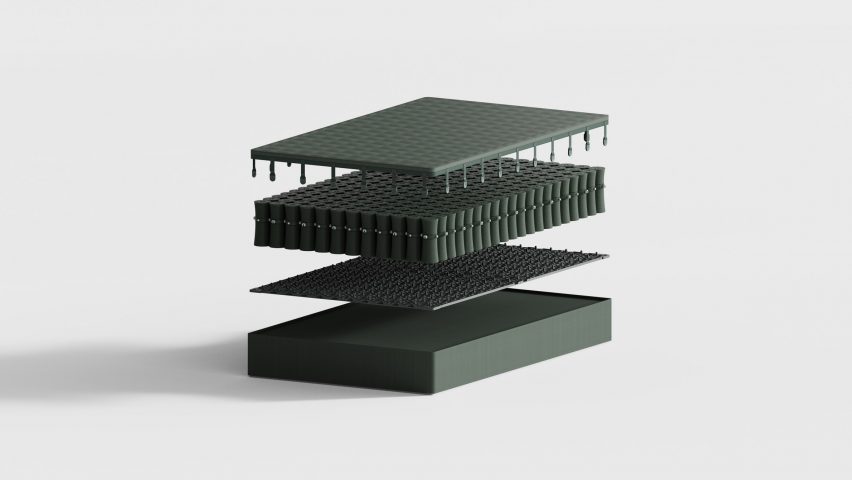
Additional spring modules and a different base and topper can be added to change the size of the mattress, and the whole kit can compress down to around 80 per cent of its size when disassembled.
The mattress comes in a reusable packaging system, also designed by Layer, that sees it divided into small components and split across several cartons, each weighing less than 10 kilograms. The spring modules compress from 250 millimetres to 50 millimetres in height as part of this.
Layer founder Benjamin Hubert told Dezeen that the studio tried to tackle multiple problems with current mattresses in one go with Mazzu, ranging from the impracticability of transporting them to the lack of customisation.
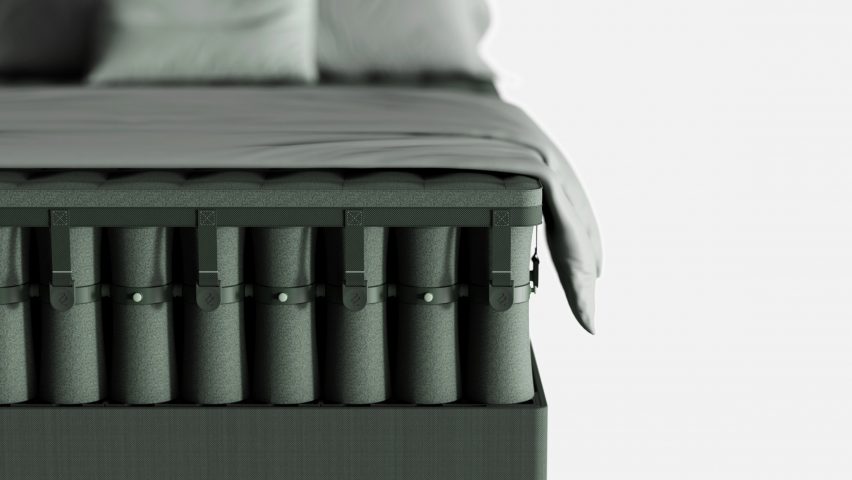
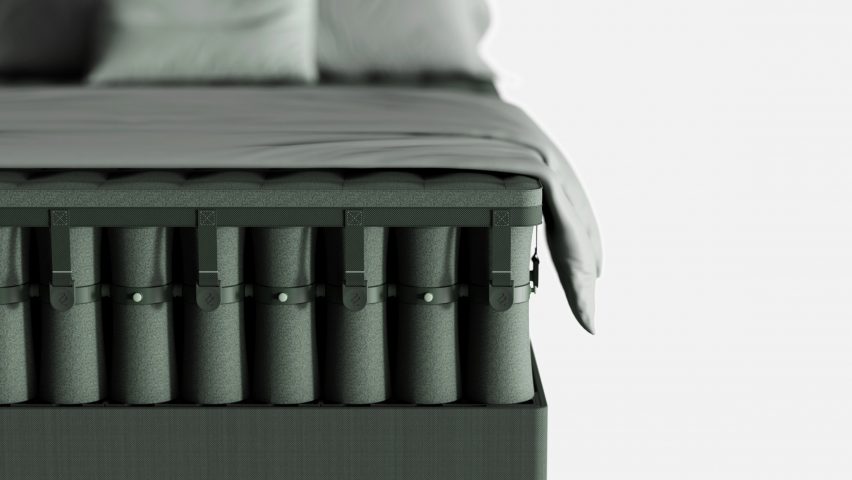
“They are too bulky once you unpack them and they ‘inflate’ from their compressed shipped form,” said Hubert. “They contain huge amounts of foam, which is next to impossible to recycle, and for the most part you can’t pack them down again for storage or transport.”
The studio wanted to avoid using polyurethane foam, a common mattress material, because as well as being difficult to recycle, it is energy intensive to produce and generates volatile organic compounds (VOCs) that are harmful to health.
The material is technically recyclable, but most mattresses do not reach the scarce recycling facilities, and they are often discarded before their time. In the UK, for instance, around 6.4 million mattresses are thrown away each year — about one for every ten people — and only around 14 per cent of them are recycled.
Instead of foam, the Mazzu Open mattress’s hourglass-shaped springs are shrouded in a two-tone 3D-knit polyester sleeve. The other materials used are steel for the springs, ABS plastic for the connection system and wool for the topper. The wool is biodegradable, while all the other materials are recyclable.
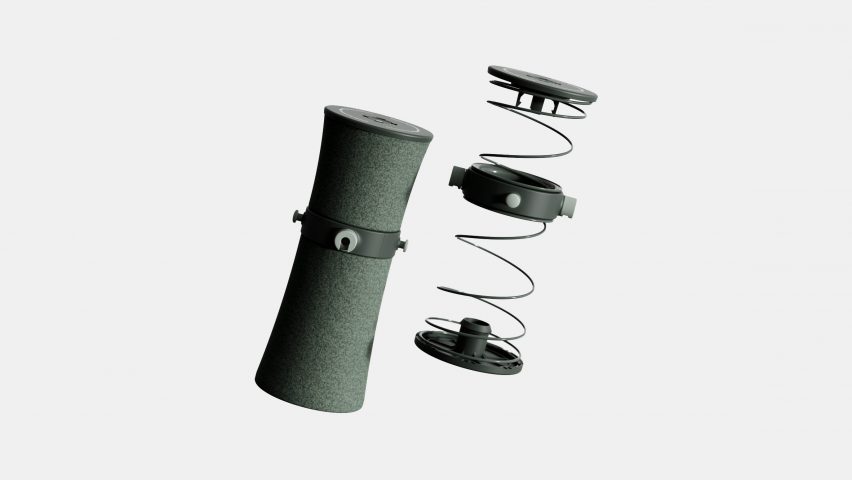
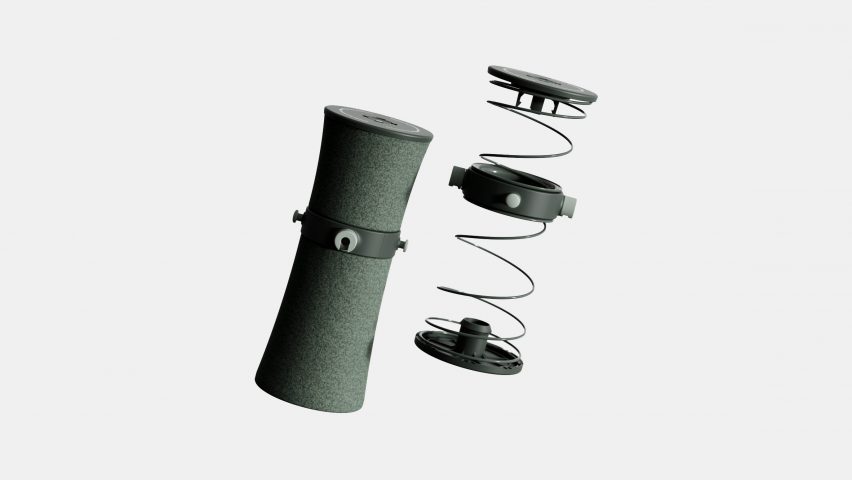
Hubert describes Mazzu as “leading the way” in delivering sustainable, high-performance bedding, and says the companies worked together for three years through the pandemic.
They went through many iterations of the mattress design in that time, as the studio tried to find a connection solution that would be both simple and comfortable.
“We must have tried about 20 different connection techniques,” said Hubert. “We had to find an optimum size that could be calibrated to fit all the standard mattress sizes too — not easy given there are a lot of international sizes.”
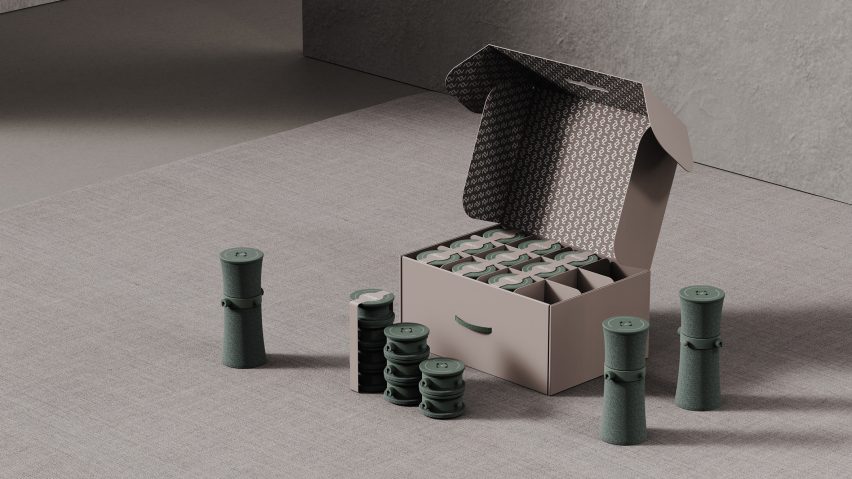
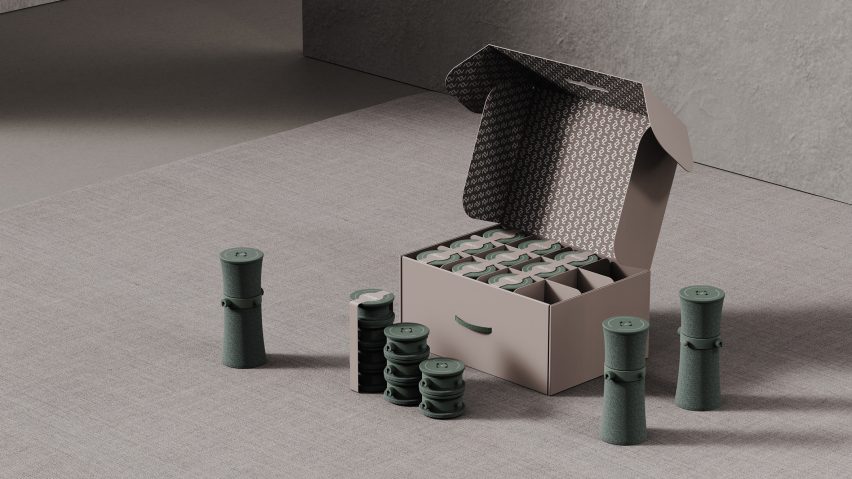
“The system needed to be highly cost-effective by using the least amount of parts and the simplest connection feature,” he continued. “The design of the connection systems changed dozens of times as we tested strength, ease of use, noise and comfort — we had hundreds of springs in the studio at times!”
Other recent designs from the London-based design studio have included sustainable dog toys for Canadian company Earth Rated and a green hydrogen vehicle retrofitting system for US start-up Croft.
Mazzu and Layer launched the Mazzu Open mattress at the German furniture fair IMM Cologne, which was held from 14 to 18 January. See Dezeen Events Guide for an up-to-date list of architecture and design events taking place around the world.