Human vs. Machine: Striking the Balance With AI in Architectural Design
Architizerâs Tech Directory is a database of tech tools for architects â from the latest generative design and AI to rendering and visualization, 3D modeling, project management and many more. Explore the complete library of categories here.
‘Will artificial intelligence (AI) replace architects?’
This question has been at the forefront of several discussions that have been vibrantly presenting many dystopic scenarios where big data, algorithms and machine learning will eventually replace human creativity and intuition. However, AI technology existed long before the AI bloom, rarely causing excessive panic within creative fields. So why is AI technology suddenly so threatening to the architectural profession?
Looking back at science fiction movies, AI was oftentimes presented as a human avatar that could accomplish assignments, make calculations and provide insightful information in unprecedented speeds. Nevertheless, it never performed extremely creative tasks. It was always depicted as a trusted artificial “advisor” capable of processing large amounts of data and automate complex procedures.
When platforms such as Midjourney, DALL-E and Stable Diffusion were introduced to the world, the creative skills and intuition necessary to visualize spaces and settings were abruptly redefined. Consequently, AI technology became a tool for generating impressive compositions and rapid design prototyping through the use of simple text prompts, eliminating the need for manual drawings or an overall architectural knowledge.
At the same time, a different set of tools was developed. AI apps such as qbiq and Laiout have the ability to process data, thus optimizing building sustainability and offer design solutions that are in accordance with local building codes. This type of AI software follows the more familiar pattern of speedy data processing, resulting in designs based purely on logical thinking. For the architectural profession, making this distinction between “creative” and “logical” AI algorithms is crucial.
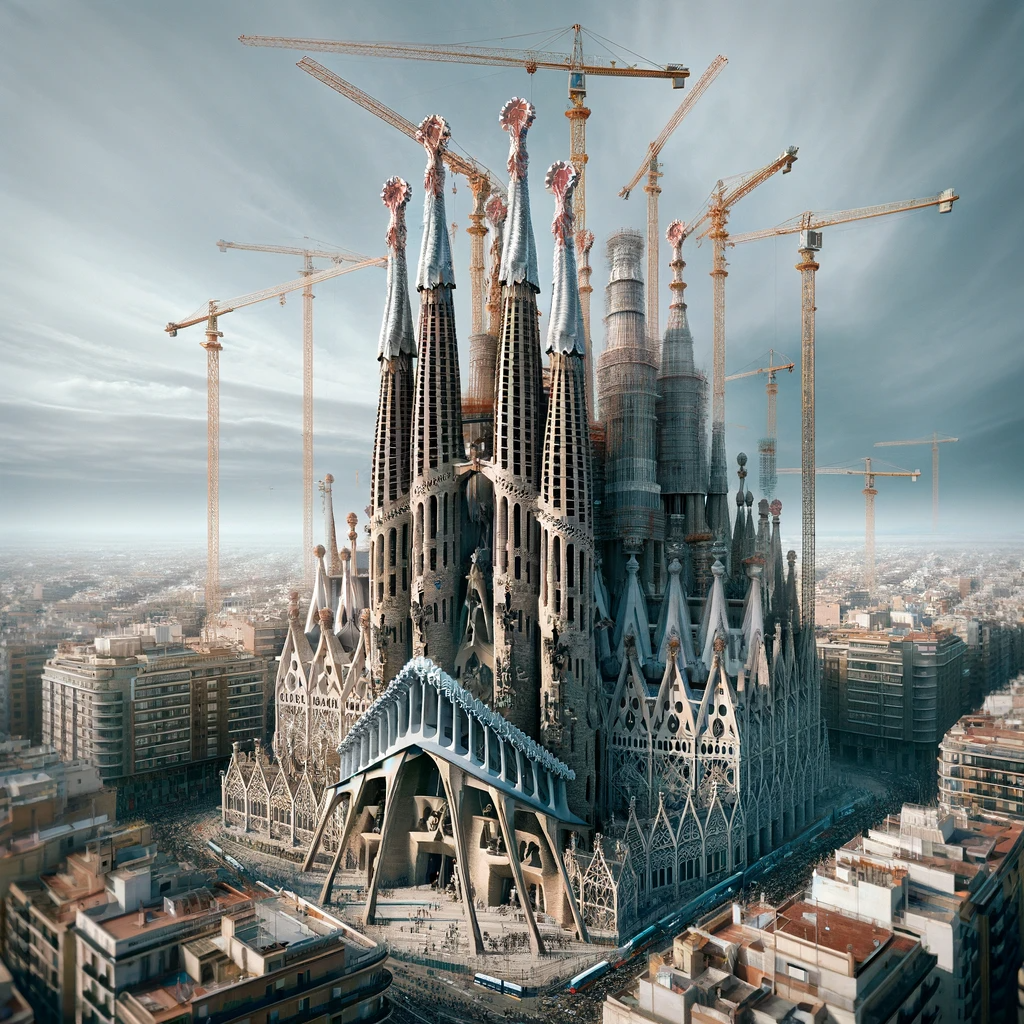
ChatGPT 4.0, Dall-E 3.0, Photo of the Sagrada Família in Barcelona, by ChatGPT 4.0, Dall-E 3.0 (2024), CC0 1.0
Architizer’s new Tech Directory aggregates tech tools for architects, allowing you to search, compare and review AI softwares before selecting which to you in your next project:
Explore Architizer’s Tech Directory
On the one hand, even though “logical” AI tools are able to generate countless design iterations based on predetermined parameters, they lack the nuanced understanding of cultural context, emotional resonance, and human experience. There’s also a risk of homogenization, where buildings designed by AI algorithms may lack the diversity and richness that stem from individual human perspectives and cultural influences. Another challenge lies in the inherent biases embedded within AI algorithms.
Machine learning models are trained on historical data, which may reflect societal biases and perpetuate inequalities in architectural design. Without careful oversight and intervention, AI algorithms could inadvertently reinforce existing biases related to race, gender, socio-economic status, and accessibility, leading to inequitable outcomes in the built environment. Admittedly, the risks associated with data-driven AI technology and architectural design are well-known and somewhat obvious. In such a subjective discipline, logic alone is not enough to create spaces that are truly regarded as pieces of architecture. Design is partially an instinctive process that is unique for each individual architect and cannot be replicated by any intelligent machine.
“Creative” AI algorithms, however, pose a different type of challenge since they bring an ‘unpredictability factor’ to the table. Instead of relying purely on data, text-to-image generators produce designs based on subjective (human generated) prompts. Instead of spending numerous hours sketching, drawing and model making, “creative” AI apps can generate countless concepts in a matter of seconds by simply feeding them client briefs. Nevertheless, while they seem ideal for producing impressive concepts for early stage design, the images they create are fairly fictional. Ironically, they lack data.
Even during the initial brainstorming phase, architects do consider an array of objective as well as subjective information regarding their project. From climatological site conditions to potential present or future occupants and even immaterial data such as past histories, myths or cultural norms. This framework of complex interrelationships becomes the blueprint for designing for specific sites, people and cultures, adopting a holistic approach towards proposing creative and innovative solutions.
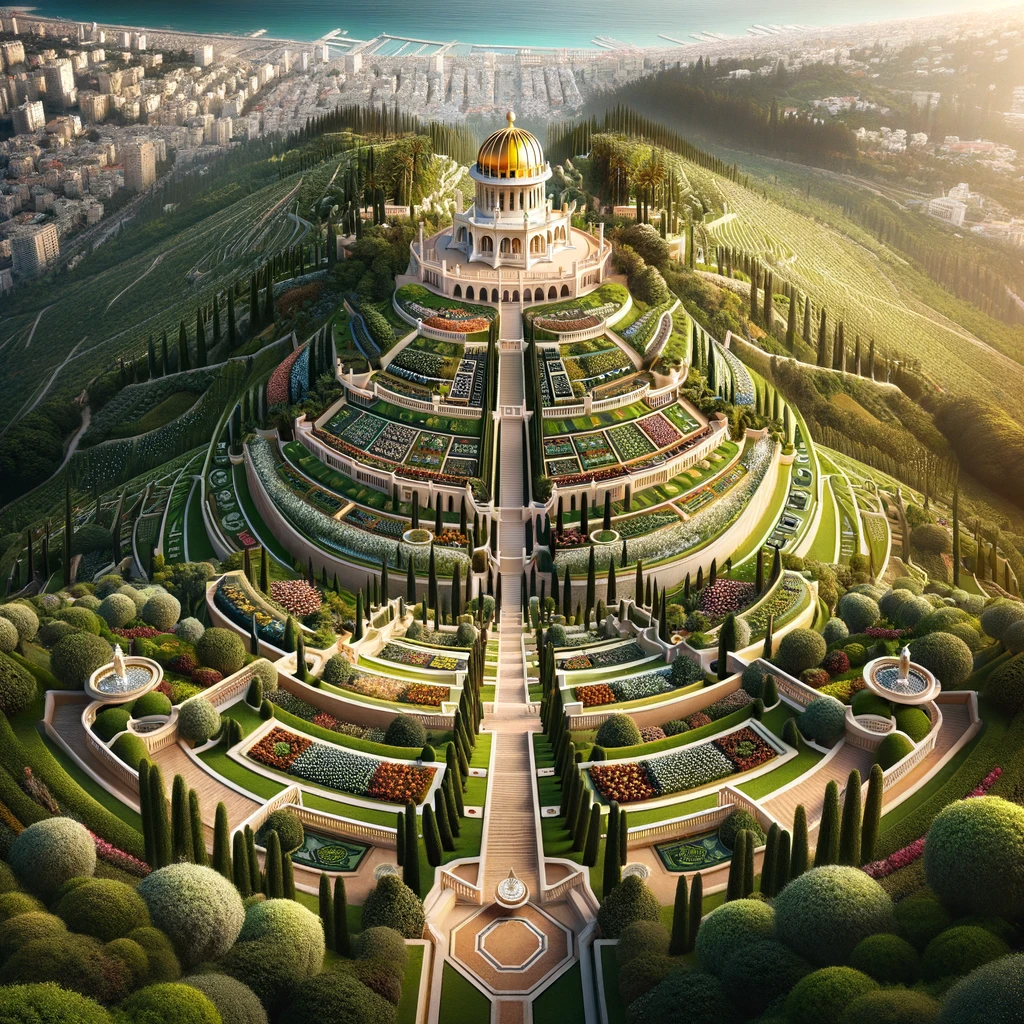
ChatGPT 4.0, Dall-E 3.0, Aerial photo of the Baha’i Terraces in Haifa, by ChatGPT 4.0, Dall-E 3.0 (2024), CC0 1.0
There is no doubt that both “logical” and “creative” AI algorithms have become ‘trusted advisors’ for many architects. “Creative” AI tools are ideal for showing design intention, representation and visualization. In other words, they bridge the communication gap between architects and clients. In parallel, “logical” AI tools can rapidly access and process information such as planning codes or material specifications and energy reports. During the technical and construction stages, many AI apps can automate processes and produce standardized drawings seamlessly and with minimal effort.
In short, both types of AI tools are two sides of the same coin, showing both promise and peril. Still, as long as architects are aware of AI limitations, integrating the technology into their workflow can provide valuable insights and inspiration, inform decision-making and ultimately enhance the practice of architecture. Architects have always been the mediators between logic and creativity, with AI being no exception. This paradigm shift presents an opportunity as well as a challenge, which — if navigated correctly — will enable architects to focus on what they do best: creating innovative, human-centered and culturally significant spaces.
Architizerâs Tech Directory is a database of tech tools for architects â from the latest generative design and AI to rendering and visualization, 3D modeling, project management and many more. Explore the complete library of categories here.