Reef Rocket is a bio-cement reef grown from plant enzymes
Industrial designer Mary Lempres has created a bio-cement structure developed to mimic naturally occurring oyster reefs that tackle coastal flooding, filter seawater and promote biodiversity.
Called Reef Rocket, the structure comprises a duo of bio-cement modules with ridged surfaces that can be stacked in two directions and create a rocket-like shape when assembled.
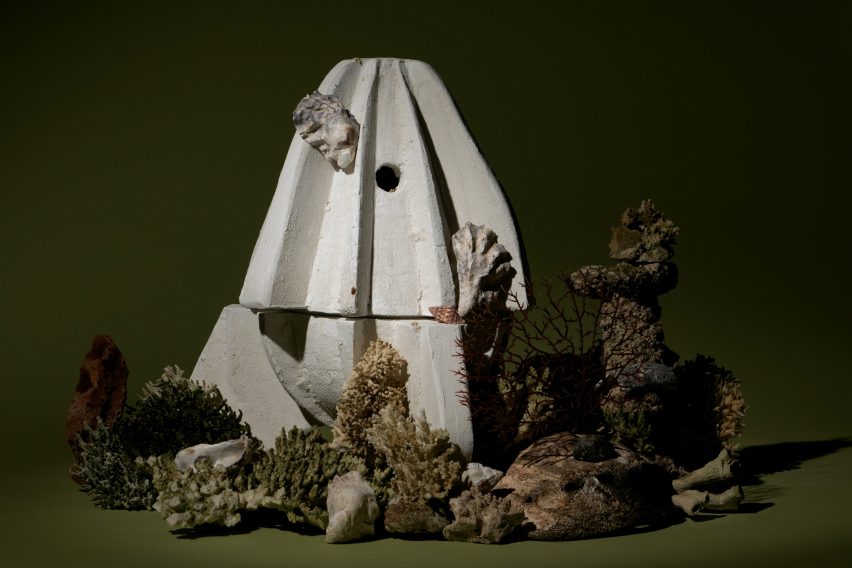
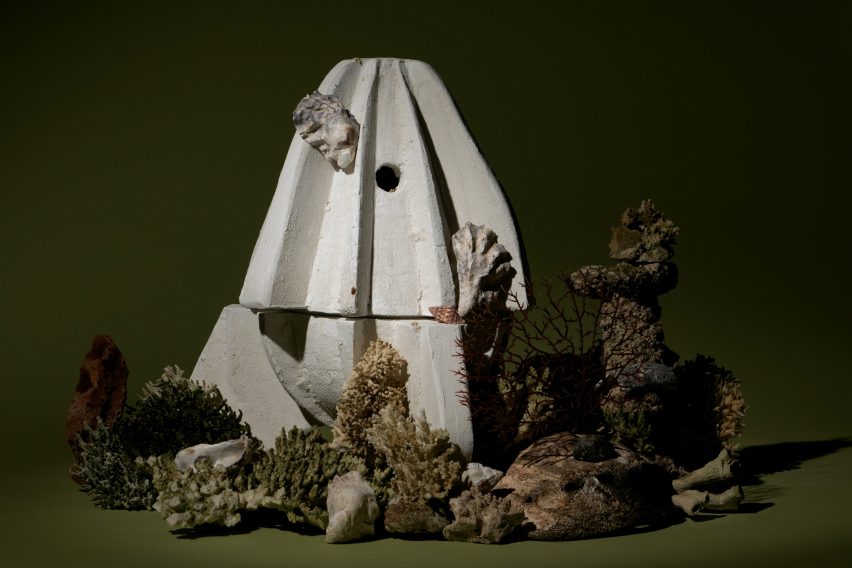
Norwegian-American designer Lempres drew on biomimicry for the project, a practice that looks to nature to solve human design challenges.
The ridged modules were created to be placed underwater and emulate coastal oyster reefs, which naturally filter algae from seawater as well as attract and provide shelter for other aquatic organisms.
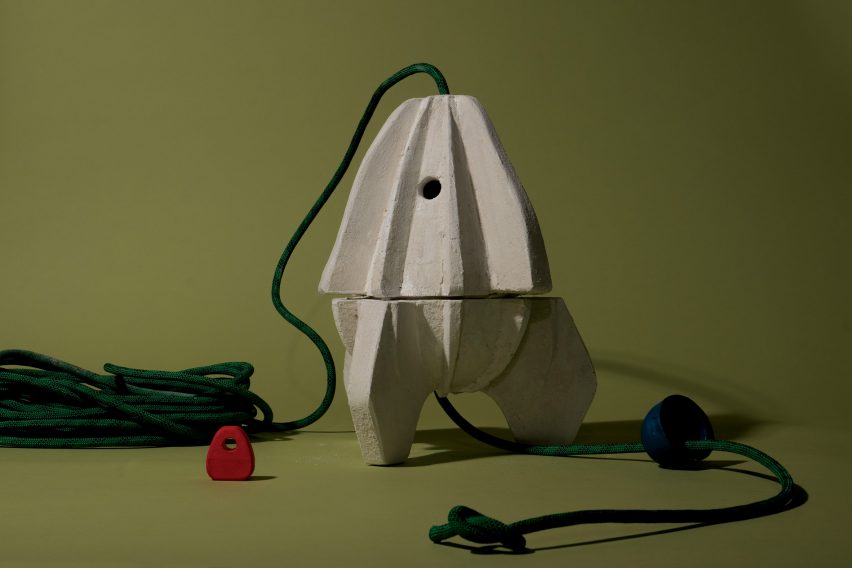
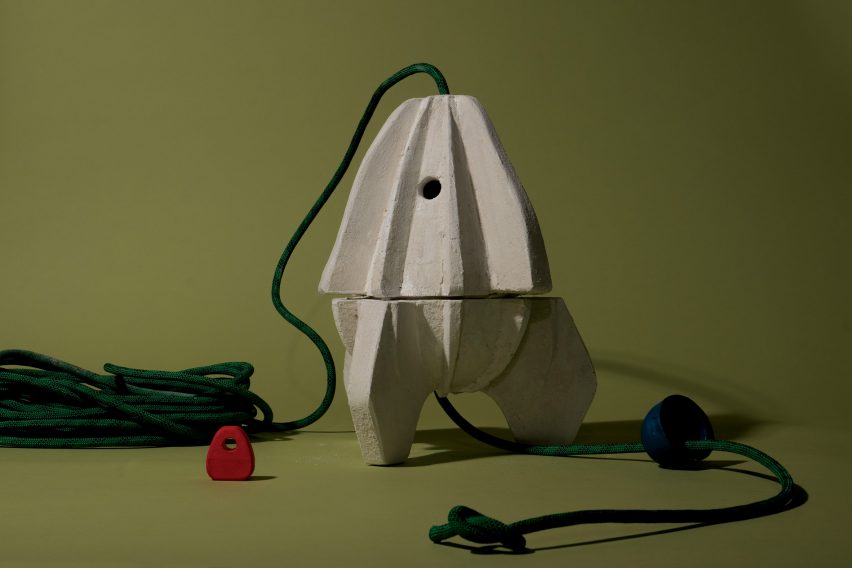
Oyster reefs also dissipate wave energy, mitigate storm surges and manage eroding coastlines, explained the designer.
Lempres collaborated with bio-geotechnical specialist Ahmed Miftah to develop a method for growing plant-derived cement that makes up the modules, which she described as “similar to the irrigation systems required for growing a plant”.
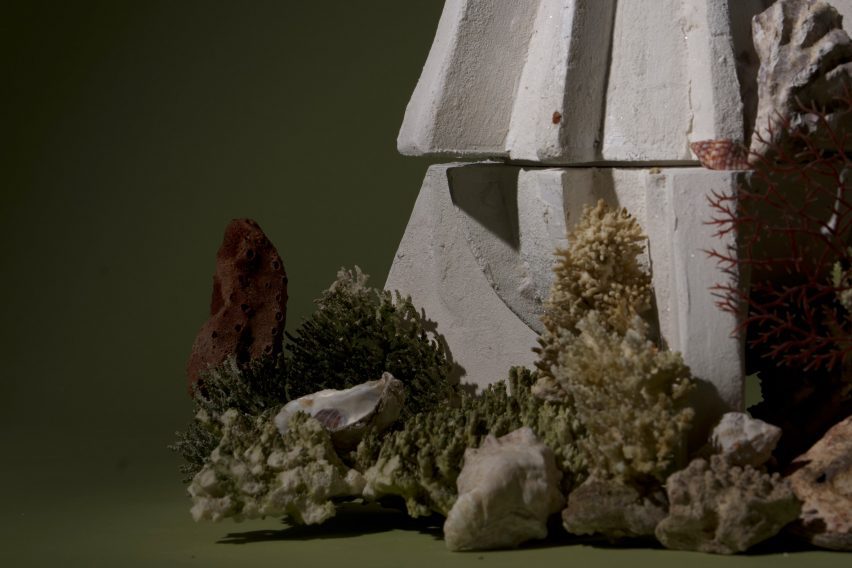
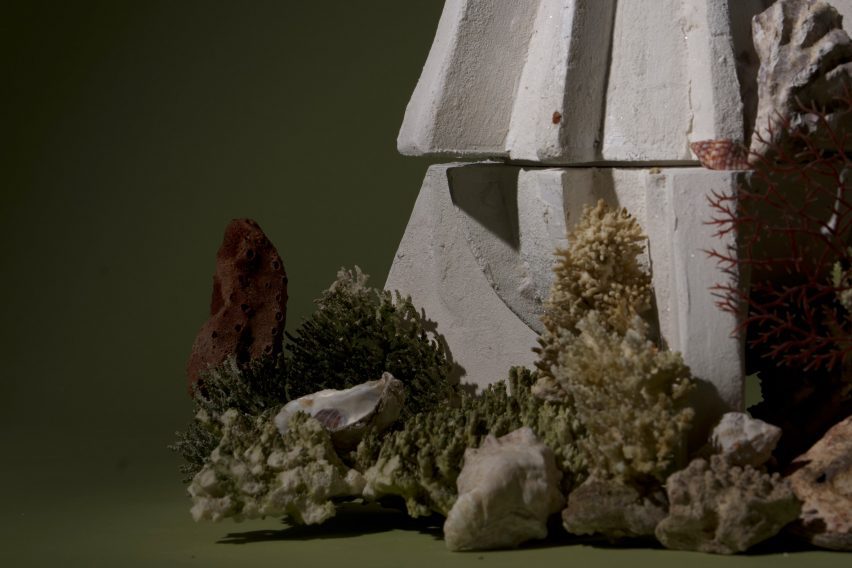
The pair poured a bio-based, non-toxic solution containing a crude extract from globally grown plants over crushed aggregate.
Sourced in New York City, the aggregate was created from crushed glass and oyster shells salvaged from local restaurants and New York Harbour.
“The packed substrate grows similarly to a plant,” Lempres told Dezeen.
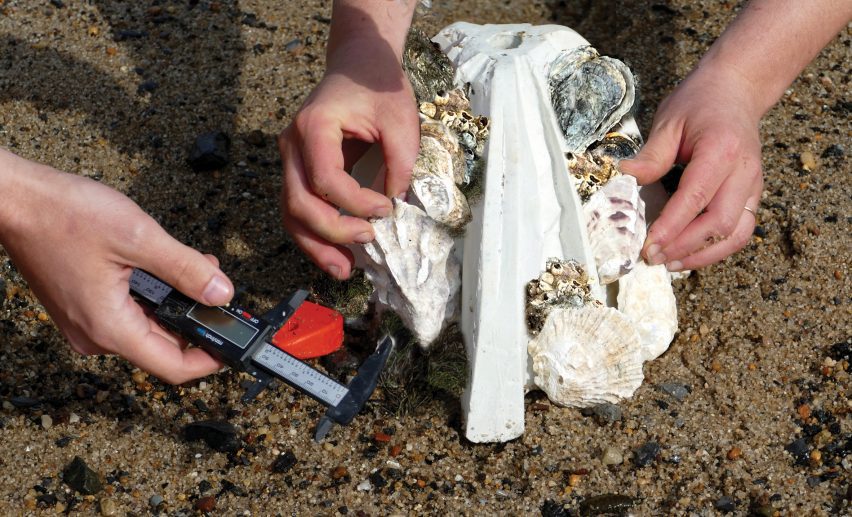
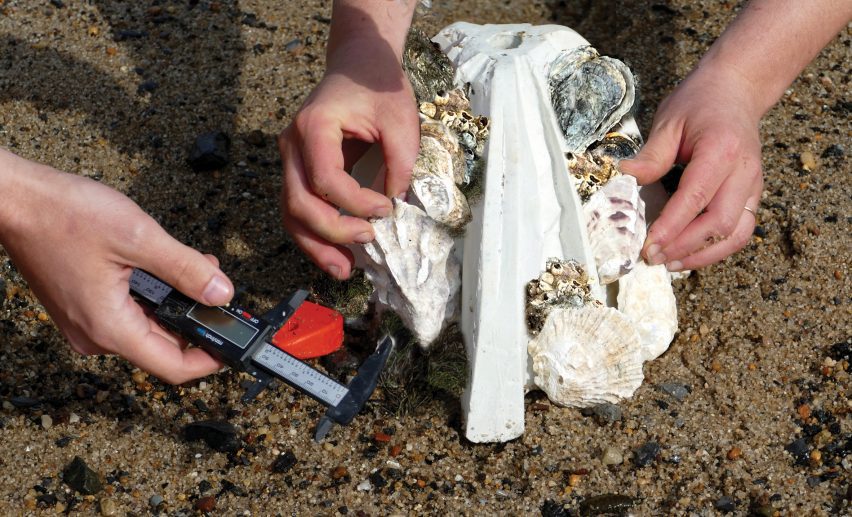
Saturated for three to nine days, the substance becomes natural concrete after the extracted biocatalyst causes minerals to form “mineral bridges” between the glass and shell waste.
“The resulting product is water-resistant, durable and comparable with standard concrete containing the same amount of aggregate,” explained the designer.
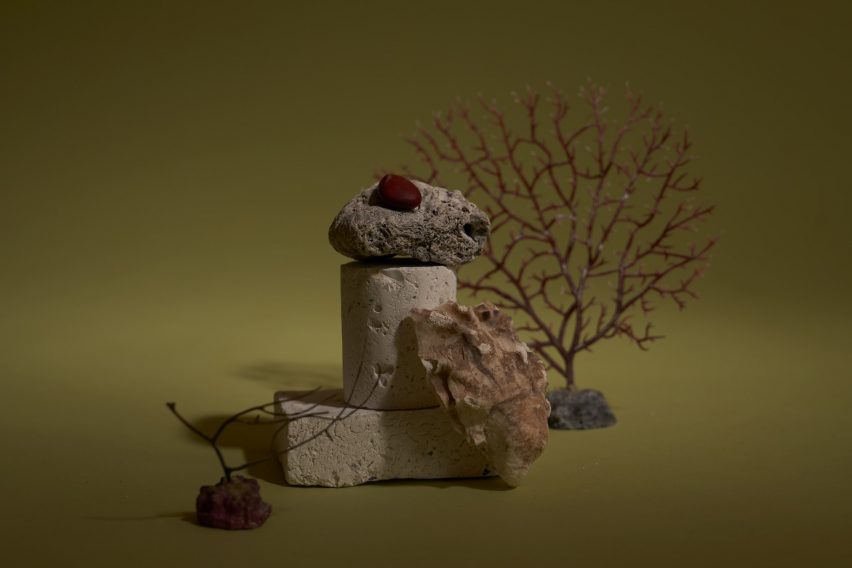
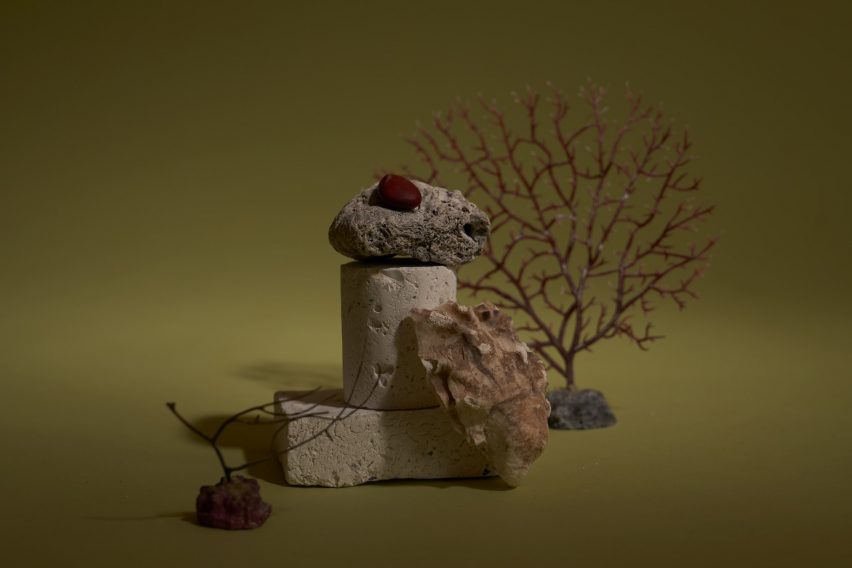
“It can be grown in any environment without heat or otherwise burning fossil fuels and is derived from waste products, making it an affordable and scalable alternative to cement,” she continued.
“Bio-concrete is chemically identical to the material oysters produce to grow their reefs. The key difference is the bio-concrete we’ve developed grows in just several days, while oyster reefs take millennia to grow.”
This process closely mimics the natural processes that occur when oyster shells and coral reefs are grown, according to the designer.
“I was inspired by the ability of this reef-growing material to withstand extreme wave energy and corrosive saltwater,” she said.
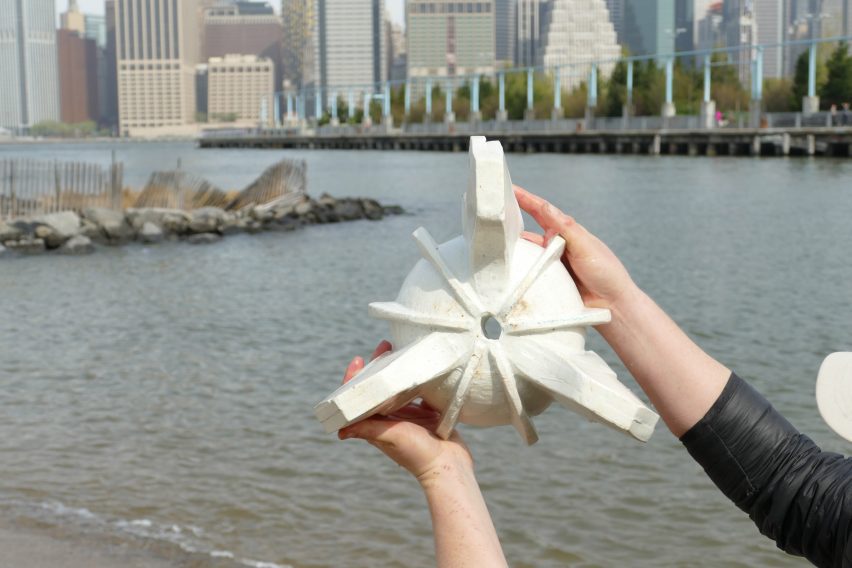
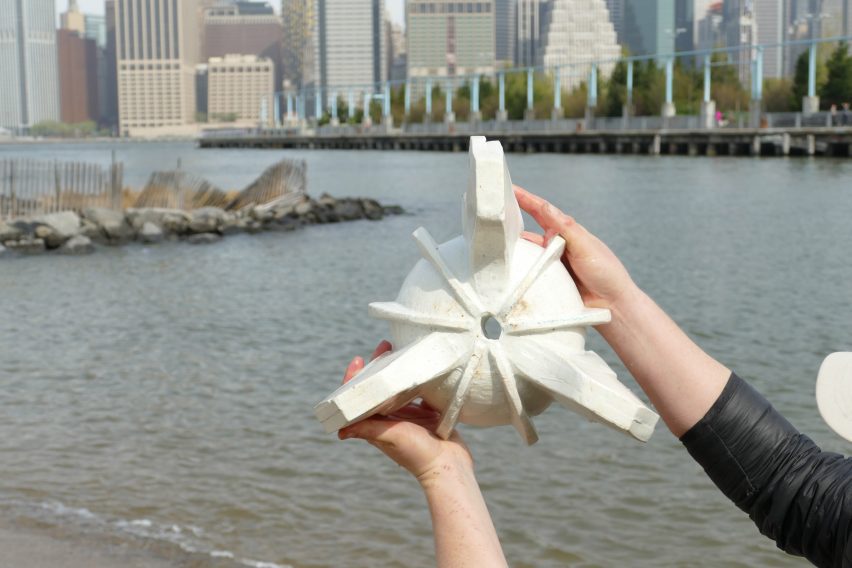
When creating the modules, Lempres and her team made “hundreds” of prototypes.
Eventually, they settled on prefabricated moulds, which the bio-cement can be packed into and set – “like sand” – without the need for heat or chemicals.
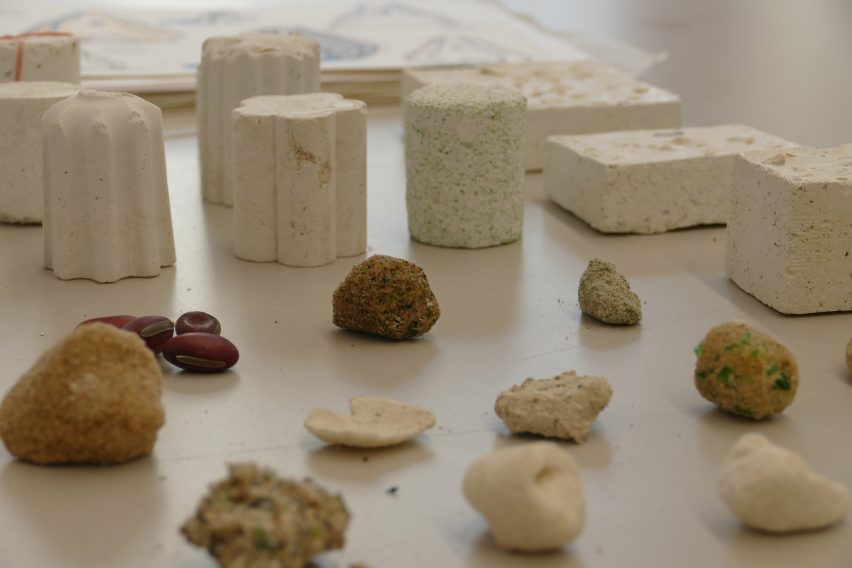
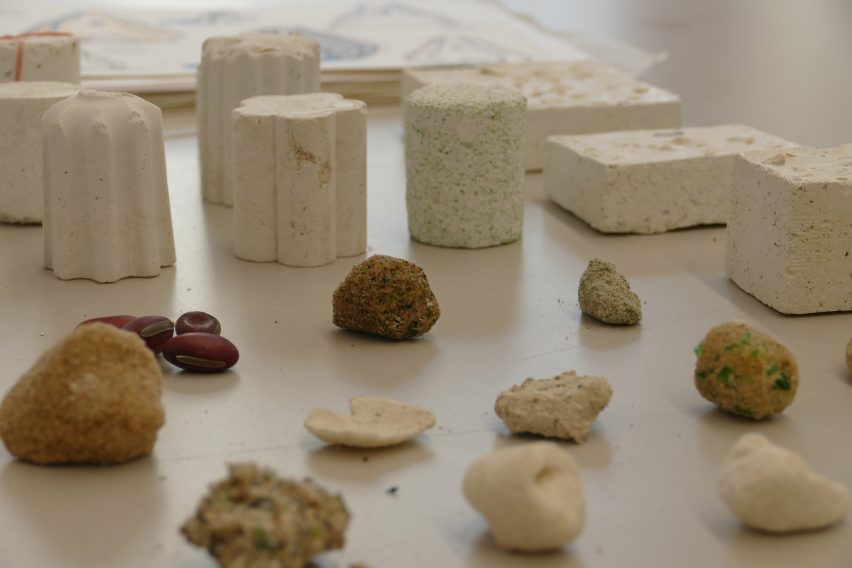
Reef Rocket was deliberately developed to be small in size, lightweight and easy to assemble, making the design accessible to as many people as possible, according to the designer.
“Nature has the incredible ability to grow intricate and durable material, like shells and coral, without polluting its surrounding environment,” said Lempres.
“Reef Rocket harnesses the natural process of growing durable minerals to re-grow vital reef structures, benefiting humans and our ecology from the worsening effects of climate change,” she added.
“This paves the way for a future where hard and durable material can be grown like a crop, regenerating waste rather than polluting our environment.”
Previously, US design workshop Objects and Ideograms conducted a research project that involves 3D printing with calcium carbonate to create sustainable underwater “houses” for coral reefs and marine life to grow. Chinese materials company Yi Design developed a porous brick made from recycled ceramic waste that could be used to prevent flooding in urban areas.
The photography is courtesy of Mary Lempres.