Barbican’s Unravel exhibition explores the subversive power of textiles
Curator Lotte Johnson discusses the transformative power of textiles in this video produced by Dezeen for the Barbican’s latest exhibition.
Titled Unravel: The Power and Politics of Textiles in Art, the exhibition examines how textiles have been employed to explore themes spanning power, oppression, gender and belonging.
It features over 100 works that make use of textile, fibre and thread from over 50 artists from across the globe, spanning from the 1960s to the present day.
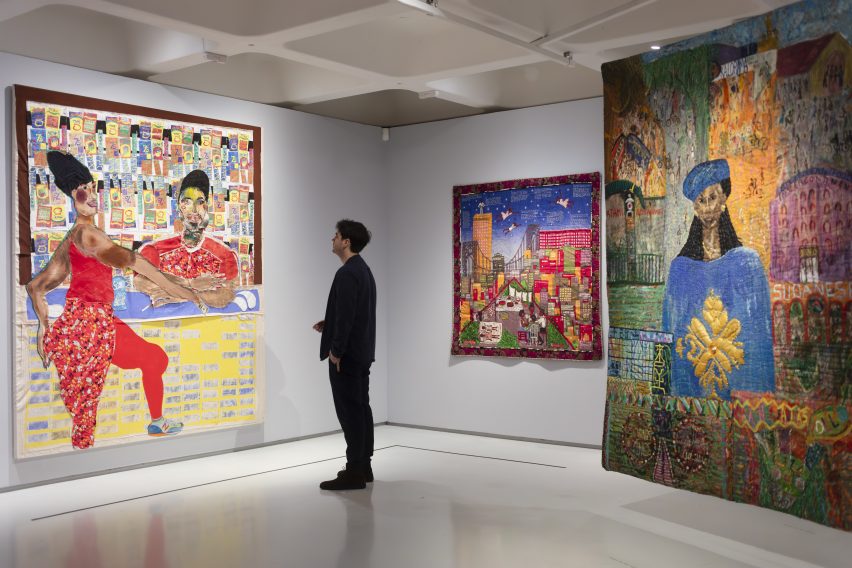
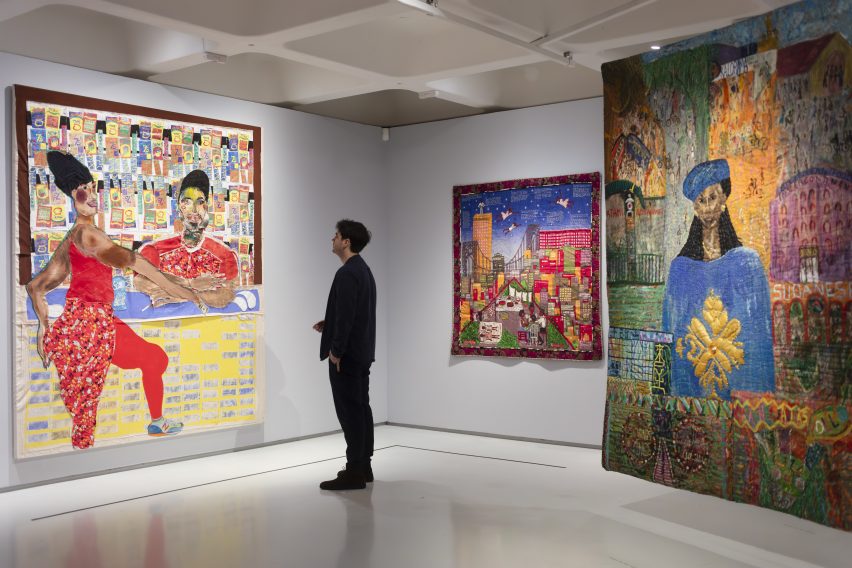
The exhibition is designed to challenge the perception of textiles being solely domestic or craft practices and instead features textile works that relate a story of resistance and rebellion as well as pieces that present narratives of emancipation and joy.
Johnson explained that textiles offer a meaningful medium to express personal and political issues due to their tactile nature and intimate connection to daily life.
“Textiles are one of the most under-examined mediums in art history and in fact history itself,” Johnson said. “They are an intrinsic part of our everyday lives. When we’re born, we’re shrouded in a piece of fabric. Everyday we wrap ourselves in textiles,” she continued.
“They’re really this very intimate, tactile part of our lives and therefore perhaps the most intrinsic, meaningful way to express ourselves.”
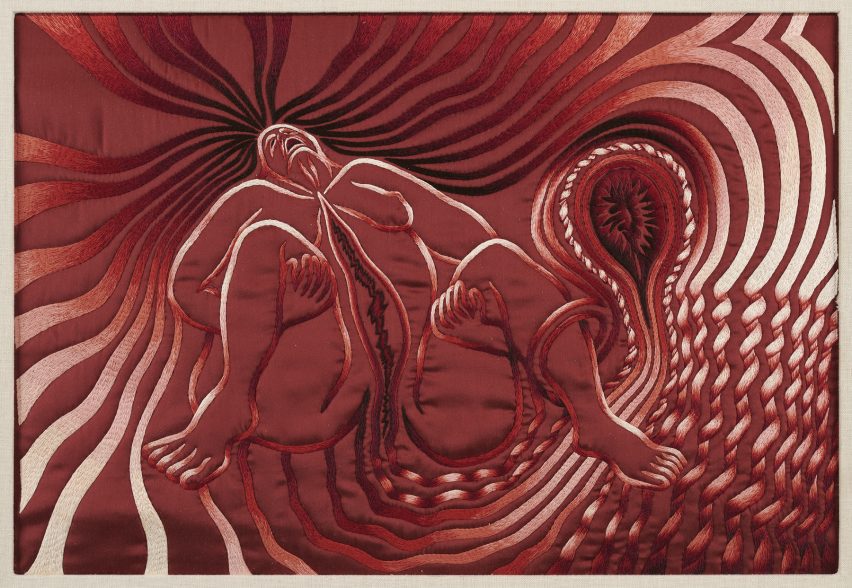
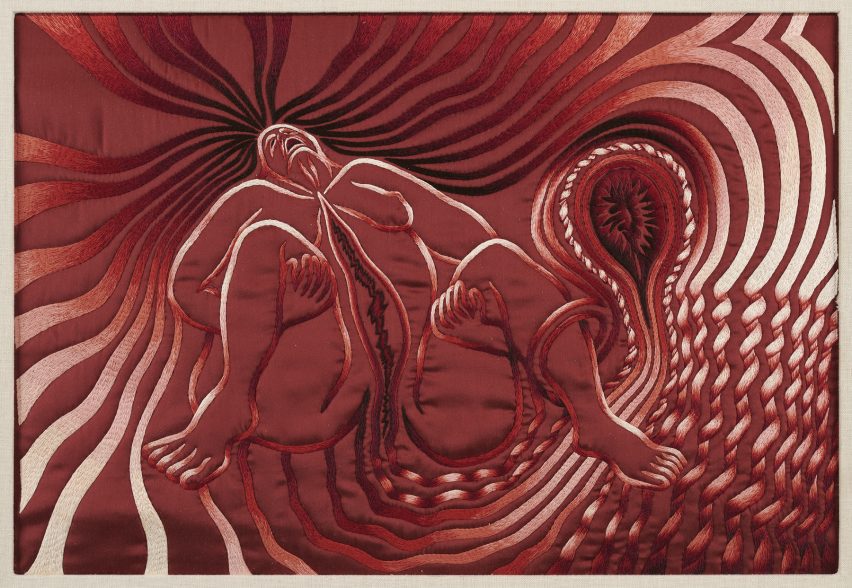
The exhibition is structured into six thematic sections. The first, called Subversive Stitch, presents works that challenge binary conceptions of gender and sexuality.
The section includes feminist artist Judy Chicago’s Birth Project, which vividly depicts the glory, pain and mysticism of giving birth, as well as a piece from South African artist Nicholas Hlobo, which, despite initially appearing as a painting, is made using ribbon and leather stitched into a canvas.
Another section of the exhibition is titled Bearing Witness, which brings together artists who employ textiles to confront and protest political injustices and systems of violent oppression.
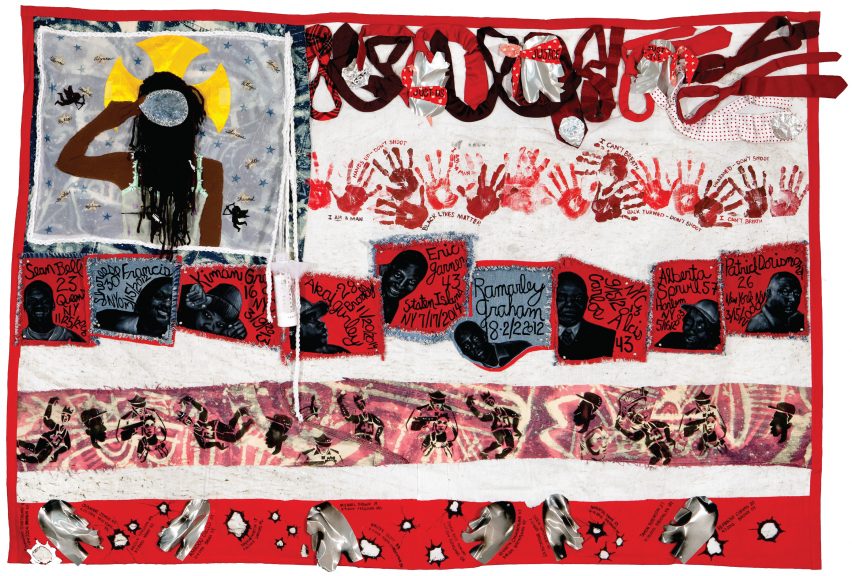
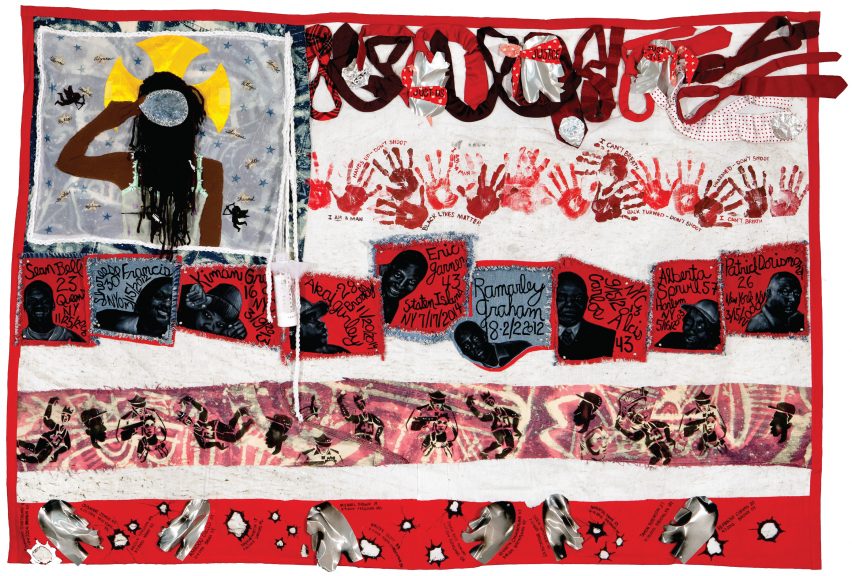
Included in this section are tapestries by Mexican artist Teresa Margolles that commemorate the lives of individuals including Eric Garner and Jadeth Rosano López.
Garner was an African-American man killed in 2014 by NYPD police officer Daniel Pantaleo, who put Garner into a chokehold during arrest. López was a seventeen-year old-girl assassinated in Panama City.
Margolles used fabric that had been placed in contact with the victims’ deceased bodies and collaborated with embroiderers from their respective local communities to create the tapestries.
The Wound and Repair sections includes work from American artist and activist Harmony Hammond’s Bandaged Grid series, in which layered fabric is used to evoke imagery reminiscent of an injured body.
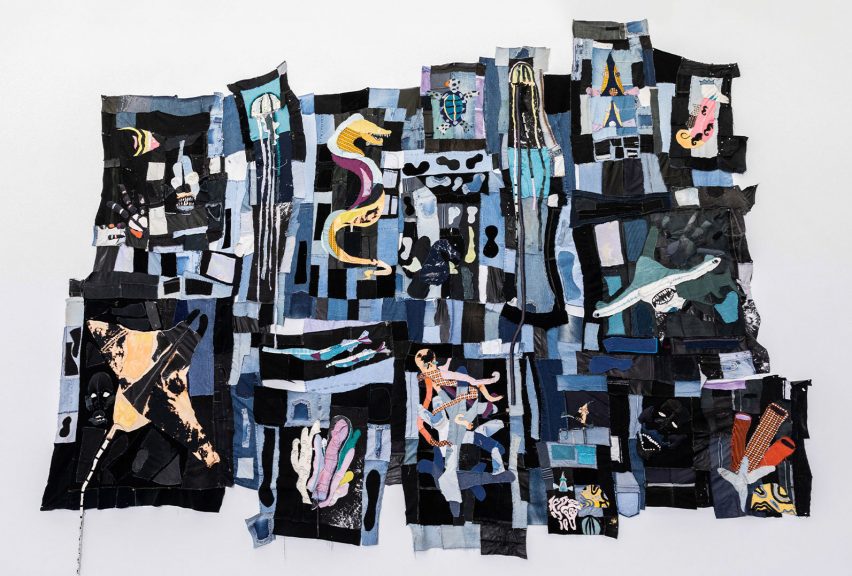
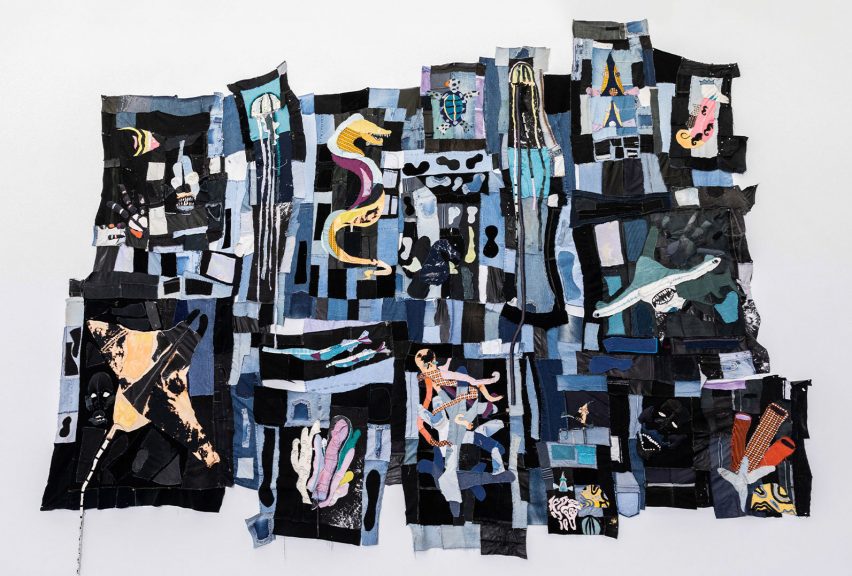
While violence and brutality are key themes examined in the exhibition, it also showcases how textiles can be used to create narratives of hope. The final, most expansive section of the exhibition is titled Ancestral Threads, which encompasses works created to inspire a sense of optimism and reconnect with ancestral practices.
“This section not only explores artists processing exploitative and violent colonial and imperialist histories, but also celebrates the artists who are re-summoning and relearning ancient knowledge systems to imagine a different kind of future,” Johnson explained.
Canadian multimedia artist Tau Lewis’s work titled The Coral Reef Preservation Society is a patchwork assemblage of recycled fabrics and seashells including fragments of textured denim.
The work pays homage to the enslaved women and children thrown overboard in the Middle Passage, the historical transportation route used during the Atlantic slave trade. These women and children have been reimagined as underwater sea creatures to transform the narrative into one of regeneration.
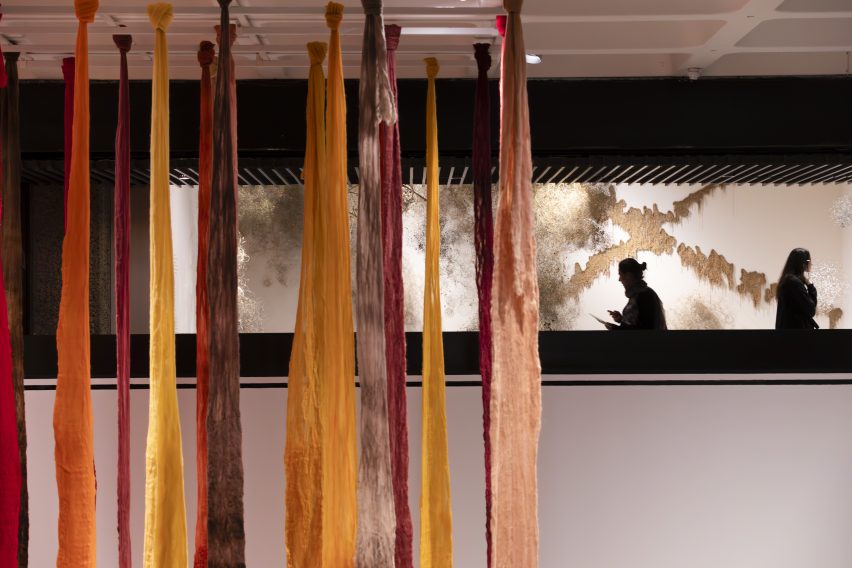
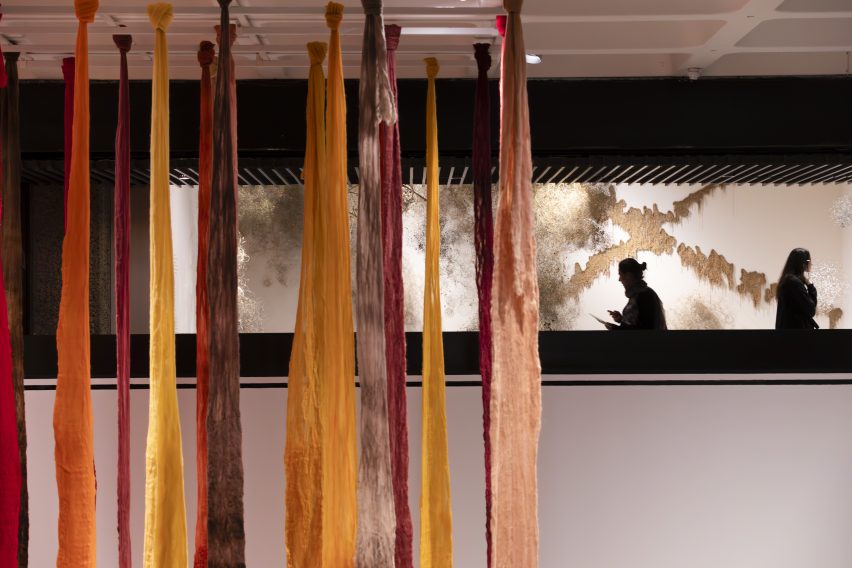
A large installation by Chilean artist Cecilia Vicuña titled Quipu Austral is situated towards the end of the exhibition. The installation takes the form of billowing ribbons hanging from the ceiling.
Vicuña references quipu, a form of recording used by a number cultures in Andean South America. Quipu was a ancient writing system which used knotted textile cords to communicate information.
Other sections in the exhibition include Fabric of Everyday, which explores the daily uses of textiles, as well as Borderlands, which examines how textiles have been used to challenge ideas around belonging.
These sections feature works such as Shelia Hicks’ colourful woven bundles and Margarita Cabrera’s soft sculpture cacti crafted from reclaimed US border patrol uniforms.
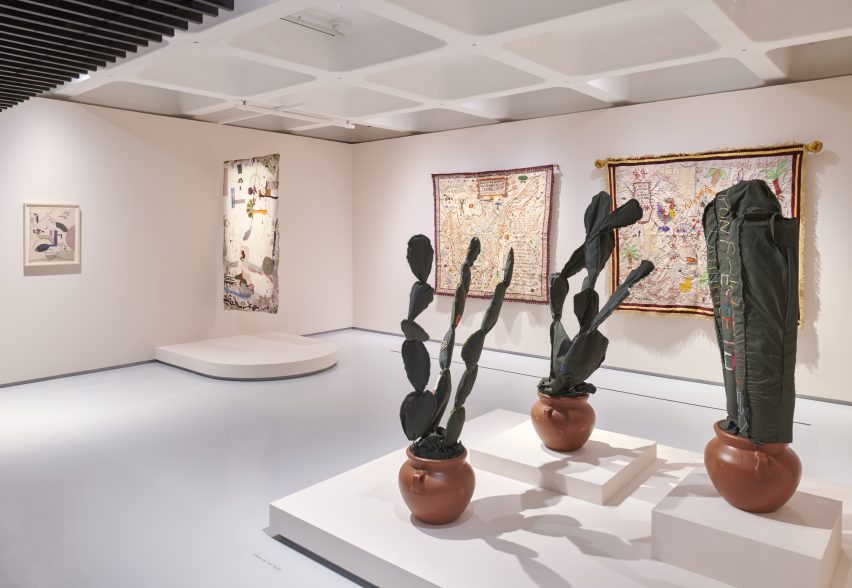
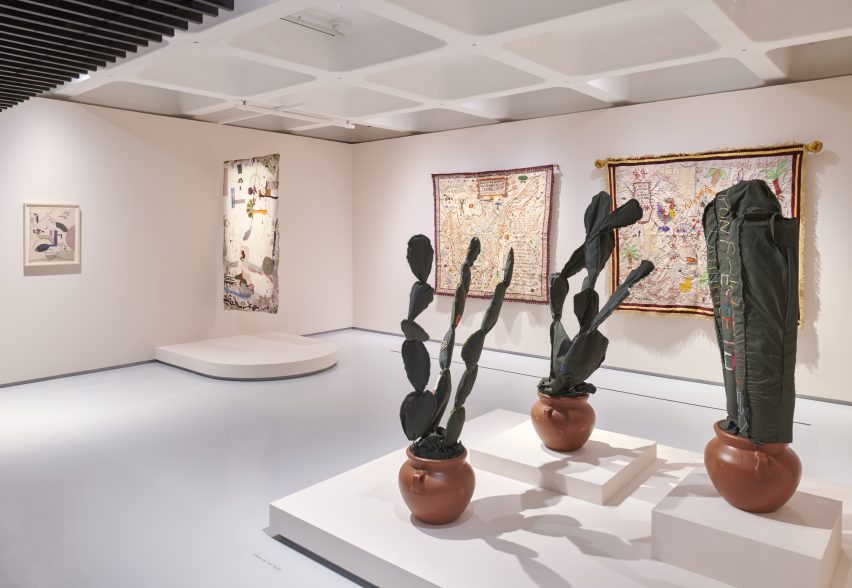
“We hope that people might come out of this exhibition feeling invigorated and moved by the stories of resilience and rebellion embedded in the work but also hope and emancipation,” Johnson said.
“I hope that the show might inspire people to pick up a needle and thread themselves and use it to express their own lived experience.”
The show is a partnership between the Barbican and the Stedelijk Museum in Amsterdam and was co-curated by Barbican curators Johnson, Wells Fray-Smith and Diego Chocano, in collaboration with Amanda Pinatih from the Stedelijk.
Unravel: The Power and Politics of Textiles in Art is at the Barbican Centre until 26 May 2024. See Dezeen Events Guide for an up-to-date list of architecture and design events taking place around the world.
Partnership content
This video was produced by Dezeen for the Barbican Centre as part of a partnership. Find out more about Dezeen’s partnership content here.