Dalston Works by Waugh Thistleton Architects became world’s biggest CLT building
Up next in our Timber Revolution series is a look at the Dalston Works apartment complex in London by Waugh Thistleton Architects, which is the world’s largest cross-laminated timber building.
Completed in 2017, Dalston Works is a 10-storey residential development in east London that contains 121 apartments with balconies as well as two ground-level courtyards, retail and restaurant space and an integrated flexible workspace.
Upon its completion, the project became the world’s largest cross-laminated timber (CLT) building, was its uses more of the material by volume – 3,852 cubic metres – than any other building. Dezeen is not aware of any larger CLT buildings constructed since.
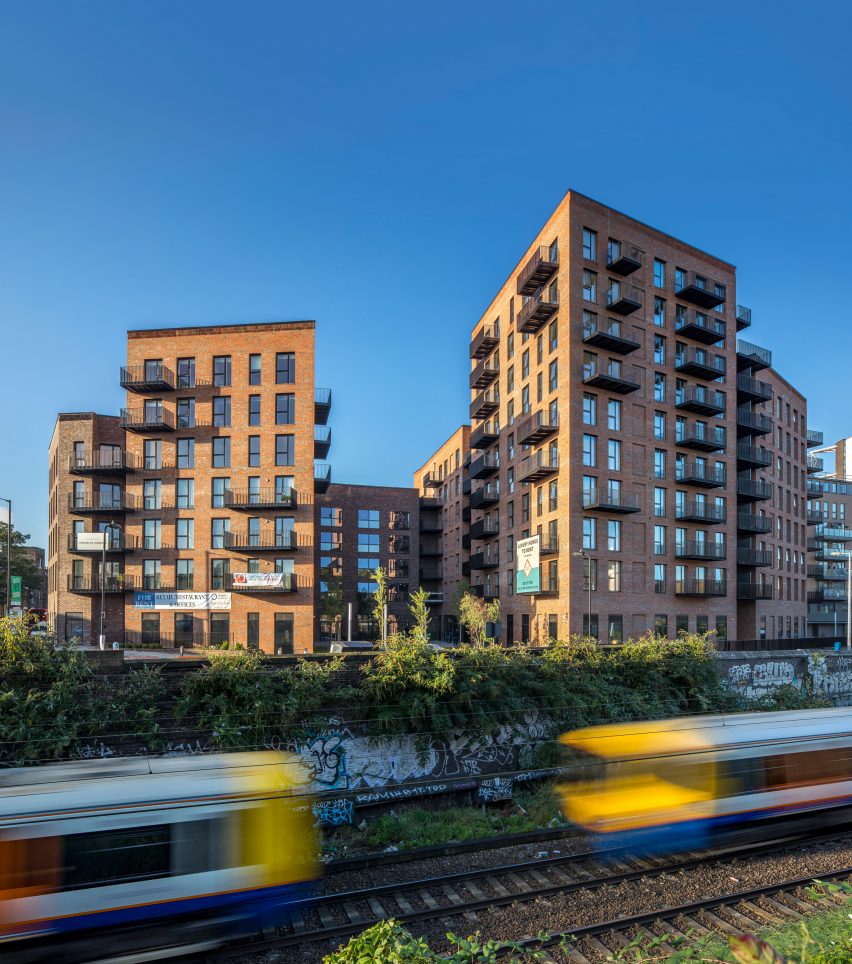
It was designed by local architecture studio Waugh Thistleton Architects – a Shoreditch-based timber specialist that has been predominantly working with engineered wood since 2003.
Waugh Thistleton Architects also designed Murray Grove, which was previously profiled as part of Dezeen’s Timber Revolution series.
CLT is a panel material made by gluing at least three layers of wood at right angles to each other, which is significantly less carbon-intensive than other structural materials such as concrete or steel.
The panels are characterised by structural rigidity in two directions thanks to the arrangement of the layers and are cut to size before being assembled on-site.
Dalston Works has external, party and core walls as well as flooring and stairs made entirely from pieces of CLT that were delivered to the formerly neglected brownfield site over 374 days.
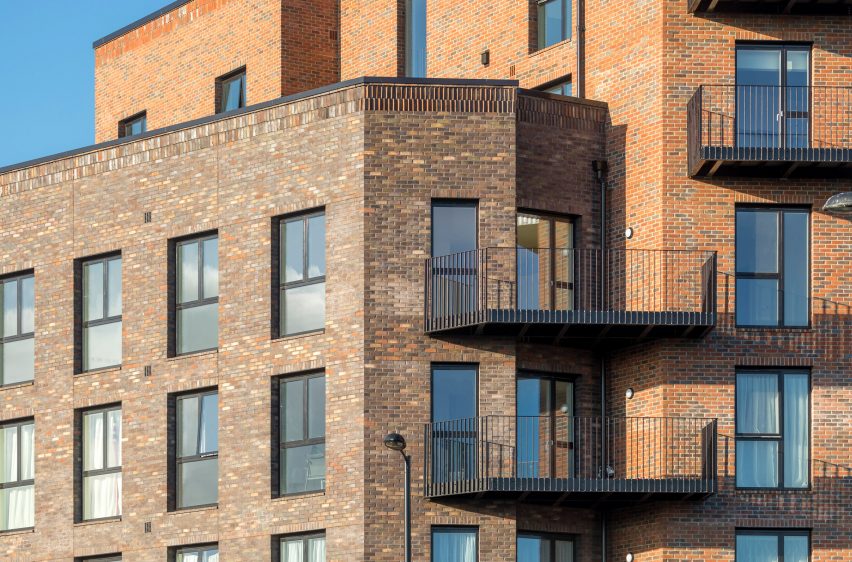
“[CLT] is replenishable, beautiful, healthy, fast and economic,” Andrew Waugh told Dezeen, who co-founded the architecture studio with Anthony Thistleton in 1997.
“Timber is easy to cut and to build with, so the buildings are easy to adapt – so they last longer,” he added.
“This also makes the material easier to use as part of a prefabricated system so that we can make higher quality buildings faster and with better working conditions for those involved.”
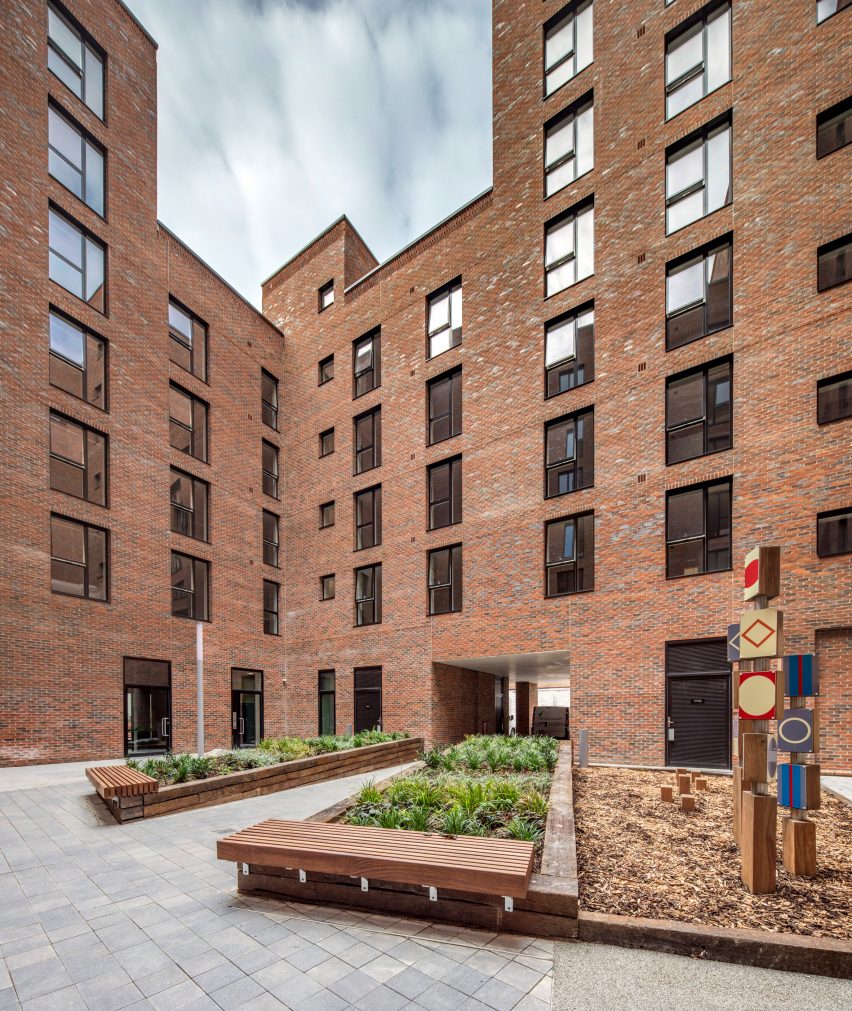
The development is separated into several boxy volumes, while the CLT frame was clad in traditional bricks chosen to reference the Edwardian and Victorian architecture of nearby warehouses and terraced properties.
“[The brickwork] was important to the client and to the planners,” reflected Waugh. “I am happy with the way it looks but would have preferred a lightweight cladding material.”
“We needed to greatly increase the amount of timber in the structure just to hold the bricks up in the air,” Waugh explained.
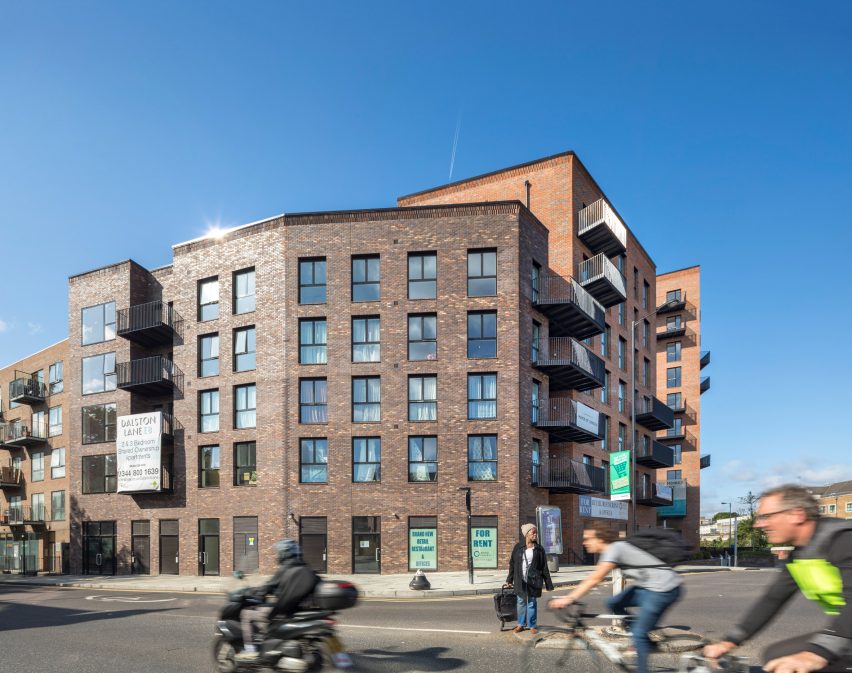
Despite this, Dalston Works weighs a fifth of a concrete building of its size, according to the studio, which reduced the number of deliveries required during construction by 80 per cent.
Creating a lighter core meant that the project could reach much higher than if it had been constructed in concrete, since the development sits above the underground Elizabeth Line railway.
The project’s CLT frame also has 50 per cent less embodied carbon than a traditional concrete one. This refers to the amount of energy required to produce and form a material or object.
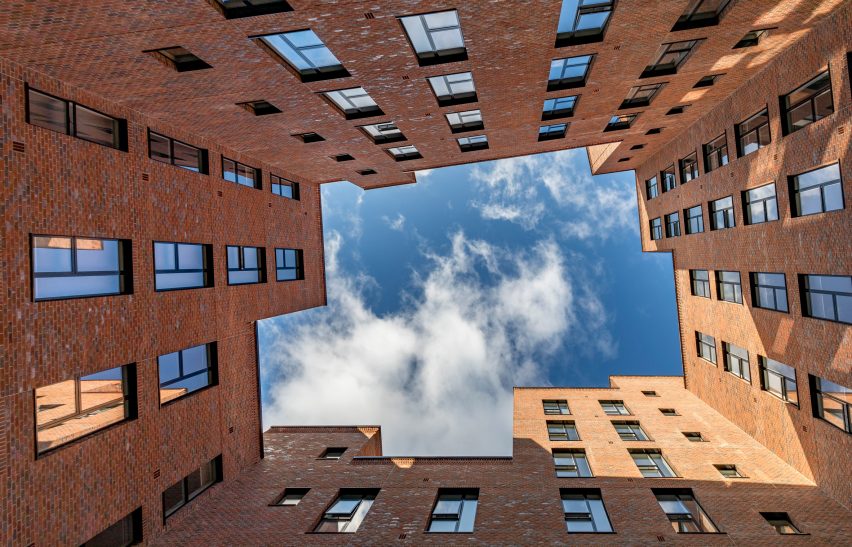
“There wasn’t a great deal of client motivation or legislative demand for any measures beyond meeting BREEAM and building regulations,” Waugh recalled, referring to standards that limit operational emissions as opposed to embodied emissions.
“My own view is that building regulations are pretty effective – and if you have an efficient, airtight building which is passively designed to suit its location then the operational carbon demand will be pretty low, and you have to assume that we will generate it from renewable energy in the near future.”
“Lots of stuff and complex gear designed to very slightly reduce the energy demand is a bit of a waste of resources. The real issue here is reducing the use of concrete and steel – the carbon savings from doing that are immense.”
According to project engineer Ramboll, more than 2,600 tonnes of carbon dioxide is stored within Dalston Works’ CLT frame.
Nearly six years on from Dalston Works’ completion, Waugh reflected on the significance of the world’s largest CLT building.
“At the time it was an important milestone – to demonstrate that timber is a viable alternative to concrete and steel – and at scale,” reflected the architect. “But I think it’s dangerous to measure a building’s success by its size,” he warned.
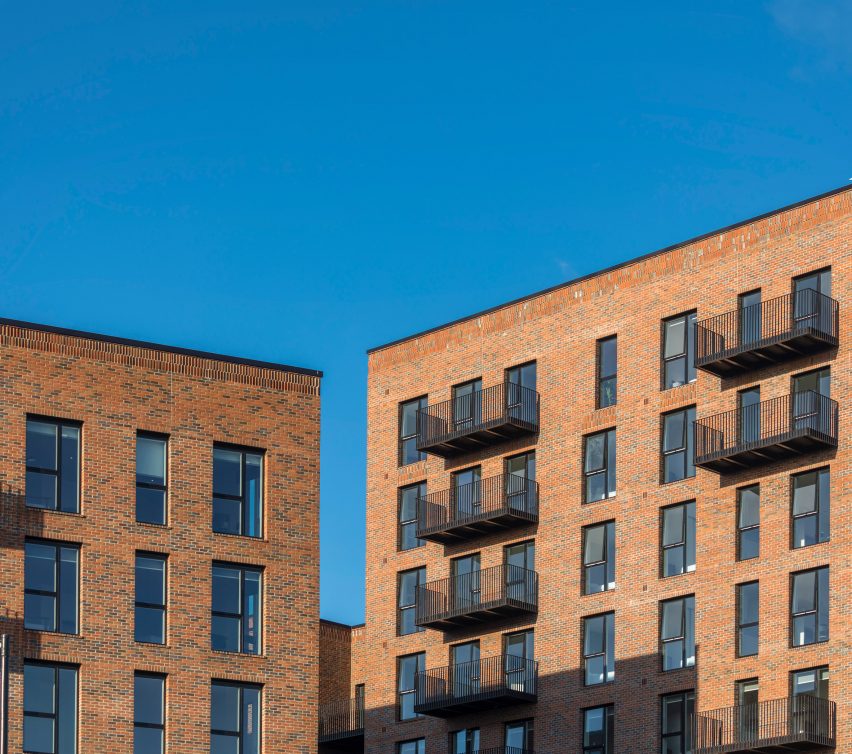
Known as a long-time campaigner for the use of mass timber in architecture, Waugh said that he recently wrote a “big piece” to the UK government calling for it to invest more in sustainable architecture practices, explaining that the UK has been “left way behind” compared with various mass-timber projects being created in other parts of the world.
“The UK is behind in terms of timber because we have a government that does not prioritise carbon reduction – and is heavily influenced by lobbying from both construction companies and the manufacturing industry,” said the architect.
“Architects need to start driving demand – seeking out opportunities to design in timber and build a market. Designers need to prioritise carbon reduction in their work and start reconsidering how they think about success in the buildings they design.”
The photography is courtesy of Waugh Thistleton Architects.

Timber Revolution
This article is part of Dezeen’s Timber Revolution series, which explores the potential of mass timber and asks whether going back to wood as our primary construction material can lead the world to a more sustainable future.