“Timber is being abused” says architect Hermann Kaufmann
Sloppiness and misinformation are threatening to prevent large-scale wood construction from reaching its full potential, argues Hermann Kaufmann – the “grandfather of mass timber” – in this interview as part of our Timber Revolution series.
“Now is a really dangerous time for wood as a resource,” the Austrian architect told Dezeen. “You can say it’s the saviour of the construction industry. And I believe it has a part to play, where it makes sense to use it.”
“But it’s also a limited resource so you have to be careful not to overuse it, especially now that other industries are jumping on the bandwagon,” he continued. “Timber is being kind of abused.”
Mass timber could “shoot itself in the foot”
Since buildings offer long-term storage for the carbon locked away in wood, Kaufmann argues that the construction industry should have first dibs on the world’s limited timber supplies.
But currently, the industry is being held back by a lack of skilled craftsmen and technical knowledge, which he warns could have a detrimental effect on building quality.

“Building with wood requires diligence but diligence is disappearing,” Kaufmann said. “If you compare the building culture across Europe, there are huge differences in the execution quality when looking at a building in Switzerland or in, say, France or England.”
“If you do a sloppy job when you’re building with wood, and you get condensation or water ingress that you don’t notice right away, the material will rot quickly and you can get huge structural damages,” he added.
“So I’m a bit scared that there will be some cases of damage in the future, and mass timber could shoot itself in the foot.”
Building in mass timber for more than 30 years
Although perhaps less well-known outside of the German-speaking world, Kaufmann is considered a pioneer of modern timber construction, dubbed the “grandfather of mass timber” by Canadian architect Michael Green.
Born to a long line of carpenters, Kaufmann dedicated himself to the “forgotten topic” of wood construction as early as the 1970s, when he was studying architecture at the technical universities of Innsbruck and Vienna.
“At the time, there was beginning to be some modern timber construction in the Alpine region,” he said. “But internationally, there was almost nothing. Even in Japan, the good architects that are now working in wood didn’t do much back then.”
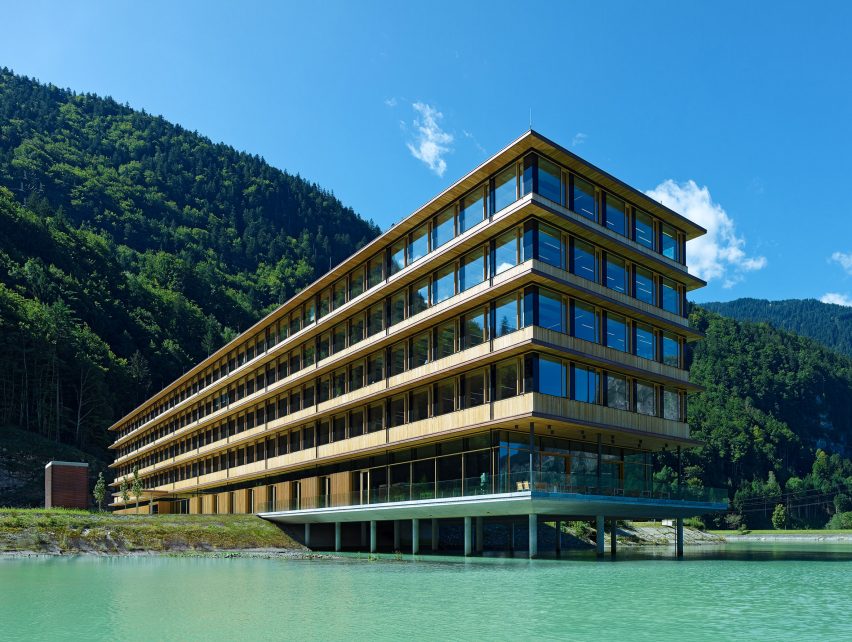
“I questioned whether I was on the right path when my fellow students were getting bigger and bigger projects and I was still working on relatively small things,” he added. “Back then, there were no really big projects in timber.”
“You had to go to a welder and get them to make you custom screws and steel parts so that you could build modern wood structures.”
Kaufmann started his own practice, Hermann Kaufmann + Partners, in 1983 and later founded one of Europe’s first dedicated institutes for timber construction at the Technical University of Munich, with the aim of reviving wood as a modern construction material.
Among his seminal projects is a Passivhaus apartment block that made use of prefabricated mass-timber modules back in 1997, a timber-skeleton secondary school that won the German Architecture Prize in 2017 and an office building perched over an artificial hydropower lake, which at one point was the largest building of its kind in Europe.
Kaufmann’s expertise in tall wood structures was also crucial in the construction of Brock Commons – a student residence at the University of British Columbia that was the tallest mass-timber building in the world upon its completion in 2016.
But even in places like Canada and Scandinavia, which currently have a number of other record-breaking mass-timber projects in the works, the architect says that there is still a considerable skills gap that needs to be addressed.
“Timber architects live off good craftsmen,” he said. “And in countries where you don’t have that, it’s difficult.”
“We advised on the construction of a high-rise in Canada with 18 storeys, which was the tallest at the time, and we were happy we found any craftsmen that knew what they were doing,” Kaufmann continued.
“And whenever I visit the nordic countries like Sweden and Finland, my colleagues complain that they don’t have any more craftsmen, just big manufacturers that end up screwing their buildings together.”
“It will be an evolution, not a revolution”
Kaufmann predicts that timber could only become the main building material in “very few countries” such as his native Austria, where timber is an abundant local resource and where manufacturers and craftsmen can build up the necessary skills to work with the material at scale.
“Many architects are changing course and discovering timber but the industry can’t keep up,” he said. “We need to have apprenticeships to train young people up and we need to build know-how amongst engineers.”
“This whole chain needs the right knowledge to get moving,” Kaufmann added. “This is happening at the moment and it could happen relatively quickly. But it won’t explode. It will be an evolution, not a revolution.”
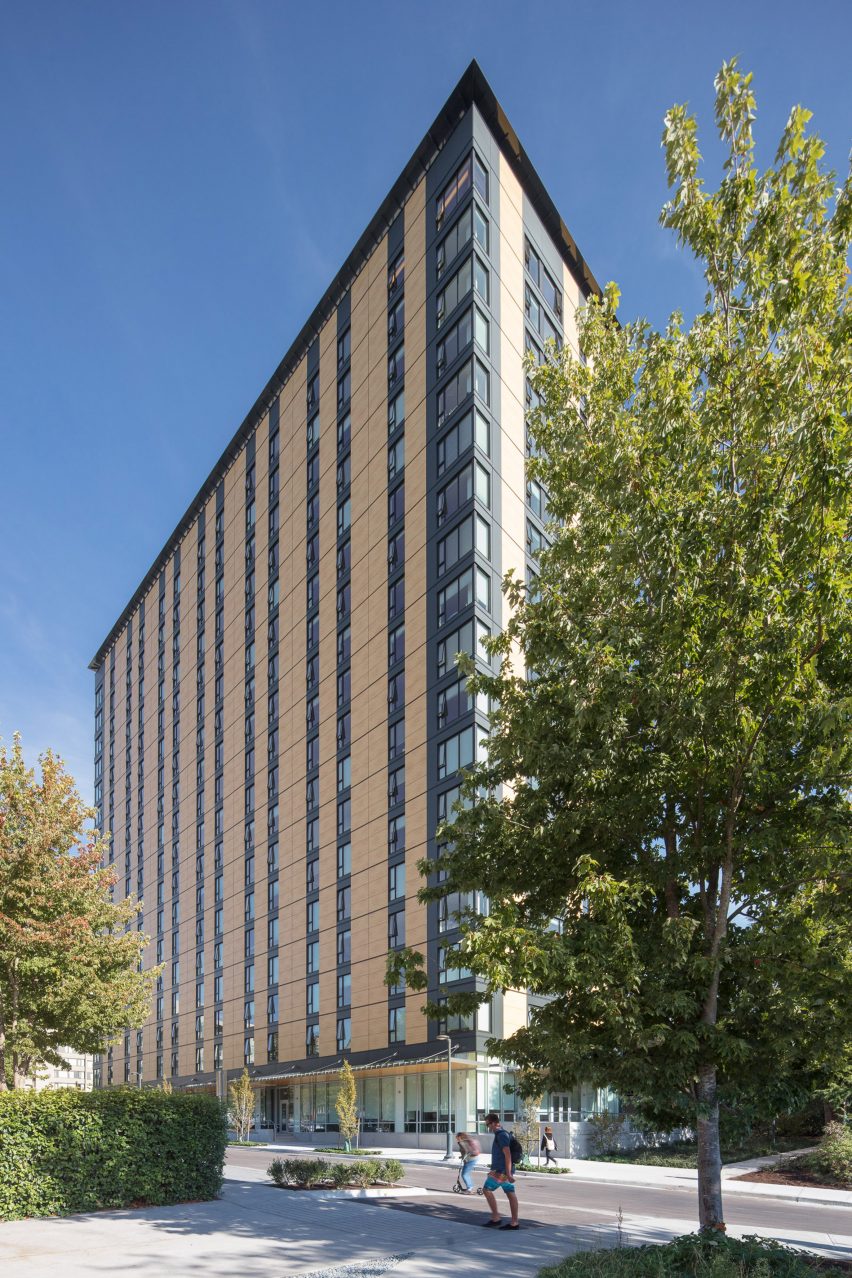
At the same time, he warns that a growing number of architects are already “playing fast and loose” with the term mass-timber and using it to greenwash their buildings.
“People will screw a couple of square metres of wood onto their facade and say the building is sustainable,” Kaufmann explained, comparing the process to adding a decorative spoiler to a vehicle to make it look like a racing car.
“It’s become a bit of an epidemic,” he added. “I will only speak of a sustainable building if the majority of its mass is made up of wood. Everything else is greenwashing.”
Architects can find opportunity in challenge
While the increased complexity and precision required for timber construction poses a challenge for the industry, Kaufmann says it also presents an opportunity for architects to once again become more involved in the process of building their projects, rather than just designing them.
“When you’re building with wood, you have to bring construction know-how into the process way earlier if you want the project to be successful,” he said. “This change in the planning culture is extremely exciting for us because it’s asking way more of the architect.”
“It’s much more interesting, and the competencies of the architect will likely have to go much deeper into the building process again, rather than just acting as a surface or colour designer and making renderings for anyone to build.”
This interview was conducted in German and has been translated into English by the author.
The photography is by Lisa Dünser unless otherwise stated.

Timber Revolution
This article is part of Dezeen’s Timber Revolution series, which explores the potential of mass timber and asks whether going back to wood as our primary construction material can lead the world to a more sustainable future.