Toothbrush pops open for recycling in Seymourpowell’s Un-Made concept
British design studio Seymourpowell has put cheap electronic goods under the spotlight with Un-Made, a project imagining four possible ways to design for quick disassembly and recycling.
As part of the project, Seymourpowell devised four automated disassembly mechanism concepts using an electric toothbrush as an example for their animated graphics.
Each of the mechanisms could be built into a product during manufacturing and then activated in a factory at the end of the item’s life.
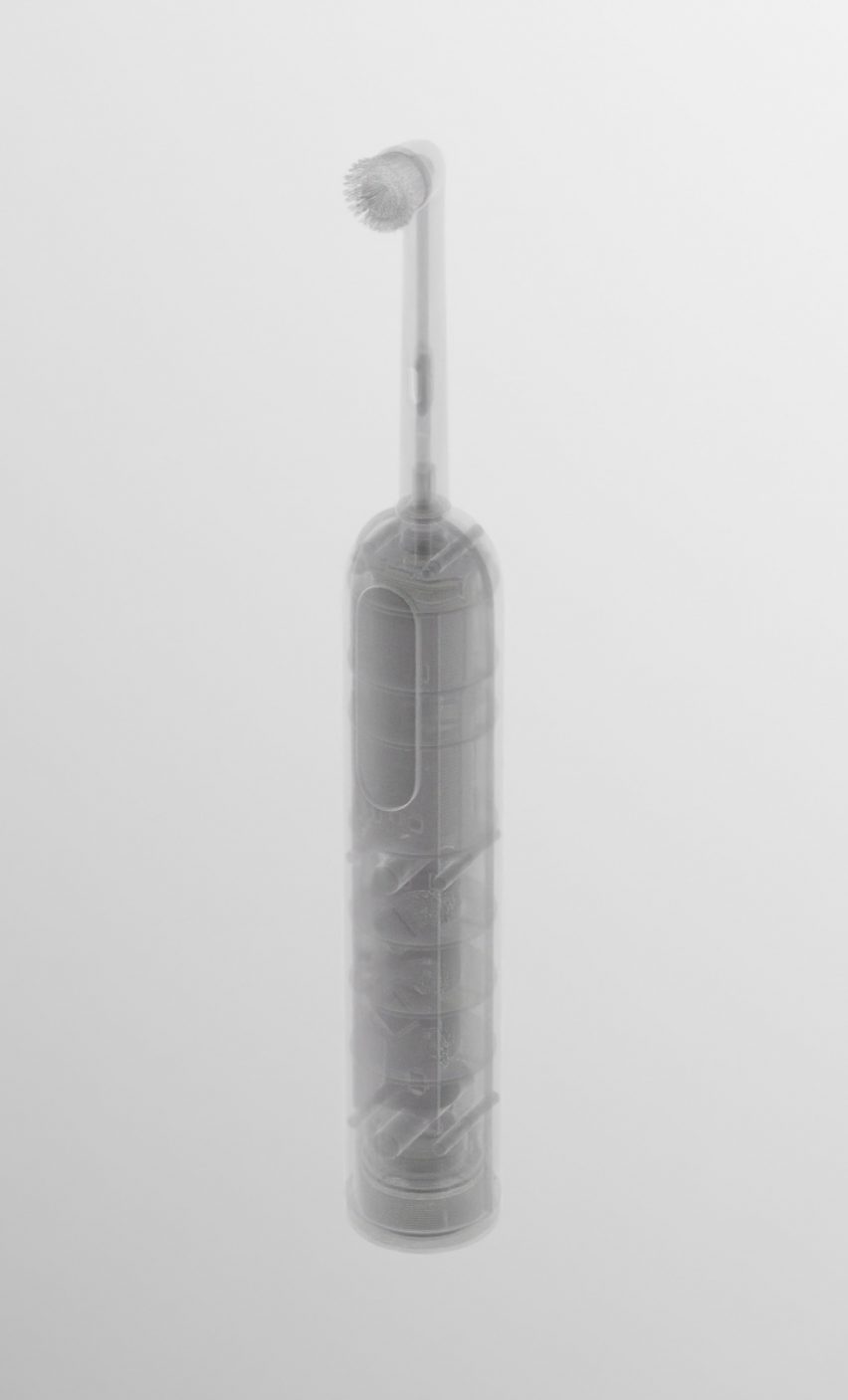
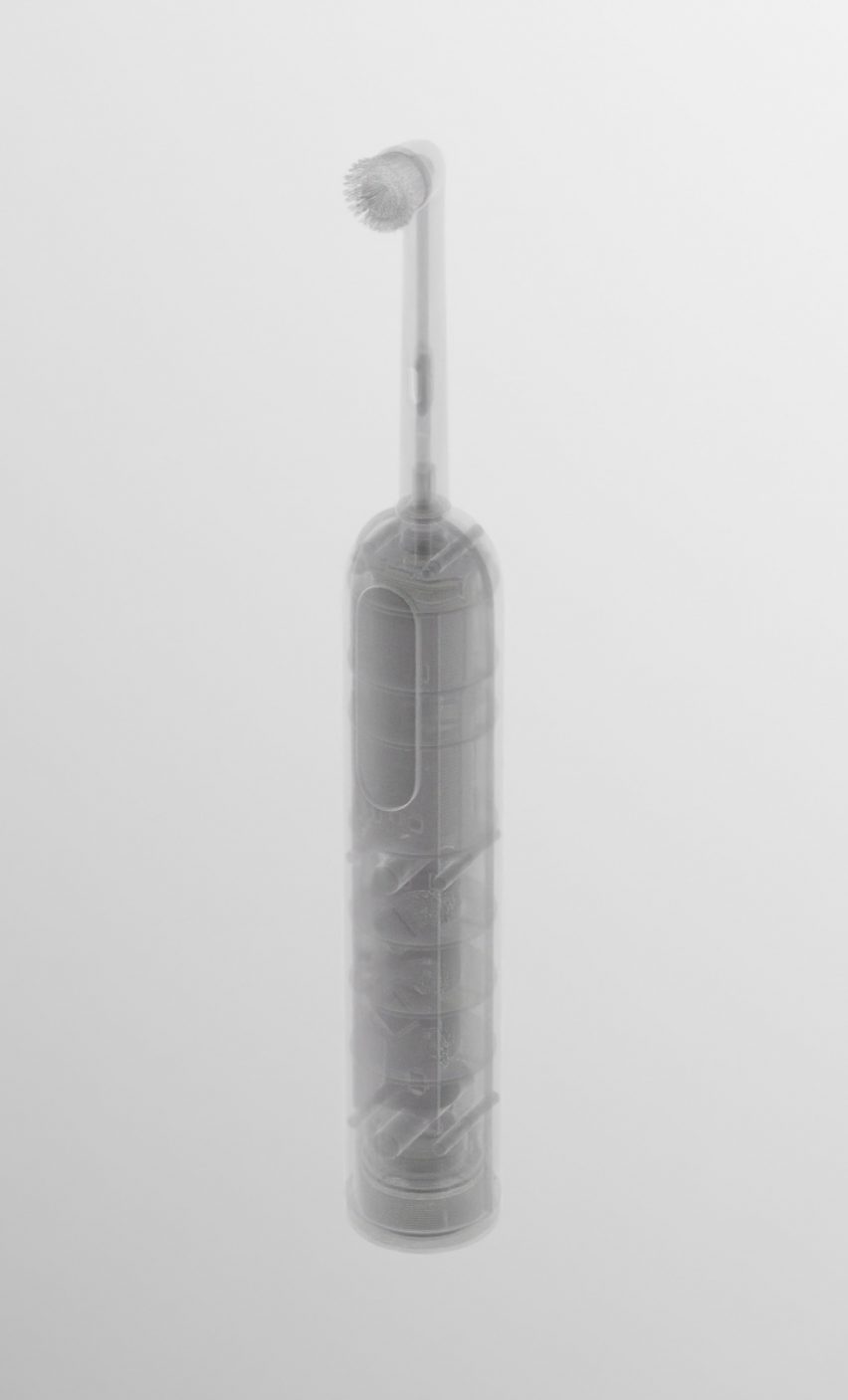
The first Un-Made concept is a pin mechanism. Similar to the action of opening a SIM card slot on a smartphone, it involves poking a pin into a small, sealed pinhole on the rear of the product to release the internal components.
The second concept is a vacuum mechanism. It involves placing the product into a vacuum, causing closed cell foams and air-sealed features within it to expand and bust the external housing open.
Third, there is a piston mechanism that works by pushing a piston through a cap on the bottom of a device and forcing all of the internal components upwards until they emerge through the top.
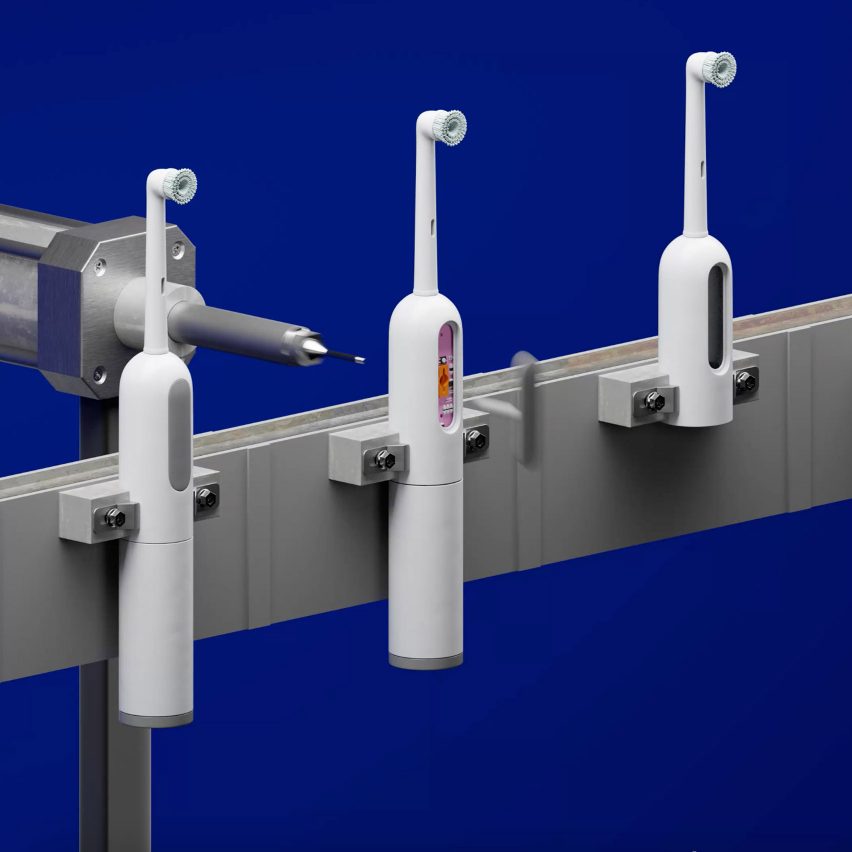
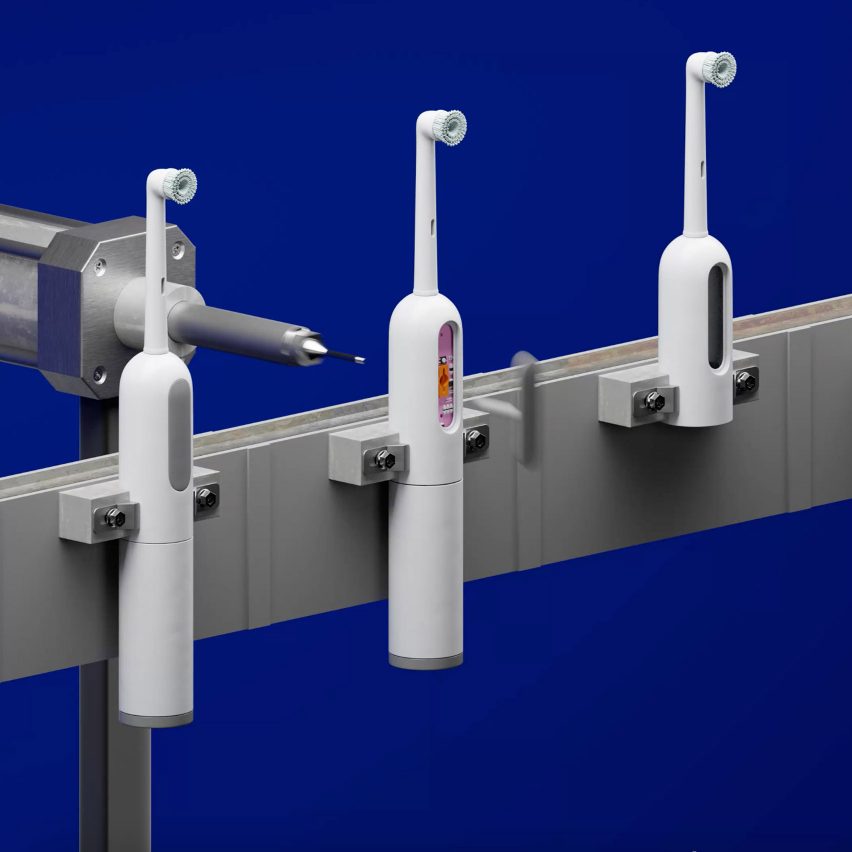
The final concept involves using UV glue – a type of adhesive that deactivates under ultraviolet light. In this concept, the product is placed into a specially lit chamber to release the clamshell construction.
The Un-Made project was led by Eddie Hamilton, a senior industrial designer at Seymourpowell, who was driven to make the work after researching what electric toothbrush to buy for himself.
“Inevitably I went for the cheap one, at which point Amazon smugly pointed out they’d sold 10k+ of that model last month alone,” said Hamilton.
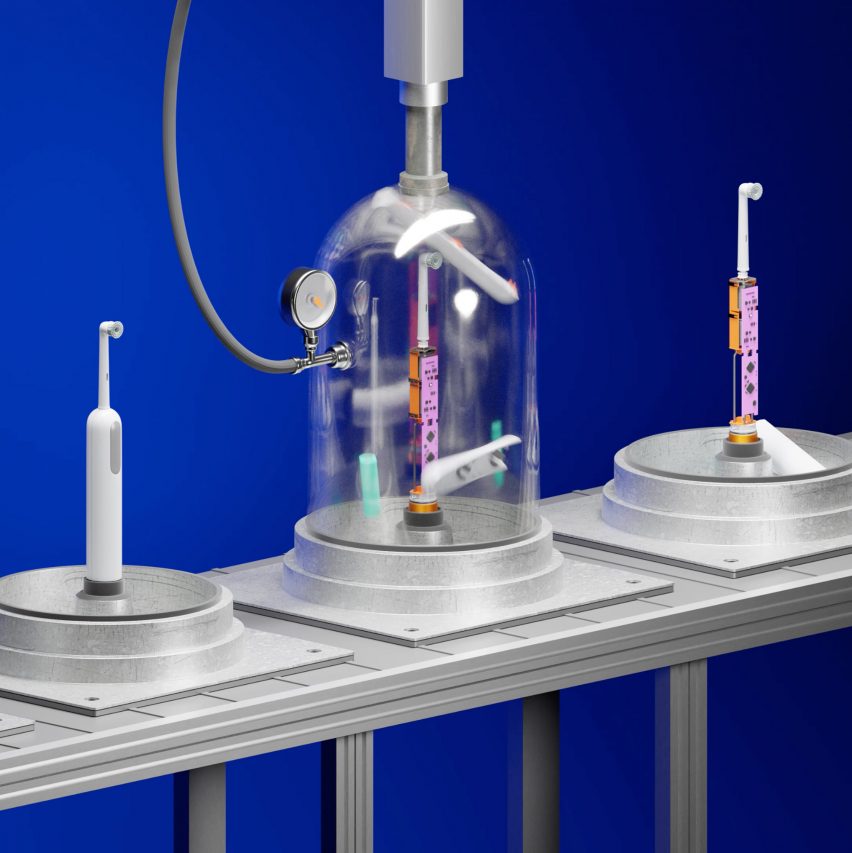
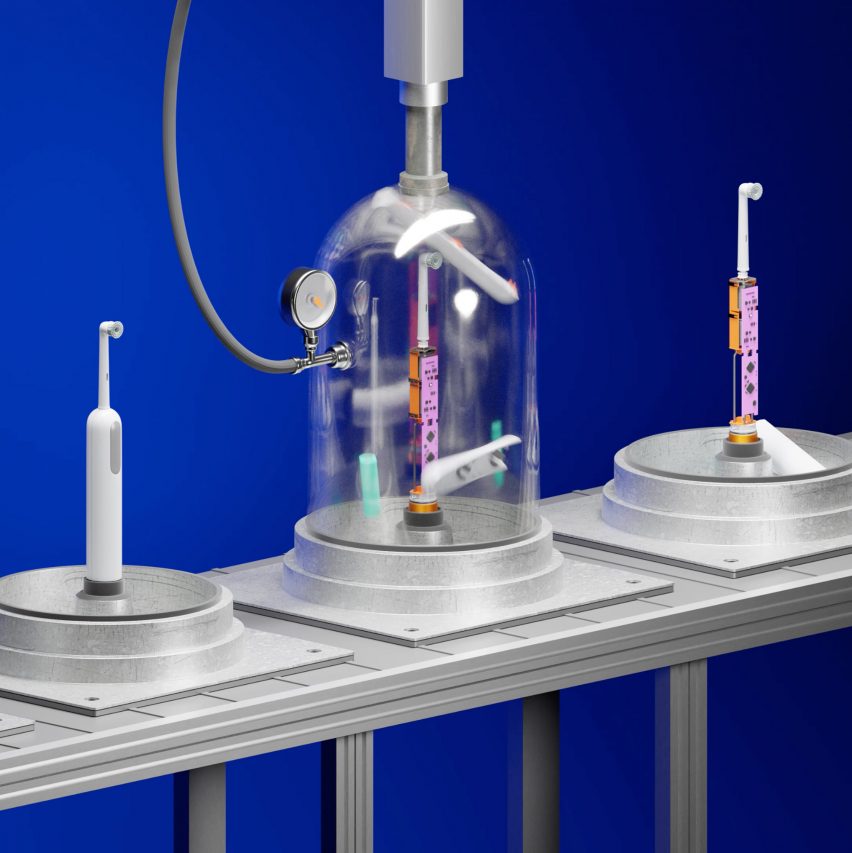
“As an industrial designer, I spend time obsessing over the product I’m working on, typically thinking of it in isolation,” he added.
“But one thing I occasionally fail to remember or adequately picture is the true scale of that product once manufactured. 10,000 units sold per month seems vast.”
Using Amazon’s bestsellers list, Hamilton ascertained that fabric shavers, steam irons, wireless doorbells, wireless computer mice, digital tyre inflators and USB-C adaptors were all items selling in their thousands each month, at a price of less than £20.
While designing products so they can be repaired is important, the associated expense may not be something that customers can justify for small items sold at this price point, Hamilton said.
“Even if we change societal attitudes, the bottom line is whether you should open that cheap toothbrush to replace a failing battery when you only paid £24.99 for it two years ago,” he said.
“I’m optimistic for some product categories to get the ball rolling, namely expensive and bulky items. But I’m also a realist that we need alternative strategies adjacent to repair. This is where we must design for disassembly.”
In Hamilton’s view, disassembly and recycling is a worthy “next best option” to repair for cheaper objects, as it keeps the materials in a circular material flow.
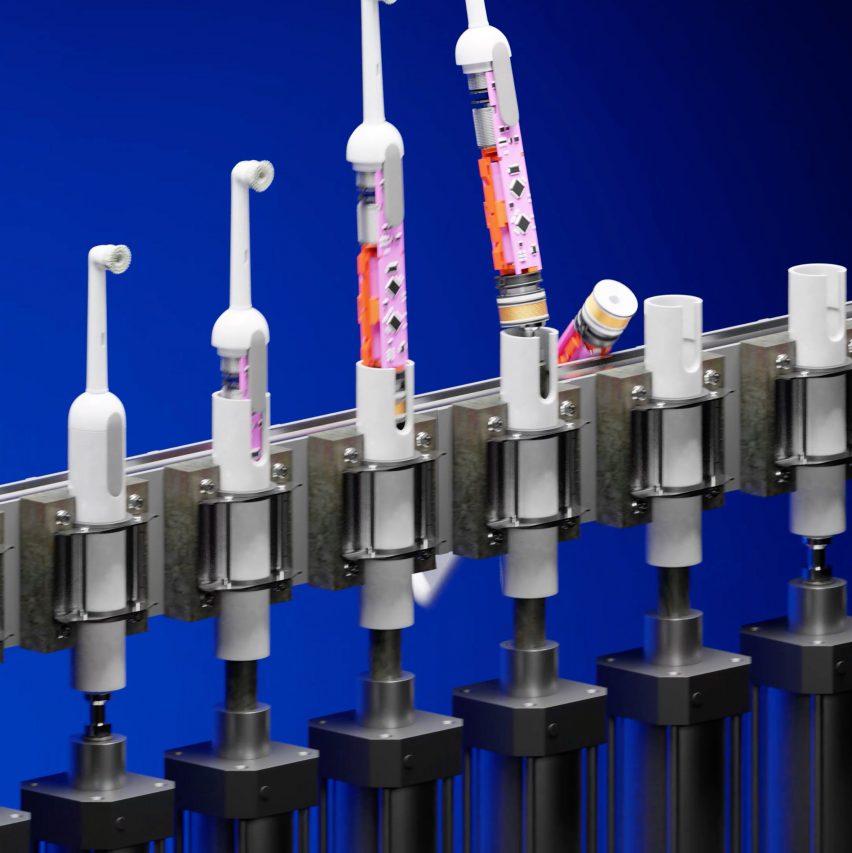
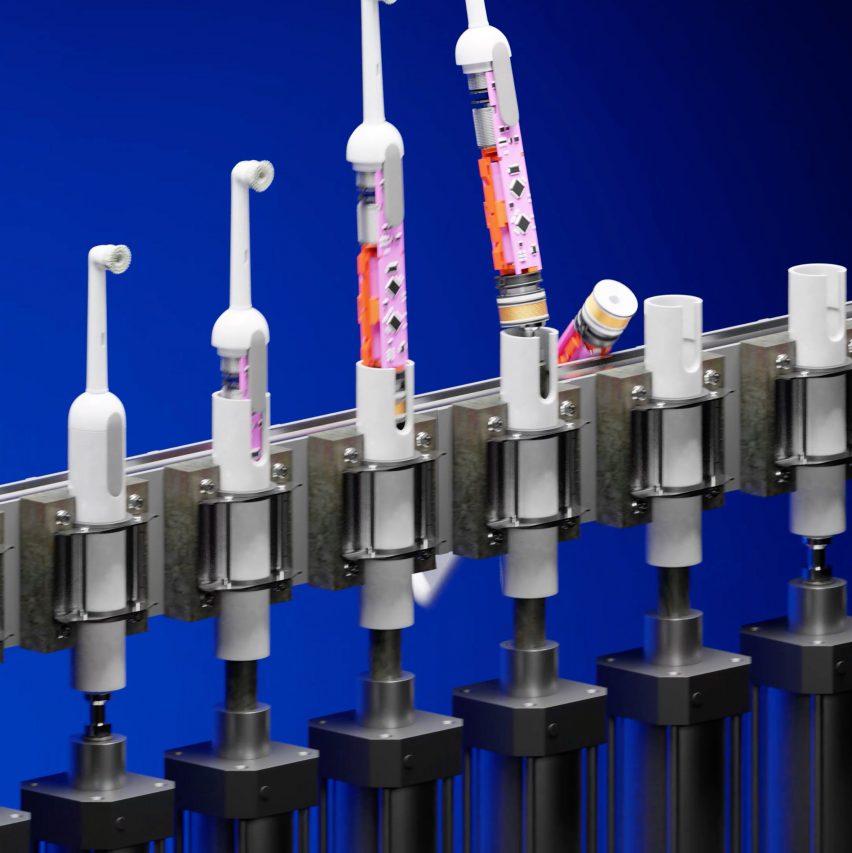
The Un-Made design team took inspiration from Agency of Design’s Design Out Waste project, which looked at three strategies for keeping a toaster out of landfill. But they particularly wanted to explore just how efficient the disassembly process could be made through automation.
The cheaper and easier the process, they say, the more motivation there is for companies to pursue this approach and recover the components and materials inside their devices.
“A huge part of the reason e-waste ends up in landfill is because of product complexity and the inherent challenges involved in their disassembly,” Seymourpowell lead designer Alex Pearce told Dezeen.
“To date, because e-waste has been considered too time-consuming and costly to disassemble – there has been no (commercial) incentive strong enough to make it a viable option.”
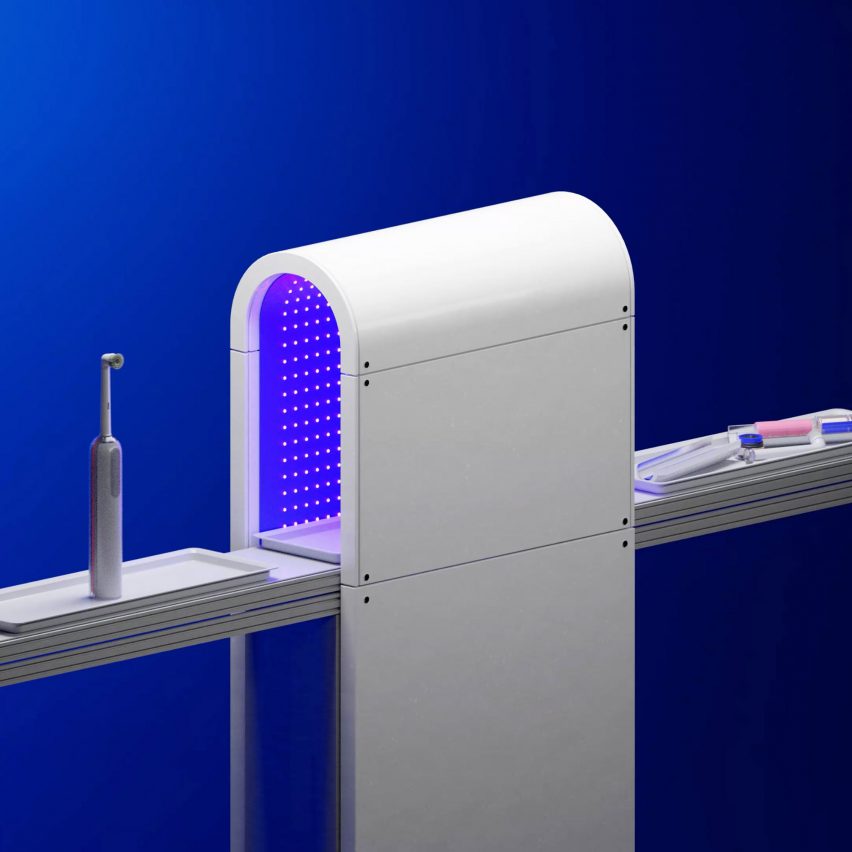
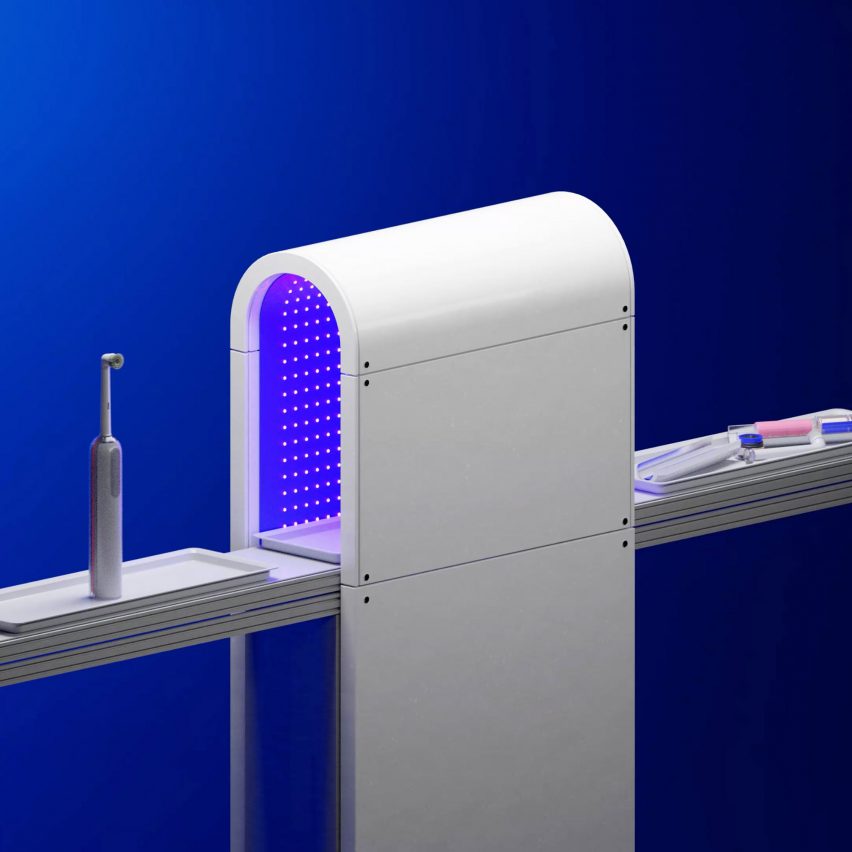
The materials inside even cheap devices are valuable, Pearce points out, particularly when there are supply shortages or when it comes to rare-earth minerals.
“When you consider that more gold exists within a ton of e-waste than within a ton of gold ore dug from the ground, a straightforward economic imperative becomes clear for companies who are able to recover and reuse these materials,” said Pearce.
Seymourpowell imagines disassembly taking place either at the manufacturer’s facilities following a take-back procedure, or potentially at a public recycling centre if disassembly processes have been sufficiently standardised.
The London-based studio is known for its innovative product and transport designs, as well as concepts that challenge current norms. Recent projects from the studio have included the two-in-one reusable Bottlecup and a spaceship cabin for Virgin Galactic.