First full-height timber wind turbine opens in Sweden
The world’s first full-scale timber wind turbine has started turning in Sweden, with a tower built by wood technology company Modvion.
The 105-metre-tall tower, located in the region of Skara, is Modvion‘s first commercial wind turbine tower, and follows on from a smaller 30-metre-high demonstration project the company completed in 2020.
While its rotor blades and generator hub are made of conventional materials, the tower is made of laminated veneer lumber (LVL), a type of engineered wood made of thin veneer strips glued together and often used for beams and load-bearing building structures.
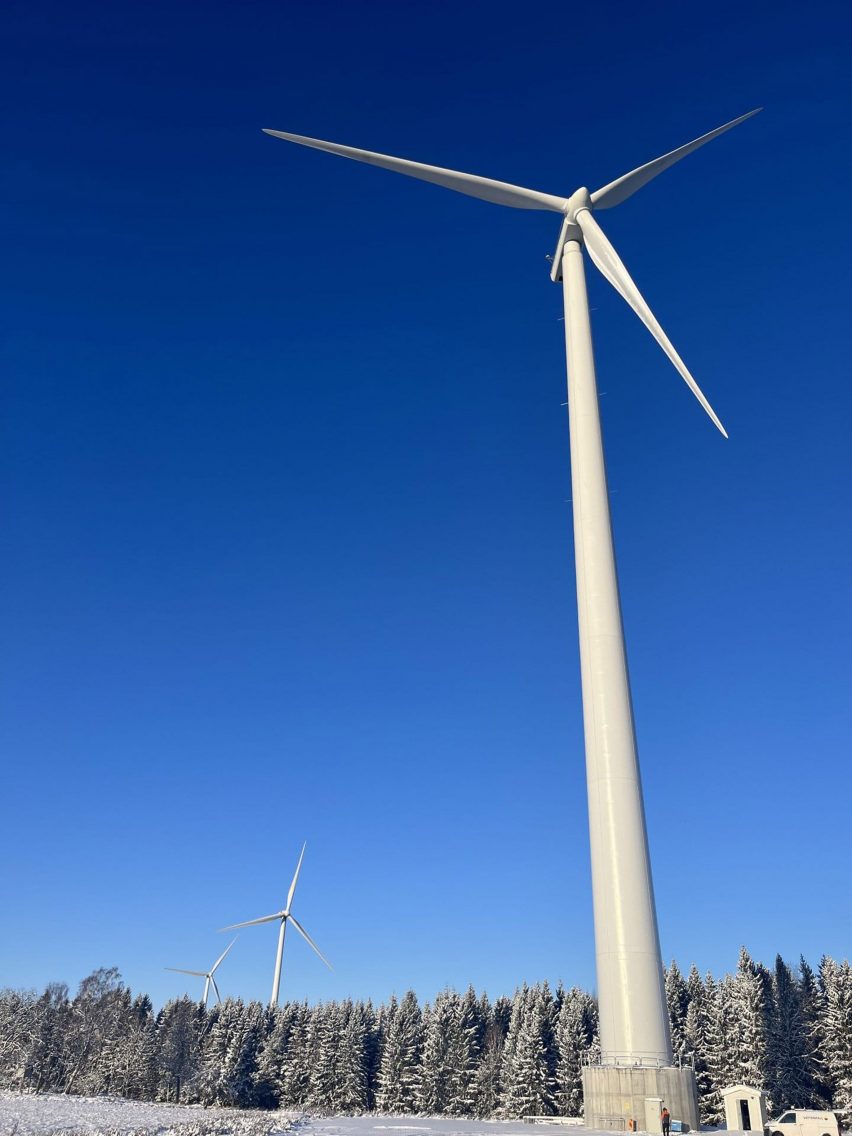
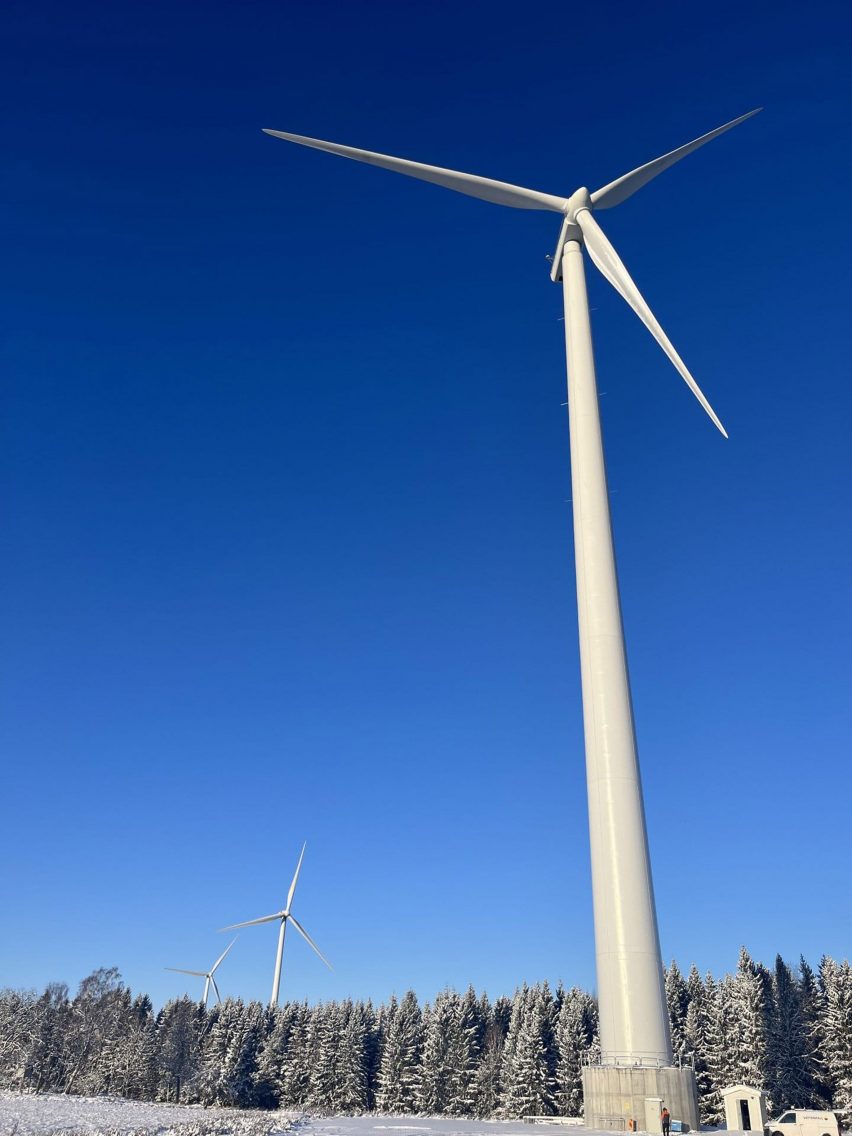
The company says that this type of wood is not only strong enough to withstand the forces of a turning turbine, it is much more environmentally sustainable to build with than the currently used steel.
While wind power plays an important role in providing the world with green renewable energy, there are still ample carbon emissions created during their construction — in part because of the steel towers.
Modvion describes its wood towers as reducing the carbon emissions from wind turbine construction by over 100 per cent, due to the combination of a less emissions-heavy production process and the carbon storage provided by trees.
“Our towers, just in the production of them, they emit 90 per cent less than a steel tower that will do carry the same work,” Modvion chief financial officer Maria-Lina Hedlund told Dezeen. “And then if you add the carbon sequestration, then you actually end up with a minus — so a carbon sink. This is great if we want to reach net zero energy production, and we need to.”
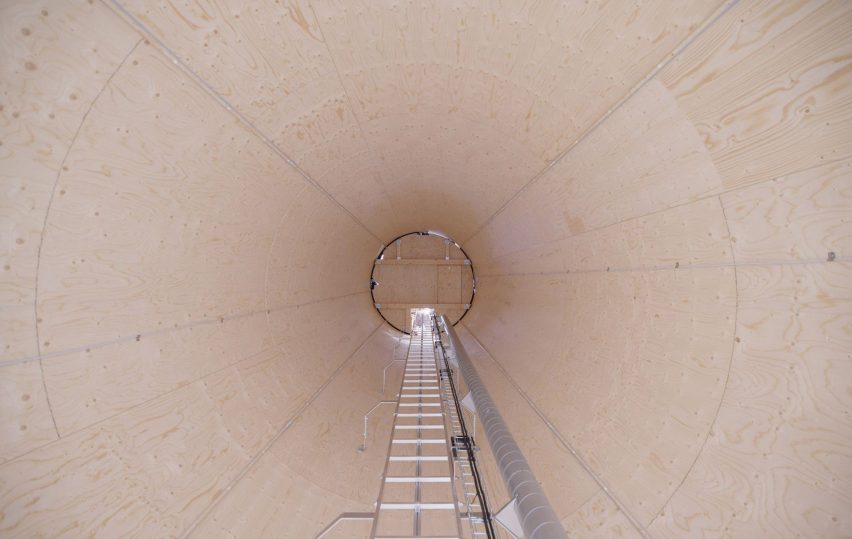
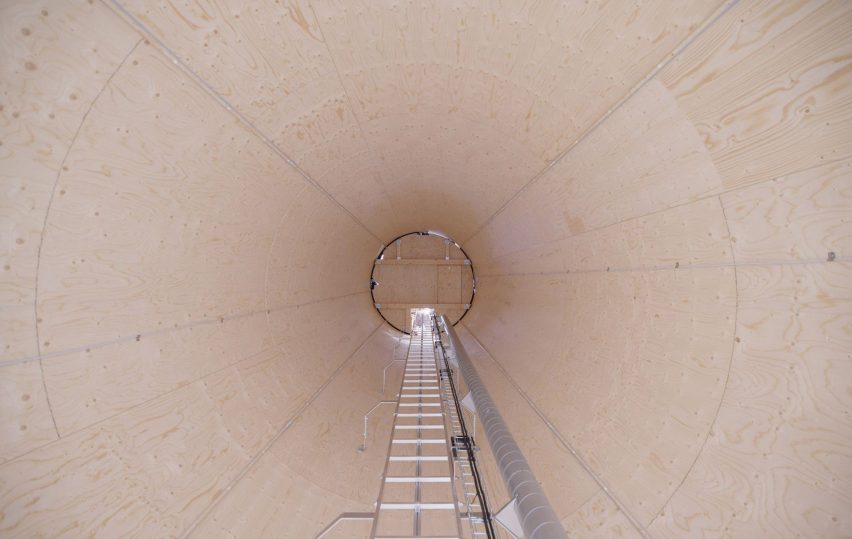
Hedlund, who is also an engineer, describes LVL as having a construction “similar to carbon fibre”, with strips of veneer just three millimetres thick sandwiched and glued together, giving it a high strength-to-weight ratio.
This lightness is a benefit, reducing the amount of material needed overall. With a heavy material, there is a “bad design spiral”, says Hedlund, as the weight of the tower itself adds to the load that it needs to carry.
And while some LVL has all their veneer strips facing in the same direction, Modvion uses its “own recipe” specifying the directions of the fibres, improving the material’s performance even more.
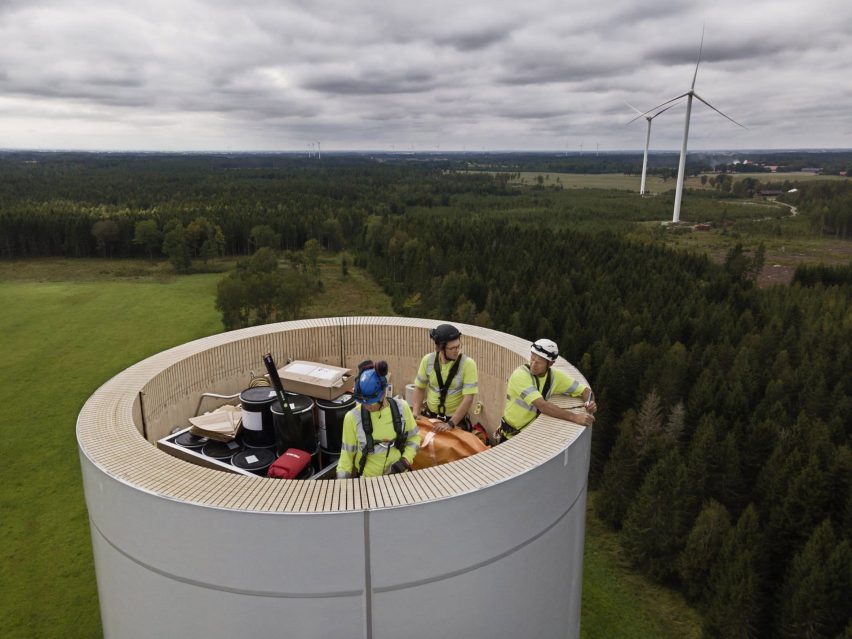
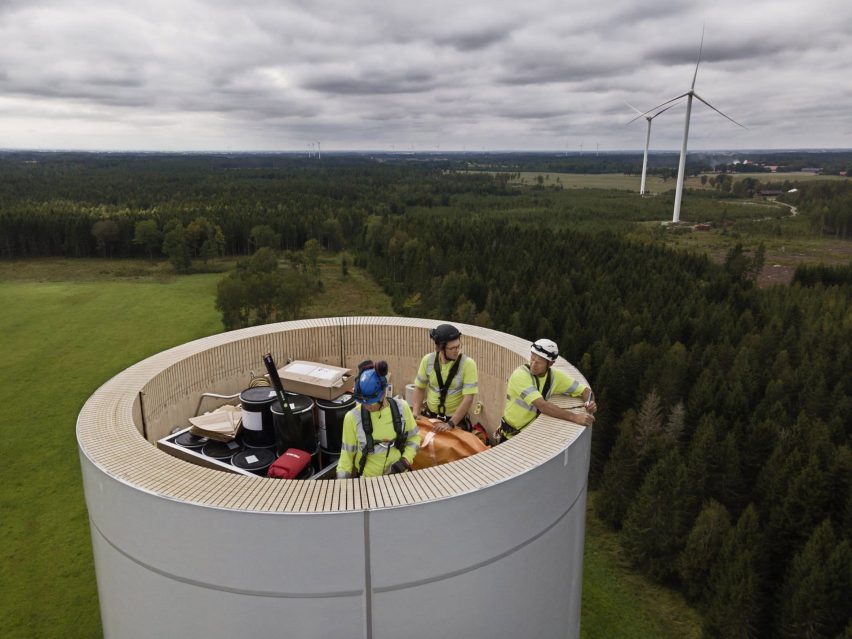
The production process involves timber boards being made to order in a standard LVL plant and then delivered to Modvion’s factory. There, they are glued together into larger modules and bent into a rounded form in a step called lamination, and then very precisely machined to fine-tune the shape.
“In the wood industry, you usually see centimetre tolerances, while we are in the sub-millimetre scale,” said Hedlund.
The modular nature of LVL construction addresses another problem Modvion has observed with steel: that with turbines getting ever bigger to give more power, it’s becoming impossible to transport steel towers to site.
They are built as essentially large cylinders and transported by truck, but the base diameter desired for the tallest towers is getting to be taller than some bridges and roads can allow.
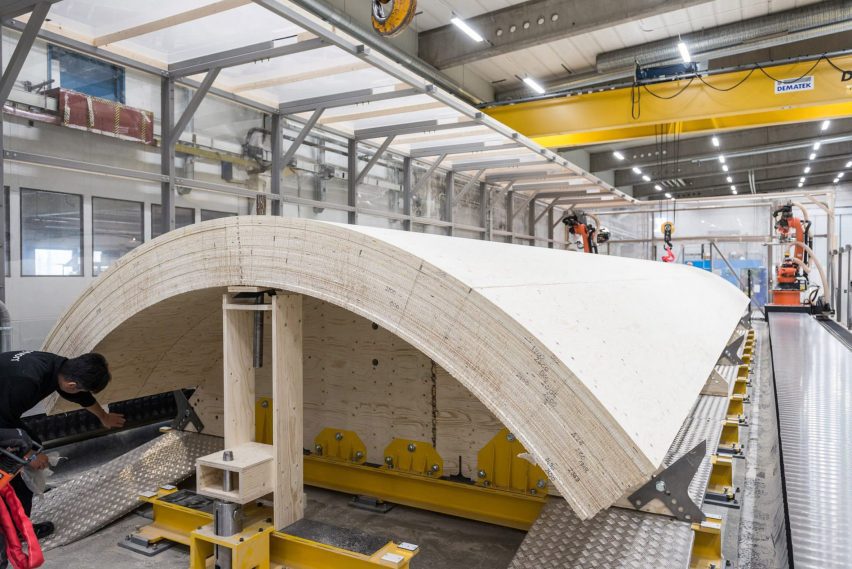
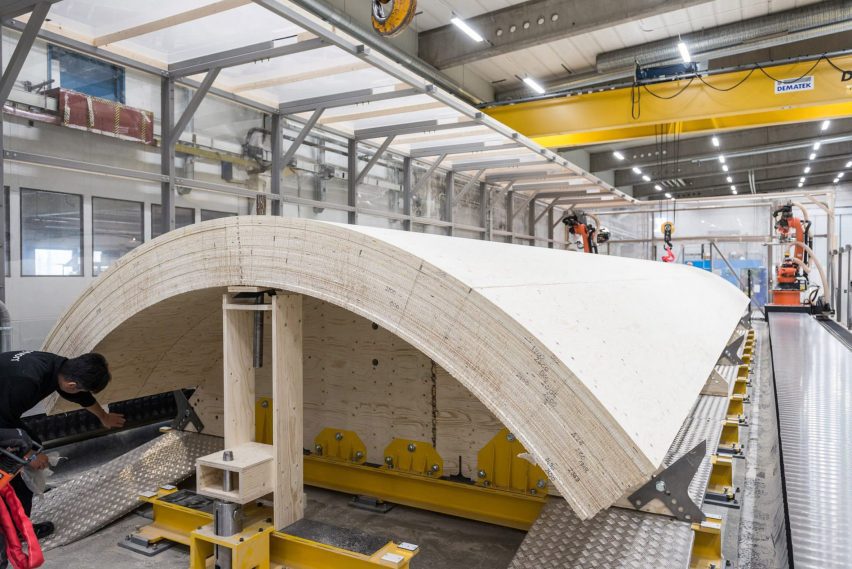
“We’re now reaching a point where they will not get through anymore,” said Hedlund. “So we will see a transition in the wind power industry to modular construction, because this is the way to get them there. And one of the big advantages of building in the material we do is that it’s naturally built modular.”
While steel could also be built modular, it would require bolts rather than glue to join it together on site, which Hedlund says is a disadvantage.
“Bolts are not very nice when you have so much dynamic loading, because it will loosen over time,” she said. “So first of all, you have to have to put them in place which is a lot of work, and then you have to also service them over the lifetime.”
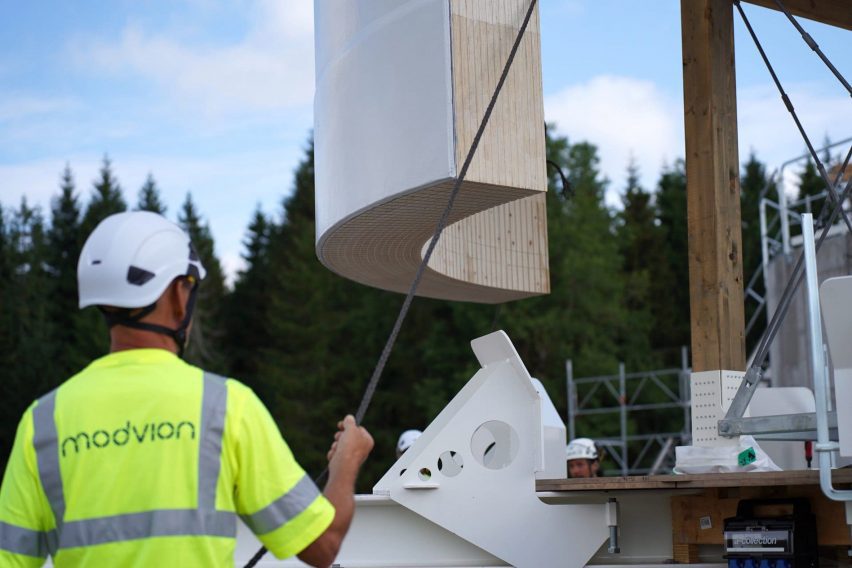
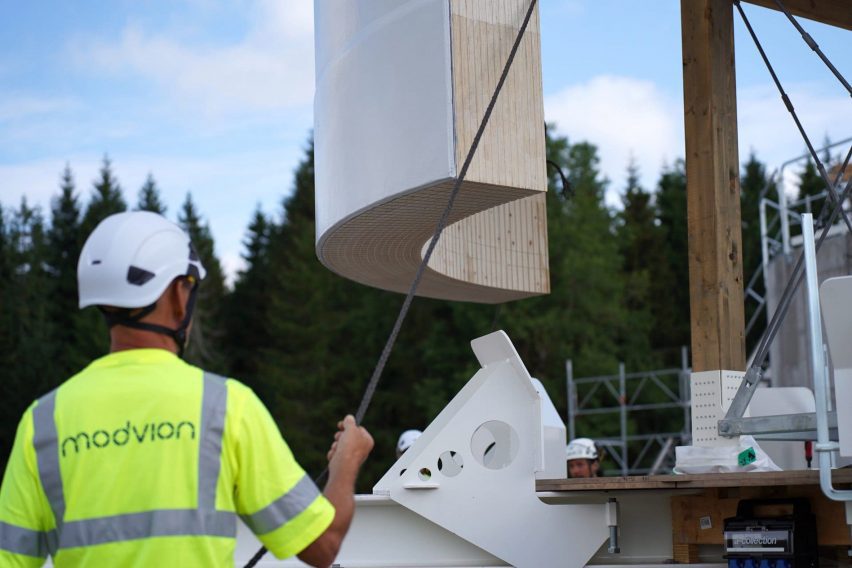
The Skara turbine has a capacity of two megawatts, which represents the maximum power output the turbine can achieve under ideal conditions. This is a bit lower than the average capacity for new turbines built in Europe.
On the outside, the tower has a thick white coating that makes it look similar to steel, and it’s rotor blades and generator hub, which are not supplied by Modvion, are made of conventional materials like fibreglass. This may change in the future, however, with another company, Voodin Blades, working on the technology for wooden blades.
Modvion was founded in 2016 by university peers David Olivegren and Otto Lundman. While its current focus is wind turbines, it is dedicated to wooden technology more broadly, and Hedlund told Dezeen that the team believes it has “the world’s strongest joint for timber construction”, which could also be put to other uses.
Another recent milestone for wind power came in the form of a wind-powered cargo ship, which had been retrofitted with two 37.5-metre-tall sails.